Straight Talking: A Closer Look at Language Used in Calibration
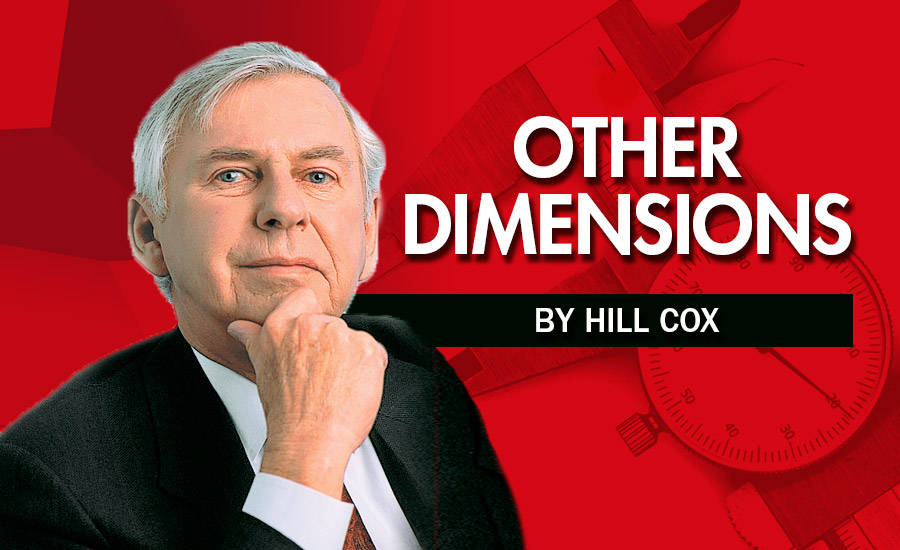
I’ve commented on this subject from time to time but thought I’d have another go at it since the questions never seem to go away. I’m referring to the language used in our day-to-day work in measurement and calibration.
Okay, I’ll admit I’m as bad as the next person when it comes to using slang but it’s so handy, which is why most people use it. It works as long as everyone understands what it means and therein lies the problem—not everyone does. Herewith some examples you may have run across with hopefully some clarifications.
Pitch Diameter, Simple Pitch Diameter, Effective Diameter, Vee-groove Diameter
As you’ve already guessed, these all relate to screw threads and the most common element of them that is gaged or measured: the pitch diameter. This one is made worse by the reality that it is an imaginary diameter halfway between the crest and root of a full thread form. Simple pitch diameter refers to a measurement of that diameter on its own as an isolated element and assumes that any other features that it encompasses are perfect and of no effect to this simple pitch diameter size.
The term Vee-groove diameter came into vogue some time back to prevent people from assuming it was something else but it means the same thing as simple pitch diameter. The Brits use the term effective pitch diameter when the simple pitch diameter reading of size is corrected to reflect the fact that the other elements of the thread that affect it are accounted for and the declared size reading adjusted accordingly.
When the pitch of a screw thread is more or less than perfect, it affects the functional size of the thread so that a bolt with a simple PD reading within tolerance may not get passed by thread ring gages because the effect of this makes it functionally larger.
To make your day more interesting, a drunken thread has the same effect and consequences but there is little AA can do to help you. What it means is the thread form does not follow a uniform helical path, something that is difficult to measure without special equipment designed for that purpose.
These are the reasons there are so many arguments over thread gage measurement using different types of measuring instruments or fixed limit gages and terminology.
Setting Rods, End Standards et al
As the name implies, end standards are physical representations of a dimension between their two end faces. The most common of these are gage blocks but there are others such as the setting rods used with micrometers over one inch or 25mm in capacity. Setting rods usually have flat parallel end faces but some have been made with spherical ends on them. There are sets of end standards that are about one inch/25mm diameter tubes that are very accurately made and can be screwed together to make up large dimensional masters. They can be used for setting micrometers as well. A common mistake in using the rods supplied with micrometers is to assume that by setting the micrometer with them you are calibrating the micrometer but you are not. You are simply giving it a reference or starting point for its measuring range. Calibration would require that you check several points over the range of the instrument to support the claim it has been calibrated.
Feeler, Feeler Gages
There are tools called feeler gages and if you don’t specify otherwise, you get a device which has a series of narrow thin steel leaves of varying thickness for checking small gaps such as those found on spark plugs. Today we have a lot of folks making gaging fixtures with reference pins or blocks on them a set distance from edges or other features of the component being checked. The nominal gap between the component and the pins is easily checked with a ‘feeler’ gage that could be specially designed for the application or, as is often the case, a typical go/no go plain cylindrical plug gage.
These simple gages can be a source of argument if you don’t specify the exact type of ‘feeler’ or ‘feeler gage’ you require. Failure to do so can leave you with a tool that is not suitable for the job or returnable and feeling miserable.
Looking for a reprint of this article?
From high-res PDFs to custom plaques, order your copy today!