Ultrasonic Parts Washer
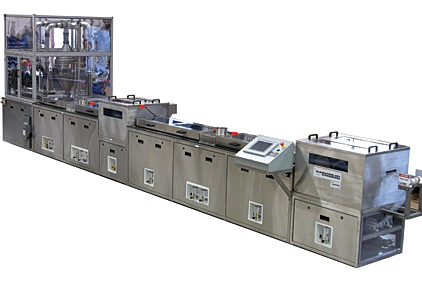
Blackstone-NEY CleanVeyor Ultrasonic parts washer utilizes a combination of spray, immersion, and ultrasonic cleaning technologies and has proven successful in achieving Six Sigma consistency in a number of applications requiring high production outputs and tight cleanliness levels. Parts with com-plex and internal geometries that need final cleaning prior to assembly are ideal candidates. This clean-ing process has proven to significantly reduce or eliminate warranty related failures that would be at-tributed to inadequate part cleaning. The Cleanveyor is modular so that more stages can be added as needed.
The first process in this powerful combination is a spray wash using a rotating brush module to quickly remove gross levels of contamination from parts. Higher pressures can be used to remove greater amounts of debris; however, the limitation of spray technology is that “line of sight” is required to be fully effective.
After scouring the external surfaces of the parts, the second process uses ultrasonic technology and is done in an immersion environment. The mechanical cleaning component of ultrasonics is the cavita-tion effect. Among nature’s most dramatic amplifiers of energy density, cavitation generates extreme local temperatures and pressures. The Cleanveyor can reduce chemical usage as much as five times
The CleanVeyor is available in three models, the CLV -8, CLV-16 and the CLV-24 and has a parts capacity from 600 to 1800 per hour. The CLV-8 comes standard with a single lane conveyor, and the CLV-16 has a two lane and the CLV-25 has a three lane. NDT
Cleaning Technologies Group
Looking for a reprint of this article?
From high-res PDFs to custom plaques, order your copy today!