Other Dimensions
Getting to the Root of the Problem
Don't Assume Resolution and Accuracy Are the Same Thing
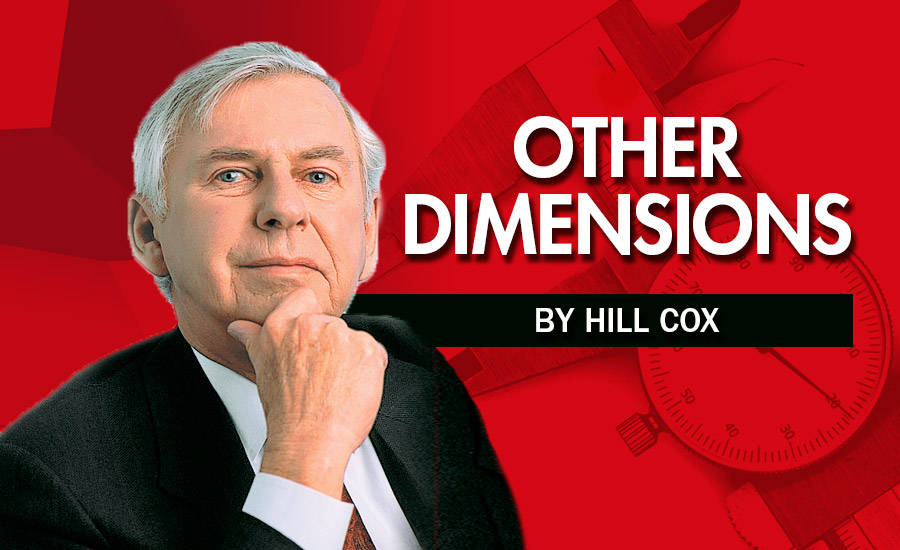
When things go off the rails quality professionals start a root cause analysis routine to determine what went wrong and why. This is a logical process of elimination until the culprit or culprits are identified. The hard part of the process is defining the cause when an instrument or gage is the primary suspect. The ‘fix’ part of it all comes easy, if it’s possible, but too often ‘fixes’ are tried before the cause has been accurately nailed down. When the analysis indicates gages or measuring instruments are at fault, sometimes basic assumptions are wrong—not the tools that provided the data. I’ll leave the overall concepts of the analysis to my colleagues on this publication that specialize in this area and focus on those ‘basic assumptions’ I mentioned.
The ‘assumed quality level’ regularly pops up when a new gage or instrument is used and starts rejecting parts. The first approach is to blame the new gage or instrument. Why? Because ‘we’ve been making these parts for years without any problems.’ The new device is often better than what it replaced and it is essentially indicating that while production may have been trouble-free the parts may have rarely, if ever, met the tolerances on the drawings. If the device these components are part of functions well, it means the specs need to be brought into alignment with reality. This usually means the drawing tolerances need to be opened up.
Poor GR&R results may generate an assumption that the instrument is defective. However the results may really indicate that the study was not properly conducted and the variation was caused by a failure to repeat the position(s) at which the measurement(s) were taken so component geometry becomes suspect. It could be that the GR&R requirement of say 10% is based on a desire instead of reality. In many situations, achieving this would require the parts in question to be measured in a laboratory setting using highly skilled inspectors and measuring instruments much more precise than those of the shop floor.
This is similar to the old 10:1 rule of thumb for gage or instrument selection. Essentially, it means an indicator’s resolution must be about 1/10th of the tolerance of the part feature it is checking. And the master it is set to would have to be 1/10th of that and the process used to qualify the master would have to be 1/10th of that... You can easily end up in millionths of an inch territory where anything that could negate a measurement will do just that. It is not uncommon for the ‘rule’ to be changed to something like 4:1 because of this. Sometimes the target ratio is beyond what the realities of dimensional metrology can provide so everyone has to go back to the drawing board.
When I’m asked to help with measurement problems, I always want to know the tolerances and the sizes involved. A popular assumption usually comes back: “It’s only a few thou,” which would seem to be an easy tolerance to work with. Until you find it is being applied to a ten-inch diameter.
Sometimes instruments and gages get a free ride because they’ve been calibrated and were determined to be ‘good to go.’ This is an assumption that may not hold up because the calibration was done improperly. Or the technician lacked the proper equipment to do so. Conversely, they may have been calibrated using masters that didn’t approximate the components being measured. Alternatively, the uncertainty of the calibration is ignored when it could explain why measurement differences mess up everyone’s day.
Too many people still assume an instrument’s resolution and its accuracy are the same thing. This is made worse with the widespread use of digital displays on equipment which encourages companies to put them in the hands of semi-skilled or even unskilled people who begin believing them. It’s not uncommon for errors in the instrument to be up to five times their resolution—or worse.
Temperature can be a big problem in dimensional measurement even in a shop with good temperature control. While the general environment is good, the temperature of parts fresh off the machine may be quite different and the errors magnified when the parts are of brass or aluminum while the instrument and its master are steel.
I assume this rant gives you some ideas that will help and leave you in peace to tear your hair out.
Looking for a reprint of this article?
From high-res PDFs to custom plaques, order your copy today!