INDUSTRY HEADLINE
IMTS 2018 to Feature Wide Range of Additive Manufacturing Resources
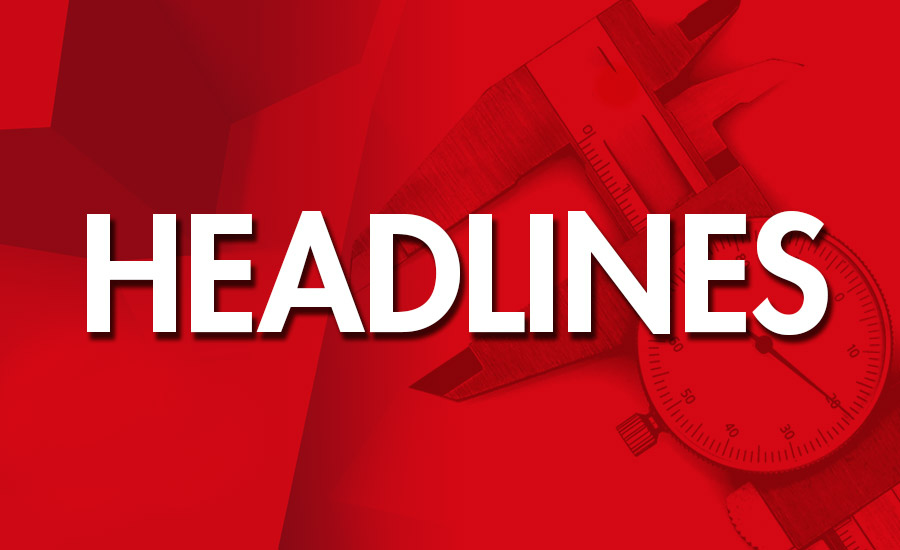
CHICAGO — Trying to analyze the state of additive manufacturing (AM) technology might feel like trying to assemble a jigsaw puzzle as the pieces are being set. Each player in this fast-moving arena presents a piece of the puzzle, and potential and current adopters have questions that range from as basic as choosing a material to as advanced as how to accurately confer properties on a molecular level.
“To obtain a true sense of what is possible today and, in the future, IMTS 2018 – The International Manufacturing Technology Show, offers an unprecedented concentration of additive manufacturing resources,” says Peter R. Eelman, vice president of exhibitions and business development at The Association For Manufacturing Technology, which owns and produces IMTS. “In such a short time, the history of IMTS has become synonymous with AM technology breakthroughs.”
At IMTS 2018, Eelman predicts that one of the hottest AM topics of discussion will be how to extend the digital thread from design through processing to final part.
Held Sept. 10-15 at Chicago's McCormick Place, the AM resources at IMTS include the Additive Manufacturing Pavilion and a second AMT's Emerging Technology Center focused strictly on additive manufacturing, both located at the entrance to the West Building in an expanded exhibit space. The AM Pavilion now boasts 56 exhibitors, up from 21 two years ago, plus several exhibitors in other Pavilions who will showcase additive-related technology.
During show years, IMTS hosts the Additive Manufacturing Conference presented by Gardner Business Media on Sept. 11-12 and the AppliedAM – Where Additive Minds Meet symposium presented by EOS North America on Sept. 12. In addition, at least six of the technical sessions presented as part of the IMTS Conference will focus on AM technology (view sessions list).
“IMTS is valuable for any company that wants to stay competitive,” says Glynn Fletcher, president of EOS North America. “Moving into production with additive manufacturing is a new experience for everybody. That's why we bring a large team of experts who know the technology and equipment, from engineers to service techs. There's no other place where you can have access to so many experts at one time. It's a truly unique experience.”
The theme for EOS' IMTS 2018 exhibit is an “Additive Mile” that takes visitors through the progressive steps of a journey in additive manufacturing: prototype, looking at material options, selecting and optimizing part design, scaling up, production, integration into a facility and ongoing service and upgrades.
New Trends
“Additive manufacturing is about solving the problem of high-cost, low-volume manufacturing,” says Ed Israel, president and co-founder of Plural Additive Manufacturing. “There's been a huge void in the marketplace for companies that couldn't afford the technology but would benefit from producing good prototype parts and serial manufactured parts using 3D printing. IMTS 2018 is the best place to learn how.”
Israel says that he thinks of Plural as an additive manufacturing integrator that works with customers to help them with any aspect of AM, from parts design all the way through high volume parts production. To help people find the right ways to apply AM, whether within an existing assembly or for new product development, Plural has developed a cost-per-part calculator.
“The big issue that will drive additive manufacturing is bringing cost per part down to a point where it can open up new markets, improve margins or accomplish other business objectives,” says Israel. “We can help companies determine whether additive has value before they invest in it.”
Glenn Redding, director of engineering for ESAB Welding & Cutting Products, agrees, saying that, “Additive manufacturing can be investigated and explore for unique applications and pain points for manufacturers dealing with high-mix/low-volume parts and who are driving for improved operational efficiencies.”
He notes that AM could help manufacturers provide additional resources to manage special requests from customers, respond faster by eliminating the need to produce tooling and do so without disrupting primary production capacity. In fact, many believe that today's fastest growing segment for AM, both polymer-based and metal-based, is for creating jigs, fixtures and other job aids that reduce cost and time-to-market.
“When people see how additive manufacturing fits with current operations and understand the symbiotic relationship between the additive and subtractive technologies, it gives them confidence to move forward,” says Eelman.
Ted Toth, senior technical advisor, Rosenberger North America, has attended every single IMTS since 1974. He says that, “from a job shop perspective, you can see additive as a threat or an opportunity. Job shops need to embrace and understand additive processes, so they can support post-process machining of metal additive products.”
Tooling Trends
“People are beginning to see that they can very quickly and locally print their own tooling and therefore increase the innovation and decrease the overall cycle time to develop that next big product,” states Bill Peter, director of the Manufacturing Demonstration Facility (MDF) at Oak Ridge National Laboratory (ORNL), a long-time collaborator with IMTS for creating demonstrations for the Emerging Technology Center.
Peter notes that the United States lost about 37% of the die and tool industry in less than a decade and currently imports 70-80% of its tools. Having demonstrated success with polymer molds, the MDF is now examining how to move forward with metal 3D printing.
“We want to look at cost-effective feed stocks and increase the deposition rate of additive systems that could make tools,” he says, noting that tooling greatly affects lead times and the cost and rate of innovation.
To directly address this point, Vader Systems will demonstrate its Magnet-o-Jet technology to melt and “jet” a continuous aluminum wire (e.g., no powder) to create metal parts. Vader has a partnership with the Rochester Institute of Technology, which is helping co-develop the technology and new materials, such as aerospace grades of aluminum that are traditionally non-weldable and difficult to print with other AM processes.
“I cannot overstate the rate of growth in AM technology,” says Jennifer Moran, director of sales and marketing for Vader Systems and four-time IMTS attendee. “At IMTS 2014, many people didn't understand basic concepts of AM. Now, people understand nuances between technology and want to discuss specific applications and materials. We bring the entire Vader team, from C-level executives to mechanical engineers, so people who have different levels of interest, from financial to technical in nature, can get answers and move forward.”
Software
In a snapshot, the industry has gone from using AM for prototyping, to building jigs and fixtures and finally to serial manufacture of end parts. It's a recommended path of technology adoption, as it helps companies become familiar in digestible increments. As companies move forward, however, they need to invest in AM-specific software.
“Originally, machines, materials and CAD/CAM software were made for prototyping. Now we need tools that are more robust to produce desirable, repeatable parts,” says Duann Scott, business development and strategy, additive for Autodesk. Scott explains that AM is an umbrella term for many different technologies and each technology has its own problems to solve.
“With our Nebfabb suite of additive manufacturing software, we can streamline workflow from design and optimization, preparation and simulation and then processing,” Scott says.
One of the issues that many users of AM grapple with is that they don't understand what happens during the build process, and that induces more trial and error time.
“What we're seeing in metal printing is that there's a lot of thermal distortion in the parts from the energy directed to the powder,” says Scott. “Autodesk software can simulate the build process and look for distortion, compensate and create successful prints for those parts.”
While Doug Dingus, Plural's director of service, has more than 20 years of CAD and related software experience, he will attend IMTS for the first time this year.
“Jumping into the additive manufacturing scene feels to me a lot like CAD did in the '90s,” he said. “If you look back at solid modeling and how it changed so many industries, this looks exactly the same way. AM is on the cusp of a big explosion. I think IMTS is the place to go, because that's where all the industry players will meet.”
With all the possibilities at IMTS 2018, “I believe the best way to accomplish your objectives is to have a plan going into the show,” says Jeff Holtzapple, business development manager, additive manufacturing, Morris Group, which represents Desktop Metal and other manufacturers. “I think if you use the MyShow Planner and make appointments with exhibitors, you'll have a much more successful time at IMTS.”
For more information, visit IMTS.com.
Looking for a reprint of this article?
From high-res PDFs to custom plaques, order your copy today!