Glass Transition Temperature of Polymeric Materials
Various laboratory techniques and how they relate to quality of data.

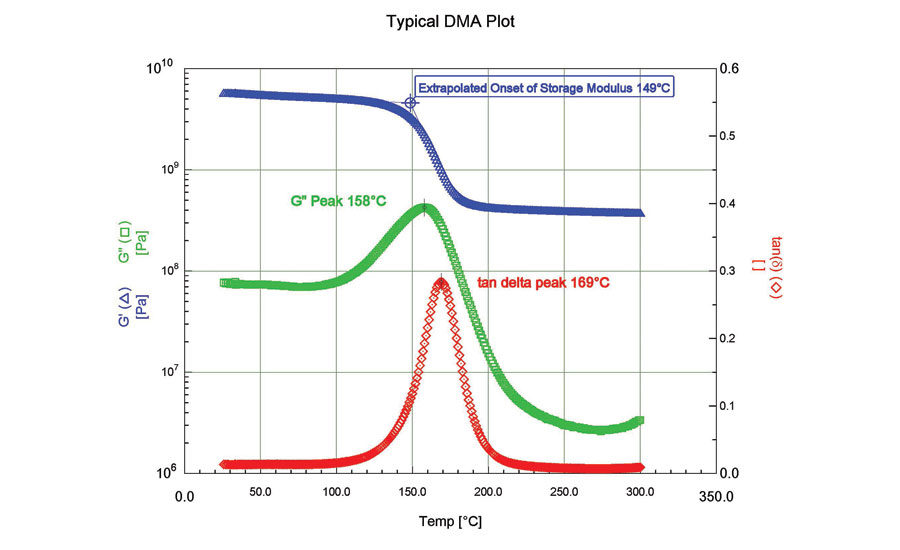






The thermal properties of polymeric materials are important to the function of components and assemblies that will operate in cold or warm environments. Glass Transition Temperature (referred herein as Tg) is the point at which a material goes from a hard brittle state to a soft rubbery state. Amorphous polymers only exhibit a Tg. Crystalline polymers exhibit a Tm (melt temperature) and typically a Tg since there is usually an amorphous portion as well (“semi”-crystalline). Identifying the Tg of polymers is of interest for various reasons, and is often used for quality control and research and development.
Three common techniques for measuring Tg:
1. Differential Scanning Calorimetry (DSC)– probably the most traditional and common technique for most polymeric materials. Simply stated, DSC utilizes a heat flow technique and compares the amount of heat supplied to the test sample and a similarly heated “reference” to determine transition points. Tg is typically calculated by using a half-height technique in the transition region. Depending on the equipment capability, DSC can be used for a wide range of thermoplastic and thermoset polymers.
2. Thermal Mechanical Analysis (TMA)– TMA is typically used to measure Coefficient of Thermal Expansion (CTE) of polymers. TMA uses a mechanical approach for measuring Tg. A sensitive probe measures the expansion of the test specimen when heated. From the expansion curve, a CTE can be calculated over a temperature range. If a material goes through a Tg during a TMA test, the curve shape changes significantly and Tg can be calculated by using an onset technique. There are also penetration probes that can be used on the TMA which is another approach that can be used for measuring Tg. In this case, a prescribed amount of force is placed on the test specimen using the penetration probe. As the temperature is increased, the probe will slowly begin to penetrate into the specimen and the temperature at which the probe penetrates into the specimen a certain distance would be considered the “softening point.” A significant change in the curve shape will indicate where the material could no longer support the probe and the Tg can be calculated.
3. Dynamic Mechanical Analysis (DMA) – DMA is probably the most sensitive technique (of the discussed methods) for Tg analysis. DMA measures the response of a material to an applied oscillatory strain (or stress), and how that response varies with temperature, frequency, or both. DMA is able to separate and measure the elastic and viscous components of polymers. How the material responds to the temperature increase can be illustrated by various means on the DMA graph. Compared to DSC, DMA can be 10 to 100 times more sensitive to the changes occurring at the Tg. DMA is useful for polymers with difficult to find Tgs such as epoxies, polymers with Tgs well below ambient temperature and highly crosslinked polymers.
Factors that affect Tg
For each of the techniques highlighted, various factors can affect Tg. For DSC, the heating rate and sample heat history are a couple of factors that may affect the test result. For materials that have broad Tgs, DSC may not be sensitive enough to show a large enough transition for accurate calculation purposes. For CTE, heating rate and probe force can affect the Tg.
For DMA, the variables that affect Tg are extensive. There are three typical approaches for calculating Tg by DMA. 1) Onset of the storage modulus curve, 2) Peak of the loss modulus curve and 3) Peak of the Tan Delta curve. All techniques are viable but may yield different results. There are also different modes of oscillation used for DMA such as torsional, single and dual cantilever, tension, compression and three-point bend. Various heating rates, frequencies and strains can be utilized as well. All of these variables can affect the Tg.
The use of Tg for quality control
All three techniques highlighted above are often used for quality control purposes. DSC is often used by laboratories (at resin manufacturing sites or contract laboratories) for common thermoplastic, amorphous materials such as Polycarbonate, PVC, ABS and Acrylic to name a few. On a regular basis, our organization uses TMA for the quality control of thermoset, composite materials for the aerospace industry. DMA is extensively used for quality control purposes for composite materials. Composite materials go through precise cure schedules to manipulate the physical and mechanical properties for the end application. Tg by DMA is a common test used to determine whether the material will perform as intended.
The quality and accuracy of the data produced by any of the means mentioned above is highly dependent upon the proper maintenance and calibration of the instrument being used.
Calibration, focus on DMA
A glass transition temperature result from a DMA test can vary significantly depending on how the test was performed and how the instrument was calibrated. There are many DMA standard test methods available such as ASTM, ISO, MIL, industry methods and customer-specific internal methods. Each of these methods may have slightly different parameters called out in them for the user to follow during testing. The typical test variables that can affect a DMA Tg result are: fixture type used (three-point bend, single cantilever, etc.), temperature heating rate, frequency, purge gas type and flow rate, material thermal diffusivity and thermocouple placement. Compound this with the fact that each of these methods may require (or allow) a different approach for the calibration of the equipment. Some of the methods state to follow the manufacturer’s recommendations (which again may be more than one approach), or refer the user to another ASTM method specific to DMA calibration. All of these variables can lead to significant differences in the Tg.
Even when it seems that a DMA test may have been performed per the same test method by different laboratories (or even within the same laboratory), the lack of consistent, standardized calibration procedures can cause much confusion when seemingly the same standard test methods were followed.
Proficiency, focus on DMA
Proficiency programs are available to participate in which can provide insight into how the data your lab is generating compares to other labs performing the same test. In the case of proficiency or round-robin type studies, detailed guidelines are provided to reduce as many variables as possible. Also, the use of Statistical Process Control (SPC) techniques or the use of traceable standards (NIST for example) utilized on a regular basis can ensure confidence and accuracy of data. If outsourcing of testing is your only option for obtaining Tg values, procuring a certified laboratory accredited in the test method you are testing to is the best approach.
A recent proficiency program our organization participated in for composite materials (organized by the Performance Review Institute) included the determination of Tg by DMA. A detailed, six page procedure, just on the temperature calibration was provided to ensure that all participating labs utilized the same exact calibration approach. The program went as far as providing calibration support bars to each lab so a material with the same thermal diffusivity was used. Efforts like this are what is needed in standard test methods to reduce as many variables as possible and to ensure accurate, quality test results.
Conclusion
There are various approaches to obtain Tg of polymeric materials. Sometimes trial and error has to be used to determine which technique is best. It is extremely important to know which technique and test parameters were used to determine Tg if comparing back to historical data. Similarly, if testing to a specification or industry standard, the technique and test parameters must be well defined. Even within a test technique, the means of obtaining the Tg can be performed various ways and the result can vary significantly. The Tg by DSC, TMA or DMA rarely will be the same and can vary by as much as 20°C or more! Tg by the various techniques is a proven quality control approach, but as discussed above, complacency and lack of diligence when it comes to understanding each approach can lead to serious consequences for research and development efforts or can lead to a misleading pass/fail assessment if trying to certify a material for quality control purposes.
Looking for a reprint of this article?
From high-res PDFs to custom plaques, order your copy today!