Other Dimensions
A Master
What Do You Expect Your Master To Do For You?
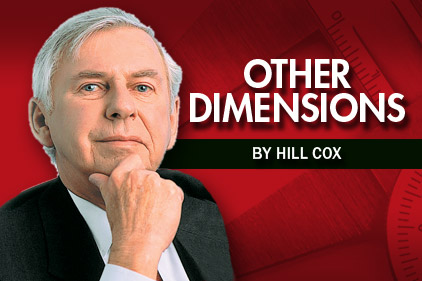
Nothing makes life easier than having a ‘master’ for the dimension(s) you have to measure. But a simple request for one with a dimension attached to it, for example, is not enough information to get something that will do what you want it to. Knowledgeable suppliers know that the term ‘master’ is generic in the broadest sense of the word and start asking so many questions it may seem that nothing is truly simple anymore. But it is in your best interests to answer those questions or you’ll end up with something that is more expensive than it needs to be or may not do what you want it to. The comments that follow will help you avoid these pitfalls.
What do you expect your master to do for you? The obvious answer is to provide a physical reference, but that’s not too enlightening. Is it being used to set a specific dimension for a measuring instrument? If the answer to this is yes, the next question that needs to be answered is: what kind of instrument? Often folks try to narrow things down by specifying they want a gage block to a special dimension so they get the most accurate master. The problem with this is the cost involved in providing a gage block to a special dimension, particularly when typical gage block tolerances are cited. And if the feature being measured is an outside diameter, a gage block may not be your best choice due to problems with instrument contact geometry. Some folks ask for a gage block and since they know it will be expensive, ask for it to be made from carbide or ceramics to increase its life. This will help where wear is a concern, but the increased cost of using these materials may not be worth it. Besides, temperature variations in use may negate the accuracy requested.
If the master you require is for setting a general purpose instrument such as an outside micrometer, they are made to standard dimensions in usually one inch or twenty five millimeter sizes. To differentiate such dedicated masters from others, they are usually referred to as setting rods or end standards. Yes, you can have similar items made to special dimensions if necessary.
When you are measuring inside diameters, the best ‘master’ for such applications is a setting ring and where some air gage systems are being used, high and low limit masters are required.
Threaded masters are often requested by customers and this means more questions. For example, is the master to be used for setting adjustable thread ring gages? If the answer is yes, you need a truncated style setting plug gage designed for that purpose. Conversely, if you are working to a foreign thread standard, you may require ‘wear check plugs’ for use with non-adjustable thread ring gages. This must be stipulated or you’ll get incorrect masters.
If the thread master you require is for setting thread comparators, this should be stated along with the thread details. Not to confuse the issue, but you’ll have to specify if it’s for use with a thread measuring micrometer, which uses a slightly different critter for the job. Alternatively, if you’re looking for thread masters to check fixed limit gages such as go/no-go plug gage members, there aren’t any threads to North American standards that follow such practices with the exception of some pipe threads.
The single greatest error in specifying masters is to ask for tolerances such as XX in some cases or even XXX in others. Not only are such tolerances expensive to achieve, often, they are not achievable in the real world when measurement uncertainty is figured into the equation.
Your lowest cost master will have a nominal tolerance but be calibrated to a finer one. All you have to do is make your instrument display the amount the master differs from the nominal value you are measuring and you are in business.
If you follow this approach to tolerance selection, you’ll save money because coarser tolerances are cheaper to produce. You’ll also have a longer working life for your master because it will stay within a coarser tolerance longer than a closer one. The only thing that will change appreciably will be its calibrated size and that won’t matter that much since you compensate for this when setting up your equipment to its most recently calibrated size.
Looking for a reprint of this article?
From high-res PDFs to custom plaques, order your copy today!