Thread Ring Calibration Confusion
The problem is one that has plagued the industry for some time.
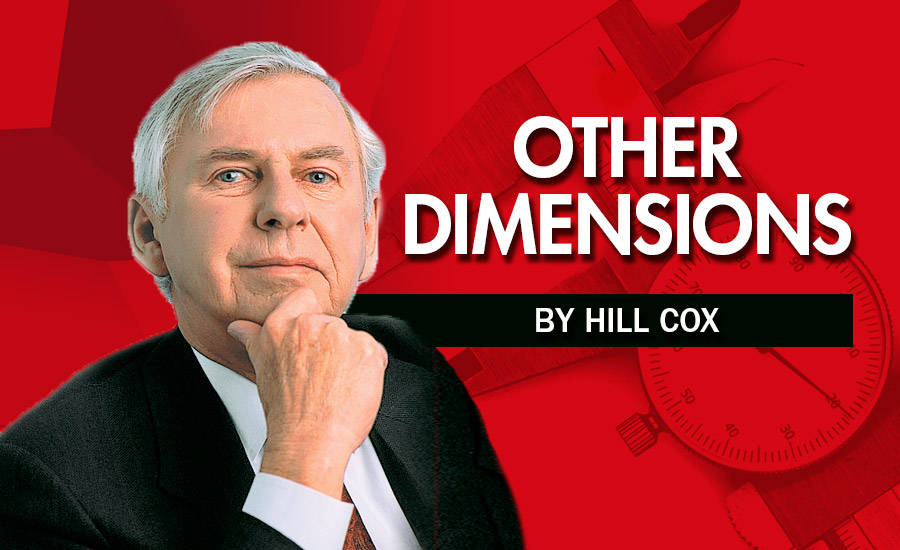
One would think that when you get your thread ring gages calibrated and there are no red flags raised by the reported data you’re good to go. Unfortunately, this sea of tranquility can end up drowning you if you have misinterpreted the reports—something that happens when disputes arise.
There are two key areas that put you at risk: how the gages were actually calibrated and how the results were reported. Most reports do not indicate the ‘how’ element and this can lead to incomplete reports. In some cases, reports are deliberately vague because the lab that issues them knows they are doing end runs around the standards involved.
Many of these situations arise when product is rejected by your customer’s gages even though your gages indicate the product is good. To make matters worse, both calibration reports from different labs indicate all the gages are within spec. Now what?
One way out of the problem is to get both rings checked by the same lab if you can agree on which one of the two involved shall be used. This could result in one set of rings being reported as out of spec when that is not the reality. This could occur due to different calibration methods being used.
The ASME standards that adjustable thread ring gages are made to are pretty straightforward. They require the use of a setting plug made for that purpose. If all the rings involved were set up on the same setting plug the arguments could be eliminated. However, some labs won’t invest in the setting plugs and they use direct measurement techniques to get around the issue. If your gages were properly set but your customer’s lab used direct measurement techniques, the odds are they will never agree, as I’ve outlined in earlier columns on this subject. But if the calibration report issued for the gages doesn’t outline how they were calibrated, you’ll never know.
This problem is one that has plagued the industry for some time but has now been addressed by my colleagues at the American Measuring Tool Manufacturers Association and the ASME committees that write the standards these gages are made to. The solution we have produced is a paper that is being sent to laboratory accrediting agencies offering guidance on how scopes of accreditation should show a laboratory’s capability when it comes to thread ring gages of any type.
Users of reports that follow our recommendations will know exactly how their rings have been calibrated and/or reset by breaking the methods down into two categories, one of which complies with the ASME standards using setting plugs. Other methods can be used but are ‘partial’ calibrations by comparison irrespective of how many dollars are spent on instrumentation and computers. My October 2015 column explains why.
Setting plug usage is not always reported by many calibration labs. Actual calibrated values for the setting plugs should be shown on the reports when they are used. Some labs using them simply report their specification size which means two setting plugs could meet spec but be several ten thousandths of an inch apart which leads to disputes all the time. Reporting the calibrated size of the setting plug at least gives the user a closer indication of the functional size of the plug that has been used in the process.
When you look at a laboratory’s scope and see an uncertainty value when setting plugs are used you’re looking at a guesstimate they can’t support with any meaningful documentation. Some of the uncertainties I have seen are so small they defy basic physics, mechanical engineering and precision metrology. Hopefully, the guesstimate is at least based on experience, but often that is not the case. The paper I mentioned earlier recognizes this and advises accrediting agencies to stop accepting such guesstimates.
Directly measuring pitch diameter on thread ring gages is a partial calibration method but the results will never agree with those obtained using setting plugs. And to make matters worse, all manner of devices are used for this approach, most of which are incapable of the accuracies or uncertainties claimed for them. Handheld instruments fall into this category but there are labs who swear by the readings obtained from them.
This is another area of precision dimensional calibration where knowledge of the calibration process can pay big dividends.
Looking for a reprint of this article?
From high-res PDFs to custom plaques, order your copy today!