Easily avoided situations regularly encountered by gage makers.
Error by design
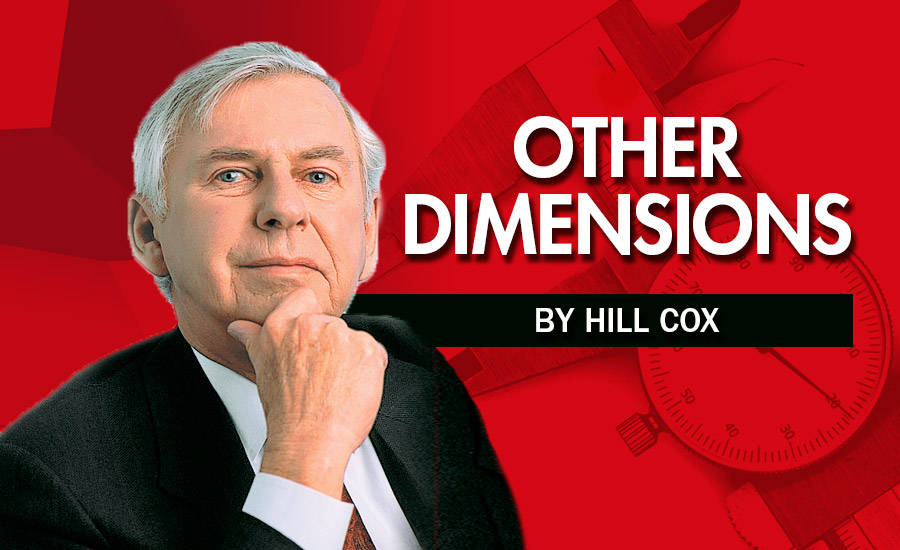
Nothing could be simpler than fixed limit gages which explains why they remain so popular. But nothing so simple can remain so when humans are involved. Someone always tries to mess things up by making simplicity complicated, ending up with a wide range of unintended consequences. The sort of thing governments the world over are known for.
The incentive behind this column is to help you avoid problems when designing special gages for the products your company produces. The following are situations that are easily avoided but regularly encountered by gage makers everywhere.
STANDARD DESIGNS
Despite what you may think, most gage designs have been covered one way or another by others and the results standardized in documents such as B47.1. Variations on these designs are often extended by gage makers to cover niche markets somewhere so your first choice should be to see what already exists before you start creating something ‘new’ that may not be new at all.
Standard designs allow you to start with a ‘blank’ that is produced in quantity to standardized dimensions and/or features which saves time and money. They frequently eliminate the need for a drawing since you only need to specify the type of gage and its critical dimensions.
ALL IN ONE
This situation arises when plug gages are required and the designer decides to keep things simple by making the gage out of one piece of metal. Simple it is, but costly since a special overall design is required. And since both go and no go elements and the handle are one piece, when the go wears out, everything else gets scrapped with it.
TWO FOR ONE
You’ve decided on a simple plug gage for the application but since a second hole behind the first one needs checking, you can be forgiven for thinking you could save gaging time by combining both in one. The problem with this ‘progressive’ style of gage is that only the one dimension can be checked in this way as the ‘no go’ part of the first gage section prevents the ‘go’ section of the second section from entering the work—unless the first section is way out of tolerance.
EXTENDED REACH
Plug gages, threaded or plain fall into this situation with expensive results being the only guarantee. Basically, the feature to be checked is only say, one inch long but it’s at the bottom of a two inch deep cavity. It’s not uncommon for the gage maker to be asked for a price on a gage with three inch (or more) long gage members to handle the problem.
This will work but the extra length of the gage members will drive the costs into the red ink department in short order. The easier way to deal with it is to buy standard length gage members with a low cost extension available for taperlock style plug gage handles.
TOLERANCES
All gage tolerances are derived from the tolerances on the component to be inspected and, if need be, moderated by how much of your manufacturing tolerance you’re ready to give up for the gage. Typically, five to 10% is a desirable compromise but often not achievable from a practical point of view. Some product tolerances are similar to gages so designing simple gages to check them is impossible. Manufacturing engineering and quality specialists should review these requirements before a lot of effort is wasted trying to bend physics and/or metrology out of shape.
Don’t clutter up your life with ‘sludge’ factors added to tolerances to cover for the unforeseen which has been common in the past. You’ll have enough problems dealing with known values.
A reminder is in order: If it’s a plug gage it will have a plus tolerance on the ‘go’ and a minus on the ‘no go.’ The reverse is the rule if it’s a ring gage.
With the global economy, it’s to be expected that gage designers will move around like products and what is the norm in one country may not be in another. Often that’s the reason some of the basics noted here are not as well-known as we might think.
The easy way out is to ask your gage supplier for a solution to your problem rather than a price for your solution of it. You’ll get the benefit of their expertise included at no extra cost.
Looking for a reprint of this article?
From high-res PDFs to custom plaques, order your copy today!