The Price of Precision
Higher tolerance “insurance” comes with a price tag.
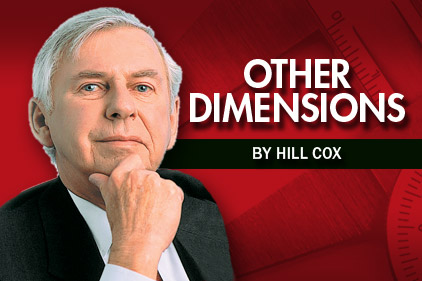
There’s an old rule of thumb among suppliers of precision gages that tighter tolerances mean higher prices. This is understandable considering the extra effort involved working within such boundaries. But not all gage users understand this. They want lower prices (always) but when the gage maker suggests that a more appropriate tolerance could result in cost savings, buyers tend to shy away. Having sold, manufactured and calibrated gages for over fifty years, these situations keep arising. I hope a look at the bigger picture may be useful.
The situation comes up quite often when the customer’s product indicates a gage tolerance of 0.000l inch, for example, but a tolerance of 0.00005 inch or less is specified. The tighter tolerance is called up as insurance because the person specifying the gage is not conversant with the process. And they usually don’t consider the implications of doing so further down the line.
There is a point where the tighter tolerance is of no benefit due to the temperature at the point of use. Or, the product being checked with it has surface finish or geometry variations that greatly exceed the tolerance such that the finer tolerance offers no inspection advantage.
Going back to the first paragraph of this rant, the biggest problem with this method of specifying gages is the higher cost of the higher tolerance. Every gage maker charges more for higher tolerances and rightly so since it does take more work to produce them and the risk of scrapping a gage in the process is much higher as well. But there are more costs involved.
Sooner or later, the gage will have to be calibrated after it has been in service for a while. The higher tolerance means there’s less material in the gage to wear out before it is no longer acceptable.
It will have to be calibrated more often than if it had been made to a more practical tolerance. Naturally, this means more expense during its useful life. But there’s another problem.
The higher tolerance gage will wear out of its specified tolerance and be rejected sooner than one made to the proper tolerance. This increases the cost of gaging that part feature.
Higher tolerance “insurance” comes with a price tag.
Another situation along similar lines comes up frequently where setting masters are concerned. Once more, excessively close tolerances are often called for when they are not needed. The same cost problems occur like those noted earlier. But there’s another problem in this case: the tolerances become so tight that rejection of the master when new can occur due to measurement uncertainty. Or the master could be accepted as new but rejected on calibration due to uncertainty when it has worn very little—if at all.
The purpose of a setting master is to give the device it will be used with a known starting point for measurements. In the case of high/low limit masters, they provide assurance the unit is performing reasonably accurately within a specified range.
In either case, it is not necessary for the masters to be made to super-accurate tolerances. The ideal is to know what their dimensions are to a high level of precision. Minor variations from the desired size or sizes are acceptable when you know what they are. Calibration provides the exact values they represent.
An example of this would be where a master is made to 50 micro-inches and the measuring instrument is set to the nominal value or zero. This means the setting could be off by 50 micro-inches. However, if the master was made to 100 micro-inches or 0.0001 inch but its calibrated value used, the most it would be off could be the uncertainty of the calibration or less than half that of the more accurately made master. All you have to do is put the actual value or variation from nominal into your setting as an offset.
Using this method, the original cost of the master(s) is lower, and since the tolerance is much larger, the master will be considered acceptable for a much longer time before replacement is needed. Higher accuracy at lower cost.
As you can see from these examples, a little bit of care in selecting gage or master tolerances can provide extra gage life, better accuracy and lower costs.
Hill Cox is president of Frank J. Cox Sales Ltd. (Brampton, Ontario, Canada). He may be reached at
Looking for a reprint of this article?
From high-res PDFs to custom plaques, order your copy today!