Other Dimensions
Practical Checks on Measurements
Is there a way to improve calibration—without ramping up costs?
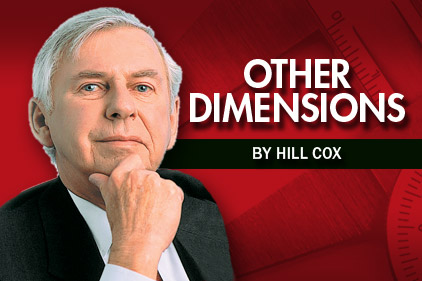
Many companies have their equipment calibrated on a regular basis and believe all will be well until they are calibrated again. Then the follow-up calibration shows one or two instruments were not able to perform up to expectations. Now what? A worse situation occurs when an instrument fails in service and suspect work is shipped and then discovered by the customer. This can happen because calibration deals with a situation at a fixed point in time. You could reduce this risk by calibrating instruments before and after each time they are used but that is not usually a practical consideration. And the effectiveness of it diminishes in proportion to the time between these two calibrations.
You have to remember that the calibration process deals with the instrument involved, not the measurements it produces. An instrument that passes the follow-up calibration could have been used in measurements that were out to lunch due to other factors. What other factors? Two culprits that come to mind are temperature variations or manipulative variations.
You have to remember that the calibration process deals with the instrument involved, not the measurements it produces. |
Yes, if you’re running a decent SPC process during production, it could flag the situation for you before damage is done. But what happens if you are not involved in the wonders of statistical control? Just as an inspector can be fooled by “readings” that look good, statistics could likewise be fooled by readings that look good but aren’t what they appear. If you rely on calibration only to avoid such problems you are taking what could become expensive risks.
Is there a way to make calibration more encompassing like statistical processing—without ramping up costs? The simple answer is yes. In fact, some measuring instruments, such as some air gages, provide the solution to the dilemma. Due to a couple of the factors that can cause them to drift, most makers of them recommend high and low limit masters as “check standards” to detect if this is occurring. We need only borrow a page from their book to solve our problem when traditional instruments such as micrometers and calipers are involved.
Unlike air gages, the check standards for general applications do not have to be as precise as long as they have been calibrated to a suitable level of precision and there are no geometrical irregularities such as roundness or taper that could give inconsistent readings.
In practice, the person taking the measurements takes some on the standards or masters along the way. The frequency of these checks could be every hour or after a specified number of workpiece measurements have been taken. This requires the masters to be at the location where the work is being done, i.e. the shop floor. This has the benefit of ensuring that temperature problems will not invalidate the results as the masters will vary in proportion to temperature swings just as the workpieces will. For this to hold, masters and the work being measured would have to be of the same material.
For optimum results, the master should be the same shape and size as the feature being measured. Round work requires the use of round masters such as setting discs or rings. Sometimes this is not a practical consideration and a workpiece known to be within tolerance can be used on a temporary basis. This has the added advantage that both master and work to be measured will be of the same material and both will react in the same way to temperature changes. Such masters should have the axis of the feature that was calibrated marked so variations in shape will not produce confusing numbers.
Properly made masters will eliminate a lot of these problems with the exception of temperature. To overcome this problem, engineering could indicate what the readings should be at different temperatures likely to be encountered in the shop. The inspector could adjust readings by referring to a chart of correction factors. An ongoing indication of the temperature at the workstation would be required. As an alternative, the tolerance on a critical part feature could be adjusted to account for known temperature risks.
The use of properly made masters from your gage supplier will be the easiest to work with and they don’t have to be super accurate as long as they are within linear expectoration (spitting distance) of the size you’re looking for.
Looking for a reprint of this article?
From high-res PDFs to custom plaques, order your copy today!