INDUSTRY HEADLINE
Norsk Titanium to Deliver the World’s First FAA-Approved, 3D-Printed, Structural Titanium Components to Boeing
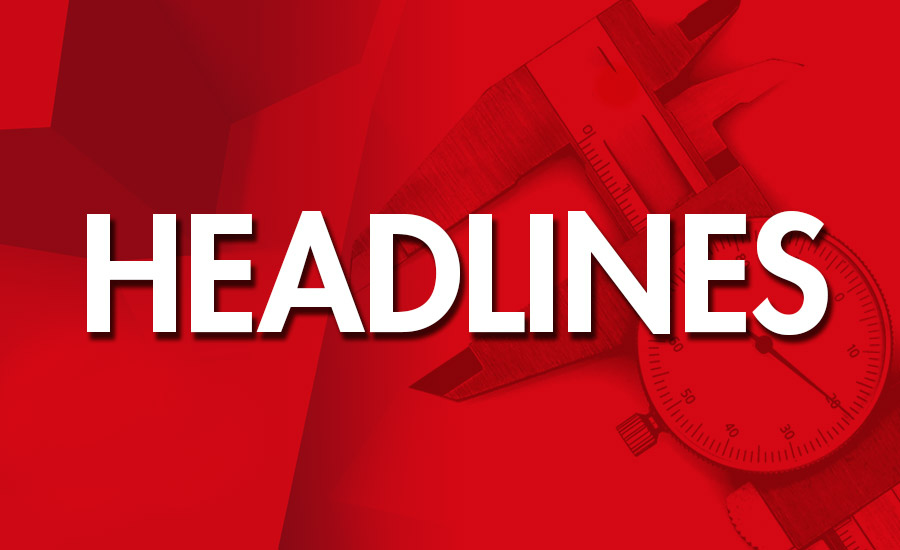
OSLO, NORWAY — Norsk Titanium AS, a supplier of additive-manufactured, structural titanium components received a production purchase order for 3D-printed structural titanium components from Boeing (NYSE: BA) that are being produced by Norsk’s proprietary Rapid Plasma Deposition process.
“We are proud to take this historical step with a great aerospace innovator like Boeing,” said Norsk Titanium President and Chief Executive Officer Warren M. Boley, Jr. “The Norsk Titanium team will continue to expand the portfolio of components supplied to Boeing meeting stringent certification requirements. It is an honor to earn FAA approval for these structural parts.”
Boeing designed the components and collaborated closely with Norsk Titanium throughout the development process. To certify these initial structural components on the Dreamliner, Boeing and Norsk Titanium undertook a rigorous testing program with FAA certification deliverables completed in February 2017. Norsk Titanium, with their wire-based RPD process, is the first supplier for Boeing’s high deposition rate material specification.
“From the outset, the 787 has been the hallmark of innovation and efficiency,” said John Byrne, vice president, airplane materials and structures, supplier management, Boeing Commercial Airplanes. “We are always looking at the latest technologies to drive cost reduction, performance and value to our customers and Norsk Titanium’s RPD capability fits the bill in a new and creative way.”
The Dreamliner RPD components will be on display at the International Paris Airshow, Le Bourget, June 19-25 at Norsk Titanium’s booth in Hall 1, Space H299, along with a full-scale mock-up of the company’s patented MERKE IV Rapid Plasma Deposition machine that produced the pioneering structural parts.
For more information, visit www.norsktitanium.com.
Looking for a reprint of this article?
From high-res PDFs to custom plaques, order your copy today!