Keeping an Eye on Vision
IT’S A GOOD IDEA TO GET YOUR EYES CHECKED.
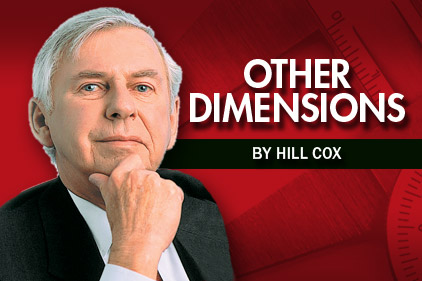
A friend in the industry contacted me recently for suggestions on dealing with a request from a customer of their calibration service requesting the results of vision tests on their lab people. It appears that their customer’s customer—a large aerospace company—has made this a mandatory requirement for all of their suppliers and any suppliers to them.
At first blush, it would seem to be an unnecessary requirement for a typical dimensional calibration facility where, if the staff couldn’t read the displays, especially the digital versions, they’d probably have trouble finding their way to work. Obviously, the request is quite reasonable where different types of optical instruments are in use and since optical comparators, optical flats and devices with Vernier scales etc. are used in dimensional work it could become an issue. Similarly, it could be argued that poor vision could impair the discernment of pointer position on analog displays.
If nothing else, a test such as this is good for new hires so you don’t have a bad experience to find out there’s a problem. Obviously, since our eyes tend to change as we get older, it is wise to check them frequently.
One method of dealing with this is to send everyone involved out for eye exams making sure the person doing the testing is aware of what is required in the workplace. Obviously, a proper eye examination by a registered professional will give the best overall results compared to the norm. But this can be quite expensive and disruptive and I don’t think it’s necessary for most situations. I believe a performance test can be an effective way to duplicate the working situation and give you information you can use right away.
Discoloration on thread gages can indicate a number of situations that would be overlooked if the inspector is color blind. So this is something that should be checked and is fairly easy to do. Take some sample chips from a paint store, stick them down on a piece of paper and label them. On their test paper, have each participant mark down the color of each from those listed. No, don’t use “summer beige” or other vague “designer” colors. Red, green, blue, brown, black, yellow and orange will prevent arguments.
Check general vision by providing instruments with a reading on them and have each participant list the displayed value on their sheet. This can include digital and analog type devices such as dial indicators and micrometers. Set up a reading on a Vernier scale such as those on older optical comparator protractor screens or a universal Vernier protractor or a Vernier caliper and see how accurately staff can read the values.
Set up an object that will provide a crisp image—such as a ball—on an optical comparator. Have the participant align its image with a line or point on the screen and zero the digital display. Back the edge of the image away from this and have the participant repeat this several times without being able to see the display. This is a situation encountered every time the comparator is used and the results can be interesting or in some cases, scary.
Unfortunately, most measurements using this device don’t provide a sharp image so the test is not always a reliable indicator of visual ability. The mechanics and measuring system on the comparator will also affect the results. To be fair and practical, such tests should use a feature your staff has to deal with on a day-to-day basis.
If your company uses specimens with various surface finish values for comparison purposes a test using them or even homemade examples that have been verified can help pick up any deficiencies in this area.
I must stipulate, once again, that the “tests” I’ve noted here are not the same as would be obtained by a professional examination. In some cases, they may be more informative because they will show the effect that a vision problem causes—if any. And, at the end of the day, that’s all you want to know isn’t it? Let the professional sort out why Charlie reads a 3 as an 8 or can’t see a scratch that looks like the Grand Canyon to everyone else.
Before your staff gets concerned because they wear glasses, do as we do: tell them that if they use eye glasses or a magnifying glass when doing their job, they should do so when tested. And they better do so all the time because we’ll be watching.
Looking for a reprint of this article?
From high-res PDFs to custom plaques, order your copy today!