Sinking in “Millionths”
DECIMALS PLACES IN SPECIFICATIONS ARE NOW AT WAR WITH DIGITAL DISPLAYS.
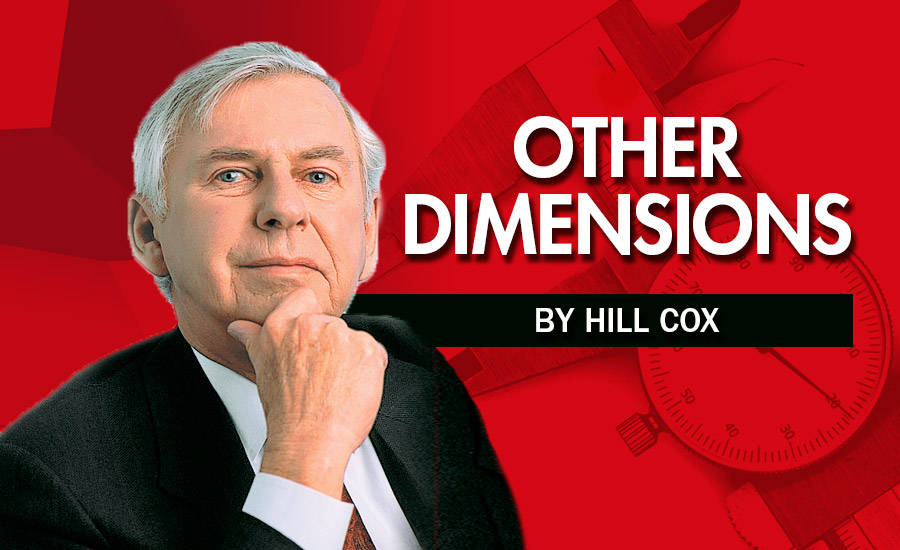
Some years ago I wrote about the ‘digital disease’ and how too many people actually believed digital displays with millionths of an inch resolution when the device they were part of could not deliver results worthy of the last few digits. Sadly, not too much has changed since then.
To make matters worse, decimal places in specifications are now at war with digital displays.
I used to think it was just me that wondered who really needs setting rings to XXX tolerance or even if such a thing was really possible. And then a faithful reader of this column reminded me that I am not alone—others in the industry share similar concerns.
An example of what I’m on about would be a plain ring gage say, .500” in diameter. If it is supposed to be to Class X tolerance, that amounts to 40 millionths of an inch. If it’s Class XX we’re looking at 20 millionths of an inch while Class XXX would amount to 10 millionths of an inch. Since this is a setting ring, the tolerance is split and applied bilaterally and becomes ±5 millionths, but let’s not get deeper than that for now.
If you were to get the good folks at NIST to calibrate that gage for you, their uncertainty would be a tad less than 5 millionths of an inch. Compare this to the XXX tolerance of 10 millionths, and you can easily see a 50% ratio overpowering the results. If you compare it to the split XXX tolerance of 5 millionths the uncertainty equals the tolerance on the gage.
This situation is not unusual when you start swimming in the sea of millionths due to state-of-the-art realities. Unfortunately, these realities are not always considered when tolerances are selected from a chart instead of being evaluated using the metrology required to get there.
You have to remember that the values I’ve noted earlier are based on NIST doing the measurements. When you get further down the food chain where most of us work, the ratios get worse.
The uncertainties involved are directly affected by the hardware typically used to take the measurements among other elements. They essentially fall into two general categories, short and long range comparators. On the short range side are high-resolution internal comparators that are set to gage block build-ups for each measured size. These may require physical manipulation of the ring being calibrated to ‘find’ the correct reading. Alternatively, universal length measuring machines designed for this type of work have long range capabilities and because of this, can be set with appropriately calibrated nominal size master rings so contact geometry does not play as significant a role as setting with gage blocks. Their performance is also better because they eliminate manual manipulation of the ring to find true diameters.
The calibration process is complicated by the fact that the specifications for plain ring gages list tolerances many assume are ‘normal’ for the industry supplying them. The origin of these tolerances is unknown to me but since they are reduced in steps of 50%, I am of the opinion that it was more a mathematical process than a metrology consideration. One thing is certain: measurement uncertainty was not contemplated or if it was, was probably a guesstimate.
The American Measuring Tool Manufacturers Association of Mentor, Ohio, is well aware of the problems I’ve noted, which is understandable since many of their member companies are manufacturers of plain ring gages. Round-robin studies conducted by the association indicate that plain ring gage calibration uncertainties are too high for tolerances better than Class X.
Perhaps the time has come for the related standards to drop the listings for unrealistic tolerances or post a notice to indicate they are not achievable at the commercial level. This would save a lot of arguments over measurements that few, if any, can prove are right or wrong.
If you believe you need those millionths of an inch, buy rings that are made to lower tolerances and have them calibrated to whatever level you want. Then preset your equipment with the calibrated values and you’re good to go. But don’t forget, those values will have measurement uncertainty attached to them that will have to be accounted for if you want to keep the corporate ship from sinking in a sea of millionths.
Looking for a reprint of this article?
From high-res PDFs to custom plaques, order your copy today!