It’s That Thread Ring Thing Again
The method shown in the standard will usually be the law.
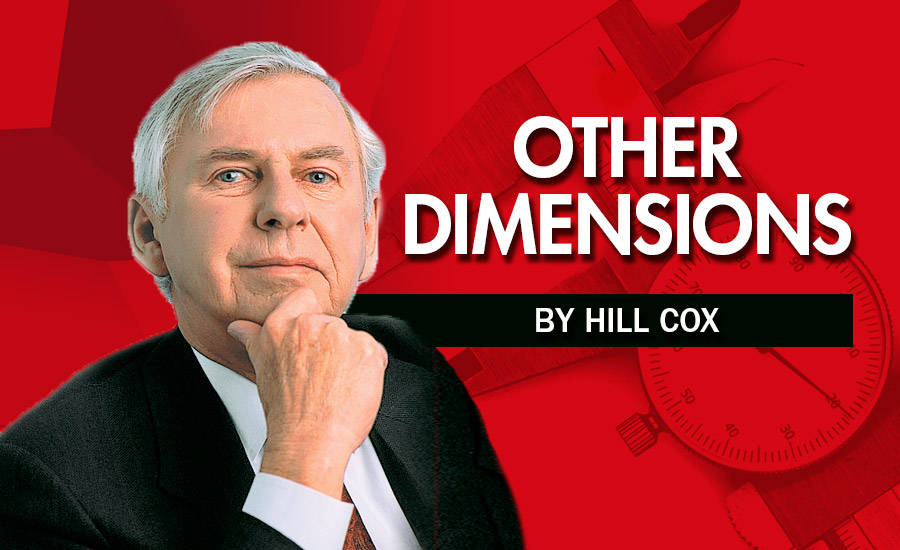
A reader emailed me after reading some of my rants on thread ring gages dealing with the problems that come up in their use and calibration. But he added another dimension to the problem since he is in the calibration business: How do the Europeans deal with their solid thread ring gages?
The short answer is that they have the same problems for the same reasons that we have. But they have an edge that we don’t. Let’s see if I can explain this properly.
Europeans have always preferred the solid thread ring gage over the adjustable type we use in North America. Their specifications usually include check plugs to verify their rings for making them and wear check plugs for determining when they are no longer considered suitable.
This means they have a go/no-go type plug gage to check the go ring for example. This easy to understand and use system is made possible by the fact that they have tolerances on the gages that are larger than American specifications and they also have a wear allowance on top of this which we do not have at this time. Their tolerances are not arranged the same way as ours which keeps things more interesting. This is the ‘edge’ they’ve got that I mentioned earlier.
Tolerances on thread gages to American specifications are there for the gage maker and are not considered wear allowances even though customers often ask that their gages be made to the high limit because they are using those limits as wear allowances.
Since our rings are adjustable, they can be checked using a setting plug made for the purpose but some labs don’t have the setting plugs required for standard gages which creates problems. Money enters the picture when special thread rings are being supplied because many customers don’t want to pay for them. Some gage makers will not supply specials unless the setting plugs are ordered with them while others try all kinds of tricks to get around the situation.
Some calibration labs try to skate around this lack of setting plugs by using direct measurement using a ULM which will not yield the same results and the same thing happens in Europe as well. Such measurements are usually for pitch diameter—a single part of the thread—which makes it a partial calibration compared to using plugs which envelope the whole thread. The pitch or lead of the thread could be out of tolerance and this condition would remain undetected by a single element measurement. Functionally, the thread will be smaller than indicated by this method which can cause all manner of mayhem.
Occasionally some bright spark will claim to solve this problem by measuring all of the individual features that make up the thread form and process the results with a formula of unknown origins. But few labs have the right hardware to provide an accurate measurement of pitch/lead or any way of determining the roundness of the thread which directly affects the thread size. With iffy data going in, it doesn’t matter how clever the formula is, the final answer won’t be worth having.
Of course, when you get to thread rings smaller than approximately 1/2’’ or 12mm, you have no choice in the matter as most ULMs don’t have probes that are small enough to do the job anyway.
Another advantage of using plugs is their simplicity in use and the fact that they will usually react the same as the ring in question to temperature differences from the ideal as long as they are allowed to climatize with the ring and you are careful handling them.
If you insist on using direct measurement the words ‘partial calibration’ should appear somewhere on the paperwork to alert the reader. If you offer this as a service outside of your organization, you should get an okay from your customer to save battles later. Because, when the dust settles, in case of dispute, the method shown in the standard the ring was made to will usually be the law.
Looking for a reprint of this article?
From high-res PDFs to custom plaques, order your copy today!