High Precision Specialized Gage Blocks
How precise does this master you need have to be?
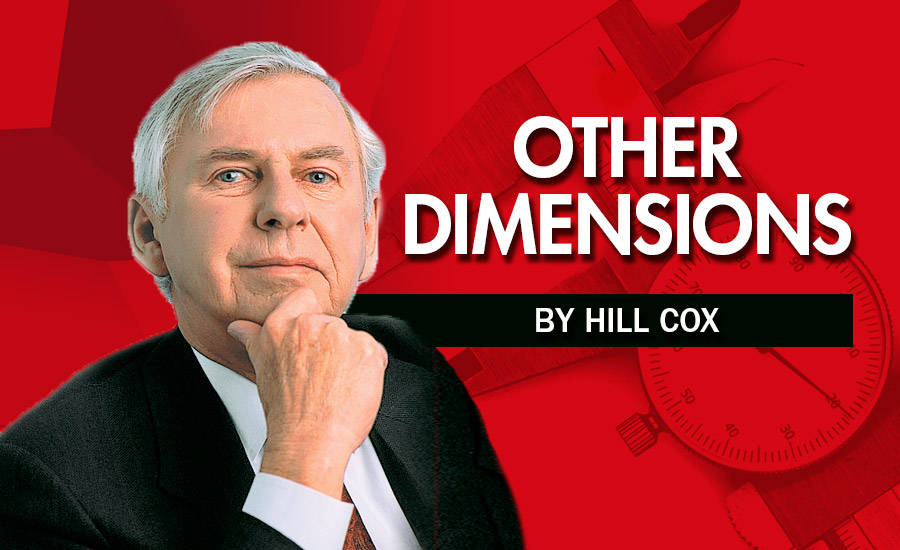
We are frequently asked to quote on gage blocks made to non-standard dimensions. Requests like this leads to a number of questions, the first question being why they are needed in the first place.
The answer would seem obvious: a very accurate master is required to set up a comparative measuring device that will be used in a production setting. Since gage blocks are the most popular representation of highly precise dimensional masters, they become the default request. But there is more to it all.
This brings up another question: Why don’t you use standard gage blocks wrung together to make up the dimension you need to save time and money? The answer usually forthcoming is that since the ‘master’ is to be used by semi-skilled operators who could break the build-up apart through handling, and they don’t have enough skill to wring them together. Suggestions that putting the buildup in a holder designed to keep them together become too technical to be considered.
The next question is obvious but the answer is not always thought out very well. It is: how precise does this master you need have to be? Answers to this question can range from Grade A or AA. In many cases, the answer stipulates no variation at all from the requested size which is stated to six decimal places. Asking about the temperature conditions it will be used in falls on deaf ears so a dose of monetary reality has to be administered at this point in the discussion.
Knowing that a standard gage block close to the desired size only costs say $50, for example, the assumption is that a specially made block might be double that or perhaps a bit more. Forgotten is the fact that standard size blocks are comparatively low in cost but to obtain this, they are made in large quantities not one at a time. This translates to a cost for a special size block being many times that of the standard block. This reality check sends the requester back to the drawing board to figure out a way to work around it.
An idea that is often floated to get a low cost special size gage block is to modify a standard block. Yes, any competent toolmaker can grind a gage block to another size at a low cost. Doing this defeats the purpose of having a gage block in the first place—especially a really precise one. As soon as you start grinding a gage block, all bets are off regarding accuracy, not to mention any warranty regarding stability, hardness and geometry that may have come with it before you started to rework it.
I know your toolmaker would be very careful and take light passes to avoid upsetting the status quo but we’re dealing with basic physics and metallurgy so this is not an option.
Another problem is: how are you going to calibrate this modified block? Most companies do not have facilities to do this and the people you send your blocks to for calibration may not be able to do it either. Why? Because most do one-on-one calibration so without a master block they cannot deliver the precision you think you need.
Yes, there are companies that actually manufacture gage blocks that have the equipment and expertise to do the job but they are few in number. If you find one willing to do a special size block for you, give them some application information and ask what level of precision in dimensional terms they can provide. This will save arguments later if you don’t get those ‘few’ millionths you’re seeking. All you have to do is be willing to spend the money and wait for it.
There is another way around this, of course. Talk with a gage making company and get them to advise what they can do for you and then have the end product calibrated to the high level of precision you’re seeking. It’s easier and cheaper to measure to millionths than make something to millionths. Armed with the calibrated size of your special block, you can set your equipment accordingly and you’re good to go.
Now, you can worry about the environment it will be used in, the state of the equipment you’re setting with it and the skill levels of those who will use it. Good luck with those details.
Looking for a reprint of this article?
From high-res PDFs to custom plaques, order your copy today!