
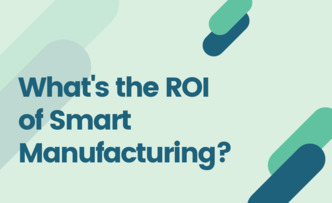
What’s the ROI of Smart Manufacturing?

A3 President Jeff Burnstein shares insights on the growing automation trend, highlighting advancements in humanoid robots and autonomous mobile technologies aimed at enhancing productivity and safety across industries.
Copyright ©2025. All Rights Reserved BNP Media.
Design, CMS, Hosting & Web Development :: ePublishing