Calibration Intervals
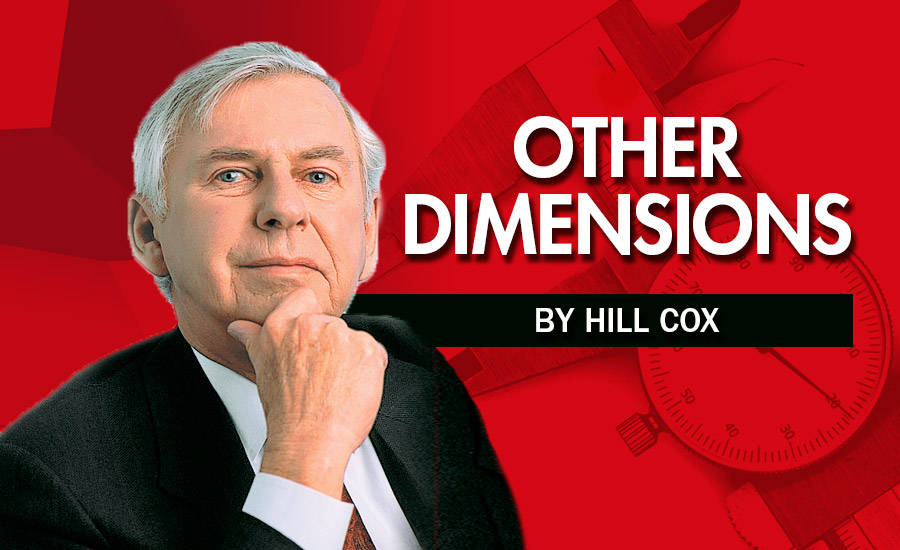
Establishing calibration intervals for gages and instruments is a tricky business, particularly if you’re starting from scratch. Calibration data, knowledge of metrology and experience come into play in this game so before we begin, let’s look at the goal we hope to achieve.
Reliable calibration intervals will ensure that the equipment you are using remains in a state of precision suitable for your work tolerances. Simply speaking, you are able to replace, repair or adjust before the gage or instrument is worn out or starts acting up enough to call your measurements or acceptance decisions into question.
The most common method of setting calibration intervals is based on time in use. In some cases, time is the guide whether the device is used or not. The advantage of this method is simplicity. Another method is to use the number of times the device is used but this method is more suited to production runs of the same items and requires some method of keeping track of usage.
Herewith some hints and things to look at so everything keeps on track whichever method is used.
The first order of business is to review previous calibration reports for a given item to see how well your current system is working. If things appear to be okay, will there be any changes to your operations that could mean changes to the intervals may be needed? This could include going from one shift a day usage to two shifts a day. If it’s the reverse of this, intervals could be lengthened. Changes to staff that are using a particular device could mean a shortened interval is worth considering until the new users prove they are as careful as those they replaced.
If your latest calibration reports show a gage is wearing close to acceptable limits, a shortening of the interval is suggested so you can ensure it is always within limit when you’re using it.
The ‘time’ method can be expensive when items are being recalibrated that haven’t been used during the latest cycle. One way around this is to seal gages in such a way that the fact they have been used since the last review is easily discerned—usually visually. As long as the seals remain intact, items bearing them don’t need to be calibrated as frequently as those in regular use. You can buy standard seals to do this job. They’re referred to as ‘tamper proof’ or ‘tamper evident’ labels. When someone tries to take them off, they break up into little bits and cannot be reused.
Another way to do this is to put a dab of nail polish at the front of a gage member so it has to be removed before the gage can be used. Any color will do of course, but you want to make sure it is easily seen. A quick visual check will show what items have been used and should be calibrated. This is particularly useful if you have sets containing dozens of gage pins to deal with.
Product design changes may incorporate tolerance changes that make a review of the hardware you’re using to verify them necessary. This could cause calibration intervals to be increased or decreased or alternatively mean a different device is required.
One way to reduce calibration costs and frequency is to review your acceptance limits for each type of device in your program. This is one of the most overlooked situations and is prevalent when fixed limit or go/no go gages are being used. Too often these limits are set to new gage tolerances which are there for the gage manufacturer. You can expand these limits to suit your work situation to save time and money.
One way to spot check your system without great expense is to use check standards. These can be specially made, but parts you have made that have been calibrated will suffice depending on your working tolerances. The inspector or machinist checks them from time to time or after an accident etc. to make sure things are still working. The device you are controlling is used to check them and if the same measurements are obtained each time, you can be reasonably assured nothing of significance has changed.
Looking for a reprint of this article?
From high-res PDFs to custom plaques, order your copy today!