Back to Basics: Six Sigma
A Six Sigma Master Black Belt provides an introduction to the methodology’s basic ideas and concepts.
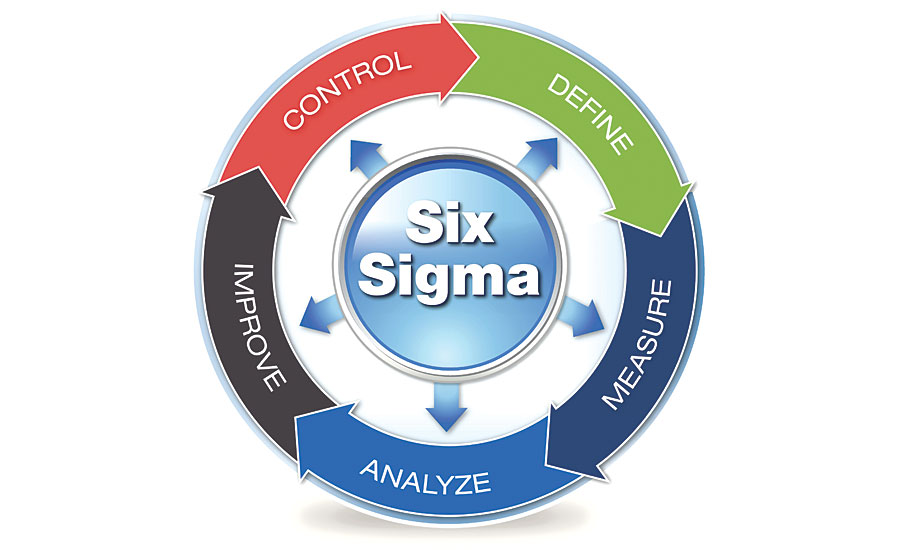
Don’t bite off more than you can chew, and really understand the methodology before attempting a large Six Sigma project. Those are the first words of advice for a Six Sigma novice from Six Sigma Master Black Belt John Vandenbemden.
“My suggestion is always go after something smaller to start with,” explains Vandenbemden, also an ASQ board member. “Help your team members understand how the tools work, how the methodology works. It also gives you a chance to identify which tools you prefer, so you can try different ones. Then go after a larger, more complex problem. Because if you start with a complex project and you get bogged down, or if it takes too long, or if people are looking for immediate results, many times it kills the program.”
Six Sigma was developed by Motorola in the 1980s as a methodology to systematically improve processes and eliminate defects by requiring all engineering requirements to fall within plus or minus six sigma from the process mean. The method was increasingly adopted in the U.S. as industry leaders such as G.E. implemented the system, and today it’s viewed as much as a management philosophy and culture as it is a strict methodology. Within Six Sigma, there are key procedures and methods to guide projects, such as DMAIC (Define, Measure, Analyze, Improve and Control).
For those just entering the manufacturing field or otherwise inexperienced with Six Sigma, Quality caught up with Vandenbemden to go over the key Six Sigma terms and ideas as a primer.
Quality Magazine: How should someone approach understanding Six Sigma?
John Vandenbemden: I think the very first thing is, they’ve got to have a commitment to want to make change. The DMAIC process is very well-defined, and it has history to show that it will work. But if the organization and the individuals involved are not committed to actually wanting to make change, then you know, having the best methodology isn’t going to work. But once you have that commitment, understanding the deliverables that need to be there for each of the DMAIC steps I think is critical.
QM: How do you explain the DMAIC (Define, Measure, Analyze, Improve and Control) steps?
Vandenbemden: In the Define stage, ask ‘Why do we want to do this project?’ We’ll build a business case: This is what it’s going to do and why people should support this. And then we’ll establish the goals. Then we’ll look at what type of team we need in order to accomplish this. Is this just in one department, or is this a problem that is more cross-functional? That creates the scope, boundaries and project definitions. And then we’ll supplement this with things like SIPOC (Suppliers, Inputs, Process, Outputs and Customers) so that we have an understanding of the playground we’re running in.
For Measure, we say, ‘Where are we today?’ That’s really the base, and that could be data. Ask, ‘Where am I?’
Analyze is looking at ‘Where should we be,’ compared to, ‘Where are we?’ I’m asking the question ‘Why?’ in analysis. ‘Why is this happening?’ And so analysis is really just addressing ‘why.’ It’s the same as in the 8D methodology, or any basic problem solving, it is to address the ‘why.’
Improve, now this is where it can be a little bit trickier. I need to go in and identify opportunities to attack the ‘why.’ So I create a bunch of potential solutions. I try to find the best one that fits for the financials, for the organization, for the goal we’re trying to achieve. This is also where I have to go and get buy-in [from the team members]. So before I even try anything, ‘Hey guys, here is what it is. Here’s the play that we have.’ And we’ll do a lot of experiments, or pilot runs, or trials, call it whatever you want. But after we determine what it could be, we’ll go out and run trials to see if the plan works. And if does work, we’re going to go into the final stage of Improve, into implementation. Now we do a lot of work (in this step). If I did a traditional Six Sigma project as a black belt, I might be here five or six months working on this project. I don’t want the problem to come back. I don’t want bad habits to pick back up. I want to make sure we understand what we did. So we have a phase called Control.
So Control is to prevent re-occurrence. Ask the question, ‘What do I need to do to put in some monitoring and measuring?’ We may need to rewrite procedures, we may put in some new technology, and we might have to do preventive maintenance. But control is trying to identify how to make this part of the everyday living, where I don’t think about this as change any longer, and instead think ‘This is just a way we’re going to do this. This is the method we’re going to follow every day from now on. This is how it works, and we don’t think about it as a change. This is just what we do. Here are our tools, here’s how we do it, and we just work them through that way.’ So that’s basically the DMAIC process.
QM: What are the different levels of Six Sigma certification?
Vandenbemden: You have four levels that could be certified in today’s world. There’s a level of just understanding the methodology, and that is what some people would call yellow belt certification. Where it just provides a certification that somebody kind of understands it as a team member. They can work in a team, and they understand the basics of what DMAIC is.
And then you’ve got your green belt, which means they do basic projects, smaller-scope, less intense. And then you’ve got your black belt. The green belt is doing it more part time, and a lot of times they don’t have the project management experience, versus somebody that might be a black belt has a little bit more experience in applying and managing projects or departments. Today, G.E., Allied Signal and several other organizations have created a level called a master black belt. And that’s changed quite a bit. In the old days, a master black belt had to really show that you could apply Six Sigma in several disciplines, and then you could train people and make people understand at a black belt level. Today, most of the certifications that are masters focuses on that they’re able to do a little bit of training, but the emphasis is more on their ability to do projects.
QM: How does someone earn Six Sigma certification?
Vandenbemden: ASQ has a full range of certifications, yellow all the way to master black belt. The criteria require a certain level of education or work experience. And then, as you go from green belt on up, you’re required to get someone to vouch for you that you completed a project or two. Then you take a test for knowledge. There are other independent, third-party certifications, as I used to do. For green belts I had a two-week training program. For black belts I had a four-week program, and my master black belt was about six months by the time that they did the training, did a couple projects, and took their test. Certification, the value of it is to the organization. It’s just like any other cert out there today, there are some companies where that’s the way in the door.
QM: What’s the difference between Lean and Six Sigma?
Vandenbemden: Personally, and this is just my own opinion, they’re both change methodologies. The Toyota (Lean) way is focused on efficiency, and Six Sigma primarily is focused on effectiveness. That’s why statistical analysis was highlighted on the Six Sigma world. So, at one point, if I was playing with something in efficiency, we threw it in the Lean box, if we were focused with data, then we focused on Six Sigma. And we kind of treated those as two worlds. Today, they’re more integrated. And many of the tools in Lean have been brought into the Six Sigma world.
QM: How has Six Sigma changed American manufacturing?
Vandenbemden: For those who have embraced it and continue to embrace it, it’s their basic problem solving tool. They will do their 8Ds, and when they have something that’s complex, they’ll run their continual improvement more from a Six Sigma type viewpoint. And that provides results that are consistent and a methodology that’s consistent. They’re reaping the benefits of the fact that people are now comfortable with that methodology. And it’s natural. It works when it isn’t just a methodology anymore; this is just the way we do it. And so those that benefit have taken it from, “You mean I gotta do it this way?” to, “Here’s how we do it.”
Looking for a reprint of this article?
From high-res PDFs to custom plaques, order your copy today!