The Pitch Mike Problem
It all starts with their name.
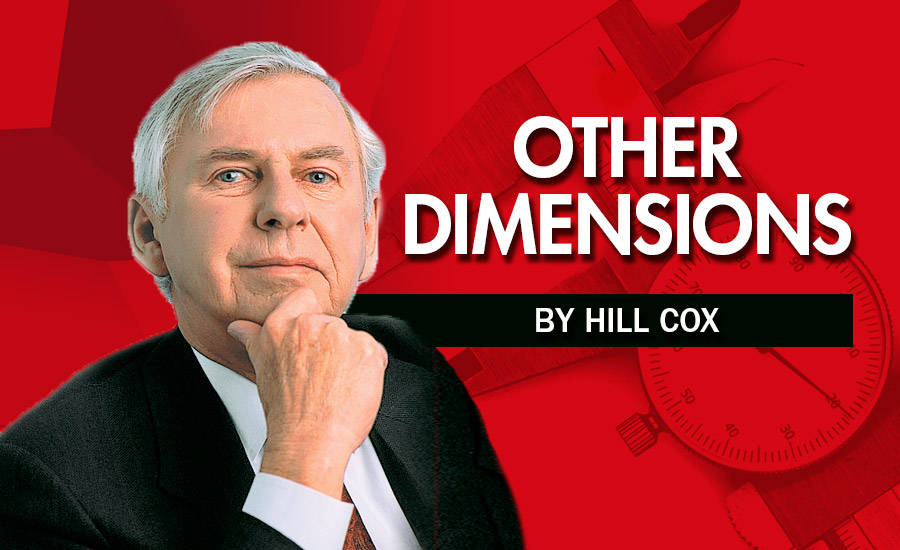
Anyone in the fastener or screw machine business producing screw threads is familiar with ‘pitch’ micrometers. These relatively simple devices are often used to set up production equipment and monitor their output, but there are many misconceptions about them which can call their usefulness into question. Problems arise when they are misapplied to various situations caused by the names they are known by and how they do what they do.
Problems that bring their value into question occur when there is an unacceptable spread in measurements between users or they indicate a screw thread is acceptable but other devices such as fixed limit gages reject them. A similar situation can arise when one type of this instrument says one thing while one of another type indicates something different and both of these are brought into question when a normal type of micrometer with thread wires is used to ‘measure’ a screw thread.
It all starts with their name.
The name ‘pitch’ micrometer is a bit of a misnomer when it comes to a screw thread because none of these instruments measure the ‘pitch’ of a thread. I suspect their common name is short for ‘pitch diameter’ but that can be a misnomer in its own right so let’s look at what they are and what they do.
Basic versions of these micrometers have a rear or fixed anvil with a 60-degree groove normal to the spindle axis while the end of the spindle is conical with the same included angle. When the spindle is closed to contact the groove in the angle, the instrument should read zero and it is then able to measure pitch diameter directly—at least that is what is claimed.
There are many thread pitches a given one inch or 25mm model is designed to cover such as 14 - 18 or 32 - 40 threads per inch (TPI). It was recognized early on that the anvils contact along the flanks of a thread rather that at a specific diameter only. This means errors caused by variations in thread form put the measurements into question, not to mention variations in actual linear pitch of a thread.
A change in design was put forward—I believe in Europe—to overcome this situation by having interchangeable contacts that can rotate about the spindle axis. This mediates some of these situations but only marginally. Astute readers (the kind that read my columns) will recognize that comparative readings between the use of thread wires (as recommended in ASME and other standards) to measure pitch diameter can never agree because the thread measuring wires locate in the thread groove while pitch micrometer vee anvils contact the thread flank but the conical spindle contacts between the thread flanks. While their form is relieved compared to their simpler version, they still contact thread flanks much more than thread wires.
You can reduce these variations by setting the thread micrometer to a thread plug gage’s calibrated pitch diameter size. Such a ‘master’ should be the same pitch of thread and approximately the same diameter as the one you intend on measuring. These days, most makers of these instruments recommend this procedure. However, remember that a pitch diameter measurement will not always agree with what fixed limit gages indicate a thread size is.
Another way to avoid these problems messing up your day is to use the micrometers for their intended purpose i.e.: a means to an end not the end itself. What this means is use the pitch mike to adjust your machines producing the threads and get you close to finished size but utilize a more effective and reliable method to qualify or accept the final product: thread ring gages in this case.
The reason for this is the micrometer is measuring a single thread element for better or worse while the thread ring gages account for far more of the elements that make up a screw thread and thus whether it will function properly.
Okay, I’m aware that some makers now decorate these instruments with digital displays which means even I can read their numbers but the basics of what those readings represent have not changed.
And, to answer the next most asked question regarding pitch mikes: the answer is NO! They are not suitable for thread plug gage calibration no matter how many decimal places you can read them to.
Looking for a reprint of this article?
From high-res PDFs to custom plaques, order your copy today!