INDUSTRY HEADLINE
Metrology for Additive Manufacturing to Come of Age
Currently, there’s not enough data for designers and manufacturers to accurately predict the performance of some additive-manufactured parts.
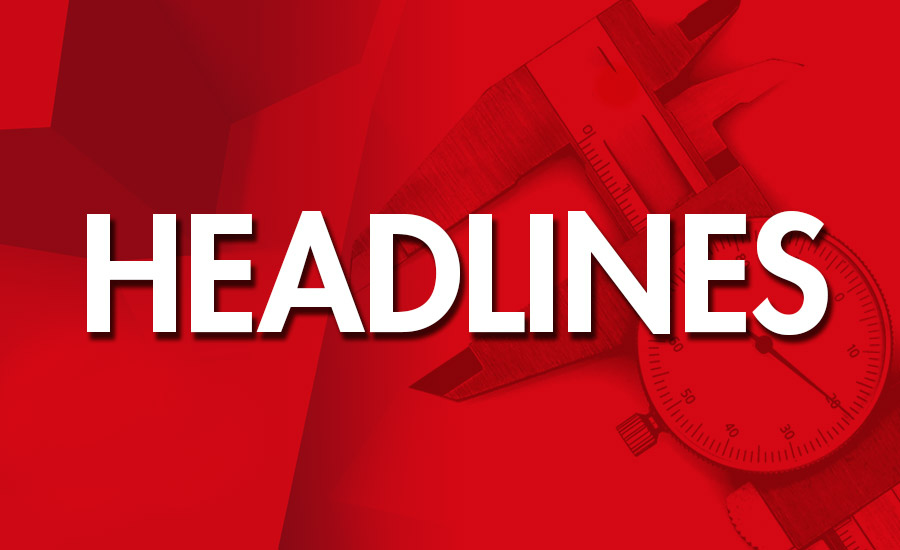
GAITHERSBURG, MD — NIST is helping additive manufacturing, often referred to as 3D printing, mature from a potentially disruptive technology into a widespread industrial capability.
NIST’s Material Measurement Lab contributes to the measurement methods, standards, data, and models required to realize the full promise of additive manufacturing, which frees designers to create novel shapes that are stronger and lighter and require less material and energy to make them. While the field is growing rapidly, with expected revenues from products and services to exceed $6.5 billion by 2019, there’s still a great deal of promise to be realized. Currently, there’s not enough data for designers and manufacturers to accurately predict the performance of some additive-manufactured parts, so it has not been widely adopted by the aerospace, biomedical, and automotive industries for parts where a failure of that component would result in the catastrophic loss of the whole structure.
The NIST Additive Manufacturing Benchmark Test Series (AM-Bench) engages multiple companies to build the same part using the same starting materials, while multiple computer modelers try to predict the finished parts’ chemical and physical properties, which NIST material science experts will measure. The final results will be available to any company to compare how their own modelling efforts perform against NIST’s data, providing them with a way to validate their additive manufacturing simulations and processes. More than 40 companies, national laboratories, and universities participate in AM-Bench; New builds, predictions, and tests will recur every two years. The robust simulation tools that result from AM-Bench will replace much of the current trial-and-error approach to making parts that perform as needed.
Forty-three companies, national labs, and universities are partnered with NIST’s AM-Bench. $4 billion can be saved each year by meeting the technical needs of the field.
Looking for a reprint of this article?
From high-res PDFs to custom plaques, order your copy today!