Software
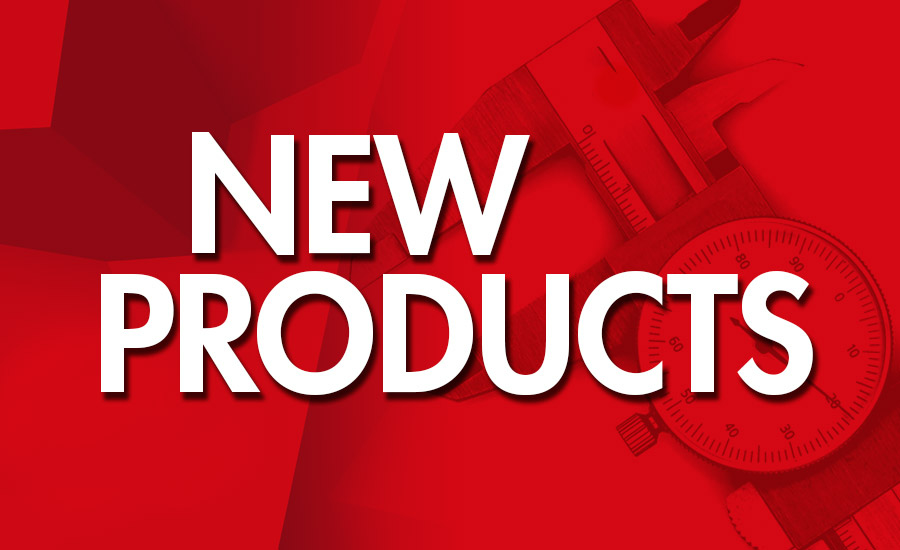
AICON 3D Systems launches a new version of the software platform BendingStudio. BendingStudio 3.0 offers many new features, which facilitate daily work in bending production. The software platform connects all data and processes around production of bended parts: from production and process planning to manufacturing and quality control. It is the only tool to meet and combine these requirements with emphasis on metrological processes.
With the revised control concept, AICON reacts to customer requirements. The software is even clearer structured and easier to handle. The set-up of inspection plans is separated from the measurements. The big advantage: The user sees only the information relevant for his task.
The new CAD-WIZARD enables the user to create bending elements for a bending machine from a component’s CAD data in IGES or STEP. Even complex data files can now be processed, and bending data are easily and reliably extracted. Even newcomers can handle this new function: The wizard guides the user through the process step by step. The set-up of new parts is integrated into the application “part editor”. This new arrangement optimizes measurement and analysis.
Besides the structural novelties, BendingStudio 3.0 offers extended measurement options. The connected measuring device, like AICON’s TubeInspect or MoveInspect, provides the measurement data, and BendingStudio carries out the analysis of the measured pipe. A wizard guides the user through the single steps of the bending point model. Usually, the analysis is automated. However, the user can step in when needed. Manual intervention is more transparent and graphically supported. In Reverse Engineering, different bending radii can easily be taken account of.
Furthermore, BendingStudio offers new options especially for very long and complex pipes with many bending points (e.g. long brake pipes). They can be measured with TubeInspect by overlapping repositioning section by section. The partial measurements are then combined. The user can either delete measurements or change the parameters of the analysis afterwards. If the overall measurement is not successful, new single measurements are added, defective measurements deleted or single measurements re-evaluated with changed parameters. This is especially useful if the part cannot be measured in a single step. It allows for an even more effective workflow, as the part does not have to be completely re-measured.
AICON 3D Systems GmbH
+49 (0)531 58 000 75
Looking for a reprint of this article?
From high-res PDFs to custom plaques, order your copy today!