Solid Thread Ring Gage Realities
A CLOSER LOOK AT SOLID THREAD RING GAGE CALIBRATION.
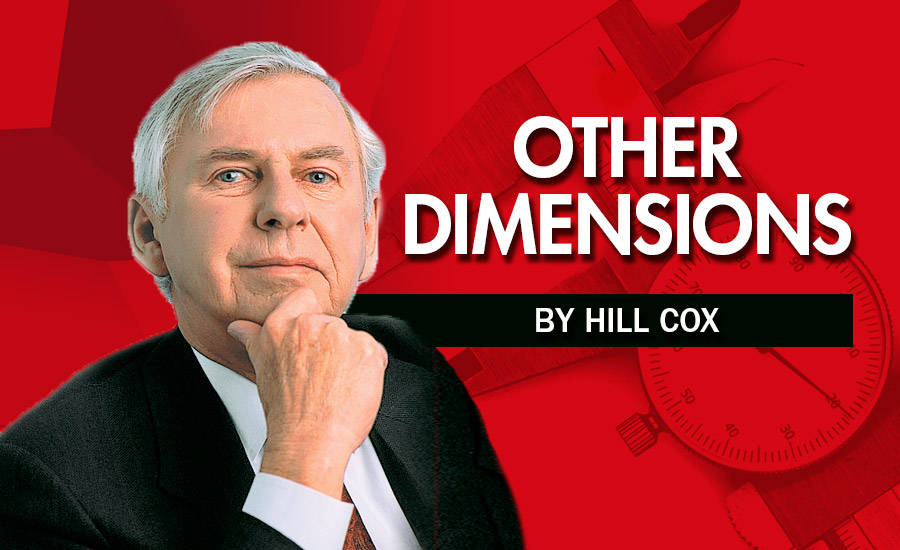
In my last column I beat up on the calibration of adjustable thread ring gages. Since I’m a nice guy, I thought it only fair that non-adjustable or solid thread ring gage calibration get similar treatment.
From time to time a customer will ask us to quote solid thread rings for standard threads due to problems being experienced with their adjustable counterparts. We are pleased to do so of course, but advise that their cost will be higher unless they are from unknown off-shore gage makers. And since they are rarely used in North America, they are not kept in stock. To make matter worse, masters to check them are rarely kept in stock by labs, making calibration of them a problem.
Proponents of solid rings will argue that they are a better gage because if they are made right they only need to be checked for wear while adjustable gage settings can sometimes be altered through rough handling or improper setting. Opponents will claim the solid rings made in other countries are not as accurate as their adjustable counterparts but they must be good enough or the countries that use them would not be able to build space stations and airplanes. What does make them more viable is the tolerances on the threads involved are typically greater than those we claim to meet.
Many of the problems encountered in the calibration of adjustable thread ring gages are common to solid ring calibration especially the differences that result when direct measurement of them is involved. In both cases, a simple pitch diameter measurement will not reflect the real functional diameter of the gage no matter how low the real or imagined uncertainty of the process is.
The Europeans frequently use ‘check plugs’ for the manufacture of their rings and the re-calibration of them. In other words, they have a go and no-go plug gage to check the go ring they are making and a similar set up for the no-go ring. They can do this because the tolerances on the rings are larger than ours. For many European specifications, all the rings need for re-calibration is a ‘wear’ plug for the go ring and one for the no-go ring. If these gages enter their respective ring it is worn to the point of being rejected.
A pitch diameter tolerance of .0003” is fairly common on the most popular sizes of thread rings to our specifications. The typical uncertainty in the measurement of pitch diameter is .0001” and has to be considered in determining the actual size of both the go and no-go check plugs if we were to use the same system here. You don’t have to be a math whiz to realize that too high a portion of the available tolerance on the ring will be lost to the uncertainty of the masters used.
Another problem I didn’t mention in my previous rant on this subject deals with measuring force. It can vary considerably between makers of devices generally used to measure thread rings.
And there’s still another problem involving the diameter of the ball contacts used for direct measurement. Too often the contact diameters are of European origins when supplied by the makers of universal length measuring machines. The wonders of software are used to adjust the readings to deal with U.S. threads but in doing so, it is assumed that the included angle of the thread is a nominal included angle but that is rarely the reality.
And speaking of software, it usually assumes the same formulae in working its wonders as used for determining the ‘over the wire’ measurement using thread wires. But, of course, a ball in a thread form does not work the same as a wire in the same situation.
Our gage tolerances are unusually close compared to the European specs. Whether we meet them in real terms is another story but whatever we’re doing, things seem to work out just fine. Similarly, the Europeans seem to get on with their lives with their specifications. If we don’t try to mix one spec with another, we should be able to coexist without difficulties.
Of course, there will probably be more arguments about gage sizes on our side than theirs.
CORRECTION: A reader advised me that I slipped an extra zero into my September column when referring to a major diameter tolerance. He is correct. It should have been .0005”.
Looking for a reprint of this article?
From high-res PDFs to custom plaques, order your copy today!