Facing Reality, Part II
When measurement disputes arise, the finger pointing begins.
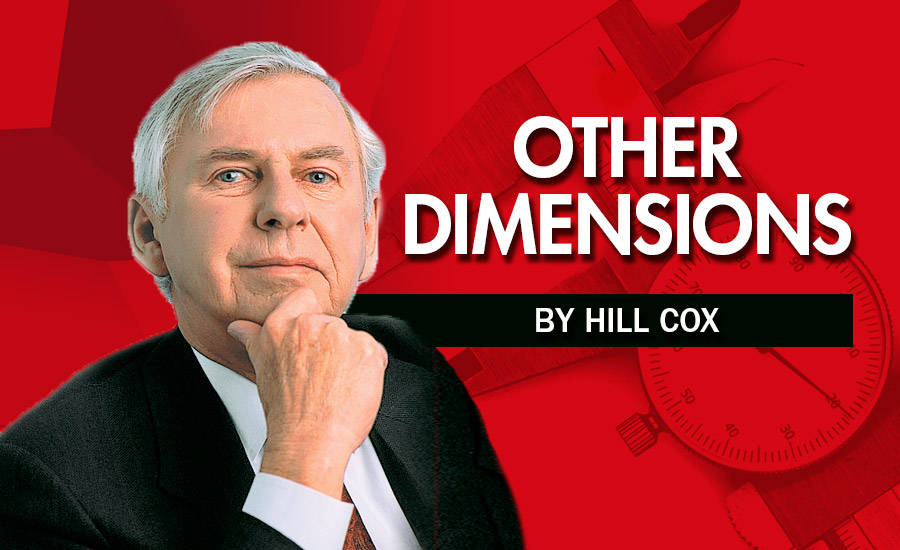
Measurement disputes over gage calibration continue despite the results of the studies noted in my previous column. As Jim Popovic, AMTMA’s managing director, put it when we were reviewing the results: “We still have people knocking their brains out over differences in readings of a few millionths of an inch. And we still have labs who believe their uncertainty for such measurements is “...a few millionths.”
Those who believe their capabilities are much better than noted in the previous column try to explain variations away by suggesting a slight difference in where the measurements are taken on the gage could cause a significant difference in the readings obtained, which is true. However, this possibility was foreseen and the gages were marked and a sketch provided to show where the measurements were to be taken. This procedure has been followed for all of the studies referred to.
Similar disparities exist when plain plug gage calibration results are reviewed. A .2185” plain plug gage was part of the package in the 2008-2009 AMTMA study the results of which were surprising to the inexperienced. The diameter readings ranged over .00017” or more. Interestingly, the claimed uncertainties—not including NIST—ranged from 5 to 27µ.” Some of this is due to the variety of contact configurations and measuring forces that were used by the participants.
One would expect that these numbers would change quite a bit when a plain ring gage of the same size was calibrated but they came out about the same. Perhaps this was due to greater care being taken with internal measurements or the skill level of those using such instruments was of a higher caliber. Despite this, the claimed uncertainties for the internal measurements were lower rather than higher than for a plug gage, ranging from 6µ” to 17µ.” NIST’s uncertainty for the plain ring was approximately 5µ.”
The Calibration Twilight Zone
This level of calibration could be considered a twilight zone due to the wide variations in calibration results. A zone where you can expect measurement disputes while millionths of an inch fade into the mist from a relevance point of view and the word ‘iffy’ takes on a new meaning.
To avoid getting lost in the zone, avoid plain plug gages with tolerances closer than XX, plain ring gages claiming to be better than Class X and thread plug gages closer than Class X. If, for some reason, you can’t avoid being trapped in the zone, you may be able to get around it by accepting reality and then making some compromises. This will entail a meeting with the gage maker and your calibration source whether it’s an independent or an in-house facility.
A review of the relevant verified measurement uncertainties is the place to start followed by deciding on how those uncertainties will be applied unless you agree to ignore them. A bad choice at the best of times but when you’re out in space, all bets are off. Sooner or later the participants will have to agree on who’s readings will be the benchmark. If you can’t decide on this, there is one outfit that is internationally recognized as providing the ultimate answer: NIST. Everyone else is a few steps down the food chain.
Hardware or Humans?
When measurement disputes arise the finger pointing begins. There is no doubt that the human factors loom large in these situations. Lack of skill or knowledge has a noticeable impact from selecting the wrong equipment for the task at hand or using the right equipment the wrong way. Too often people believe the last digit in a display because they have no sense or ‘feel’ as to what a millionth of an inch actually is. Too many confuse repeatability with measurement uncertainty.
Not all problems are due to human skills however. There are a number of mechanical reasons why there can be such a range of measurements of the same artifact. They include:
- Variation in measurement force
- Manual manipulation of the gage opposed to equipment with devices to do so
- Different contact shapes and/or deformation when used
- Condition of the equipment
- Poor quality setting masters
- Temperature differences between master, gage and equipment
- Inadequate instrumentation
In part three of this series, I’ll look at a common source of problems these studies reveal.
Looking for a reprint of this article?
From high-res PDFs to custom plaques, order your copy today!