Best Practices for New Product Testing

A friendly user interface and simple menu make training faster and easier. Source: Com-Ten Industries
At some point, manufacturers will find themselves in this situation: they have to test their new product in manufacturing-the question is how to do it. What equipment should they choose? What is the best device to use to ensure good results? How can production be validated without getting the boss upset about the budget?
Just as processes that produce a product may vary, the process of obtaining measurements and data may have variation and produce defects. Operators should evaluate the test method, measuring instruments and the entire process of obtaining measurements to ensure the integrity of the data used for analysis and to evaluate the implications of measurement error for decisions made about the product or process.
So consider the following steps:
These steps will help keep measurement uncertainty under control and ensure a good job is done.
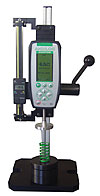
A spring tested with a manual test stand, a force gage, digital travel scale and self-leveling plate. Source: Com-Ten Industries
Select the Correct Measurement and Approach
First, back to the basics: say and write what needs to be accomplished.Quality management systems usually require full documentation of the procedures used in a test. It is vital for all interested parties to understand and agree on the methods of obtaining data and making measurements. It is common for a physical property such as force to be strongly affected by the method of testing and measuring so it is vital to fully document experiments and measurements and to provide needed definitions.
Using a standard test method, such as one published by a respected standards organization, is a good place to start. Nevertheless, sometimes it is more useful to modify an existing test method or to develop a new one. Again, documentation and full disclosure are necessary.
Then make an exact description of the specimens and test methods.
A well-written test method is important. However, even more important is choosing a method to measure the correct property or characteristic. Not all tests and measurements are equally useful. For example, if a manufactured item has several components, test methods may have several levels of connection:
Test methods often are scrutinized for validity, applicability or accuracy in a given context. For this reason, it is important that the scope of the test method be clearly defined and any aspect included in the scope is shown to be accurate and repeatable through validation.
Define the type of equipment with test parameters:
If using a norm or ASTM, do not forget the operator will follow the exact requirement of the standard.
These conditions will determine the type of machine needed, the maximum capacity, the testing space available and the displacement speed.
For the last step, define what value needs to be measured. Most of the time, the method only requires the peak force. Nevertheless, common results are break-force, first peak, peeling, friction, yield, modulus and elongation.
Electronic measuring device capabilities are important to the operator; all of the measuring devices have the capability to display the peak, but not all can display the break force, and very few can measure the peeling value without using a computer and software.
Only the most advanced test systems will display force vs. displacement in the same screen or a graph of the results.

Motorized test stands produce a constant test speed for good repeatability. Source: Com-Ten Industries
Assess the Measuring Device
Many parameters can influence the quality of the results and the quality of equipment.Measuring range: Range or continuous scale over which the test method is considered accurate. For example, it is recommended to measure between 10% and 90% of the full scale of the sensor.
Accuracy and precision: In force measurement, the accuracy will be 0.5% or 0.1% of full scale for the best instruments. This gives operators the ability to use the full range of the load cell and also will be an important issue regarding the total uncertainty calculation.
Measurement resolution: Electronic devices today have resolution better than 1/5,000, giving operators the finest reading, results and better repeatability.
Sampling rate: Generally unknown, sampling rate is a decisive factor for repeatability. When the device is reading 1,000 times per second from the load cell, operators have a very good chance the reading will catch the true peak; of course a slower rate of 60 times per second, for example, will have a very good chance of missing the true peak and giving inconsistent results.
Robustness or sensitivity to the test environment or setup: This may be difficult to control. Misalignment of the sample in the grips is a typical mistake.
Battery life: Such as the use of rechargeable batteries, for example. This provides freedom of equipment movement without a power supply or battery change.
Required calibrations: Calibration cannot be avoided, but can be easier if all the calibration data and parameters are saved with the load cell. In this case sending the load cell alone to be calibrated is useful and saves money-no on-site calibration or transportation of heavy equipment is necessary.

Appropriate fixtures improve the quality and repeatability of the results. Source: Com-Ten Industries
Assess Procedures & Operators
For the day-to-day process, how will the results be collected?The operator knows the samples, but they have to define a sampling plan, sample preparation and test fixtures. Having the grips provided with the equipment provides the advantage of having a grip that fits with the load cell (mounting conditions, tare weight and alignment). Certain equipment is designed with large testing space with threaded holes. This gives more flexibility for samples such as components or assemblies.
And if operators anticipate various tests requiring several types of grips, do not forget that a quick-disconnect connection saves time and energy when changing grips.
If possible, ask the manufacturer for a preliminary test to check that the sample will not slip inside or break in the grip.
Do not forget that measuring in compression requires good fixture alignment.
Now everything seems to be in place-but what about the operators? They are an important part of the total performance, and for them, ergonomics and safety is the main focus.
Attractive touch screens, user friendly menus, good operating manuals and easy-to-operate machines are well accepted and make training new employees easier than complex multi-parameter setups and step-by-step menus, even for high level operators.
Change of display languages is now available even on small force gages to help overcome possible language barriers.
Assess Any Measurement Interactions
The quality of the measurement will be affected by external factors such as humidity, temperature, vibration, electronic noise and static electricity.If these cannot be avoided, be sure the machine has been prepared to face such variations, particularly if it is out of normal industrial context.
Define the Data Analysis
What will be done with the results? Collecting the data will be the next step of the analysis. Will it just be noted in writing? More often, the values must be saved for traceability, reported to customers or used for further analysis. This can be done via a computer using RS232 connection, USB connections or with a memory card reader.The form of the final report can be a list of data or a complete graph.
As with all measuring equipment, the definition of a measuring device is a complete process and each step should be considered to be sure nothing is missed. This process should avoid the choice of inaccurate equipment and nonrepeatable results that will drive inappropriate decisions concerning manufactured products.
Even for basic testing a quick review of all these parameters will help save money, time and credibility. NDT
Standards That Can Help
Looking for a reprint of this article?
From high-res PDFs to custom plaques, order your copy today!