When the Lab Says No
UNDERSTAND WHY THIS HAPPENS AND WHAT YOU CAN DO ABOUT IT.
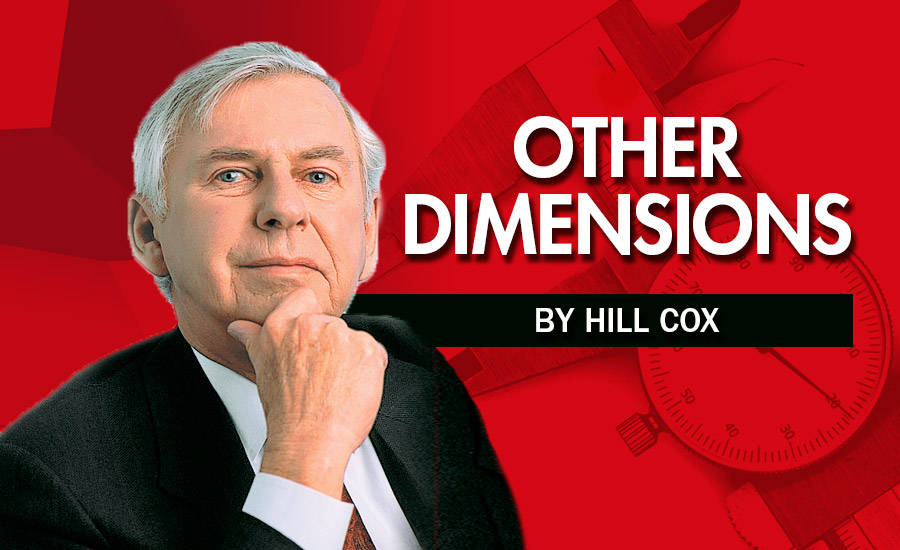
Like any other commercial enterprise, calibration laboratories cannot be all things to all people. Yes, it’s true that some think they can, but they eventually come unstuck when users of their data get into disputes and the opposing party had calibration from someone that knew what they were doing.
Most labs have capabilities to suit the range of work they are likely to encounter but every now and then they have to say ‘no’ to a request. Too often, the customer thinks they are making a big deal out of nothing because they don’t understand the implications implied by their request. The following notes may explain why you a get a ‘no’ from your calibration source—and what you can do about it as well.
Accredited or…
Agencies provide a scope of a capability for each lab they’ve accredited. If you require an accredited report but the item in question is beyond the range listed, the lab cannot provide one without risking the loss of their accreditation. One reason they don’t cover the range you require may be due to equipment limitations or, more likely, the cost of acquiring and maintaining the masters needed for limited use.
Labs may issue non-accredited reports to deal with such situations and often do so when the dimensions involved are only marginally outside those shown on their scope. Another method of dealing with this is to provide an accredited report of limited calibration that clearly states the actual range calibrated. This can work if the device you want calibrated isn’t used for its full range and it is labeled accordingly. In either case, they would seek your agreement on whichever approach you can live with.
Information overload
Many industry sectors want to have their own specifications when it comes to calibration rather than use the internationally accepted ISO 17025 standard. This has opened a Pandora’s Box of requirements—many of questionable merit—that add to the cost of the calibration. Typical of this is a small calibration job that requires nearly double the normal time to do because of the extra information required on the report by a particular standard.
Some labs will say ‘no’ to these extras or offer only some of them. Some may start adding a ‘documentation’ surcharge to cover the costs involved. If copies of calibration procedures are also requested, be prepared for a ‘no.’ After all, labs go through the hoops to become accredited so every customer doesn’t have to review their procedures and duplicate the ongoing checks by their accrediting agency.
Decision making
Many companies insist that a calibration report have all the data plus the tolerance of the gage or device in question and then ask the lab to decide if it’s satisfactory. What they rarely indicate is how good it has to be for their work since the specifications provided are usually for a new gage or instrument. And, of course, measurement uncertainty isn’t discussed. They’re asking the lab to stick its neck out for a judgment call based on iffy criteria and many will say ‘no’ to such a situation. The lab will do so because it realizes that the customer is looking for a scapegoat if something goes wrong. The customer should be making such decisions. See my October 2014 column for more details on this subject.
Custom gages
The items in question have been designed for a specific application and frequently do not have adequate documentation so the lab is on its own as to what exactly needs to be calibrated. They can guess and usually won’t be too far off the mark but many will say ‘no’ so they don’t have to waste a lot of time on engineering details and second-guesses from the customer.
Sending the lab a design drawing for a custom gage can be helpful but you would have to indicate what features you want data reported on. If the gage is little more than a modified item the lab is accredited for there may not be any problem, but if it is more than that, a ‘no’ is likely. A non-accredited report may be your only option.
Your final recourse in these situations is to shop around for a lab that is accredited for precisely the work you want done. If you are not successful, ask your quality registrar for help and if they can’t indicate an accredited source, they’ll have to concede the point and allow you to use a lab that is not accredited.
Looking for a reprint of this article?
From high-res PDFs to custom plaques, order your copy today!