Intelligent Imaging and Accurate Color Measurement in Automobiles
Color control in industrial production is critical in ensuring a quality product.

This image shows the Spectral Angle Mapper classification of paint samples, demonstrating detection of the differences between otherwise indistinguishable pairs of greens (capital green and gypsy teal). The sample as they would appear to the human eye are in the bottom right corner.
The automotive industry depends on consistency and predictability. From the color of the paint to the stiffness of the brake, car manufacturers devote significant amounts of time and money into making sure their products look immaculate and feel safe to drive. For an industry that is often on the cutting edge of automation technology in its manufacturing practices, many brands still rely on traditional systems and processes. Investment in better practices is necessary to improve upon current assessment methods. Hyperspectral imaging is one technology that has the potential to significantly impact color quality assurance in automobile production.
When it comes to shoppers, the color of an automobile is usually at the top of their request list. That is why color is a key component of a car’s value. It’s also why color control in industrial production is a critical function in ensuring a quality product. The development of more sophisticated paints and pigments in the automotive industry has presented manufacturers with new challenges for ensuring trueness to specification, consistency, and uniformity.
To ensure a consistent and vibrant look, mixture stage and post-application processes must be closely monitored to make sure the end result is acceptable to consumers. Until now, most conventional, automated technologies have provided an incomplete assessment, limited to averaged measurements from small test areas at different points around the automobile. To provide a more complete picture, manufacturers often expand these measurements to include different viewing angles and lighting conditions. However, this only gives a limited overview of the overall paint quality.
For many decades, human observers or simple tristimulus filter spot imaging instruments were the only tools available for automobile color measurement. Tristimulus filter devices utilized color filters paired to photodetectors to take spot measurements of a given sample. However, filters can only approximate the eye’s color response, have angular dependence, and deteriorate over time. Human assessment, of course, is impossible to completely standardize and objectify.
Multispectral systems, like those based upon patterned filter arrays, offer a slightly more expansive tool. These are an extension of color cameras where the typical Bayer or RGB filters overlaid on the image sensor are replaced with an array of 16 or more color filters. While no user alignment is needed and imagers can be miniaturized, the spectral resolution is limited and comes at the expense of spatial resolution, making this technology inadequate for many critical sample analysis applications.
Other alternatives adapted to color measurement, including spectrocolorimeters, spectroradiometers, and spectrometers, were first introduced into the automobile industry in the 1970s. At the time, they were cutting-edge, affordable, and offered the ability to perform more precise and accurate color measurements. However, such instruments are still only capable of spot measurements unless physically scanned across the sample area with the aid of stages or robotic arms. This renders an evaluation of spatial dependence of characteristics such as color uniformity difficult, time-consuming, and expensive.
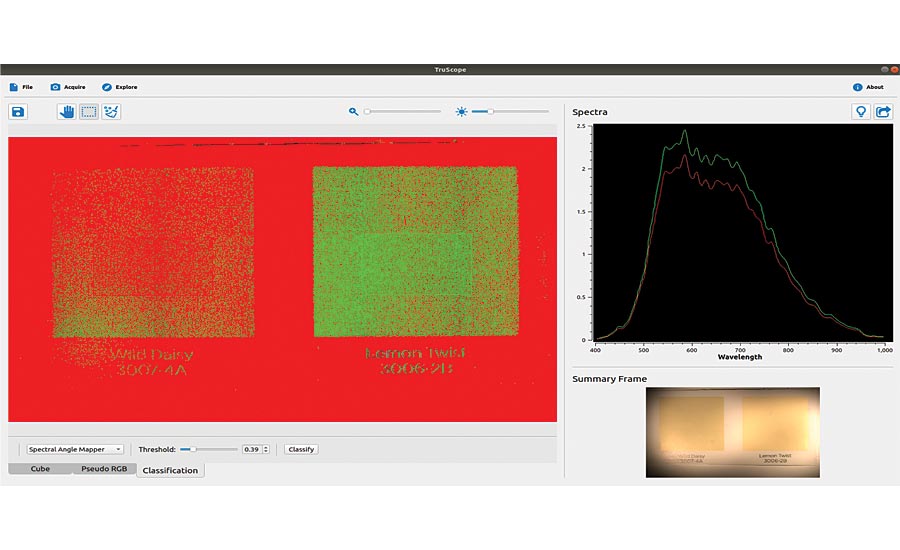
This image shows the Spectral Angle Mapper classification of paint samples, demonstrating detection of the differences between otherwise indistinguishable pairs of yellows (wild daisy and lemon twist). The sample as they would appear to the human eye are in the bottom right corner.
Hyperspectral imaging offers a solution that combines the advantages of imaging colorimeters that capture entire areas in a single measurement with the accuracy of a spectroradiometer. It achieves this by utilizing superior capabilities in two major areas—spectral and spatial resolution—to deliver a level of detail far beyond current automobile industry-standard instruments. By contrast, an RGB camera can see only three colors: red, green, and blue. Hyperspectral “intelligent imaging” can detect between 300-600 real colors: 100-200 times more colors than detected by standard RGB cameras.
Essentially, hyperspectral cameras work by generating “data-cubes,” which is where the spectrum at each pixel in the image is collected. Subtle reflected color differences that are not easily observable by the human eye and not all by RGB cameras are immediately identifiable by comparing the spectra between pixels.
Imaging technology can easily be configured into form factors and arrangements suitable for laboratory bench-top investigations or production line testing. These include assessing color on both the outside and inside of an automobile, from the paint and coating to molded plastics, lighting, lamps, dashboards, glass, and more. Intelligent imaging can also be used to assess high-tech LED dashboards, which are essentially flat-screen TVs mounted inside an automobile.
Because intelligent imaging systems can analyze a large area instead of just a small portion, it can efficiently detect anomalies instantly. Other conventional methods rely on oversampling to test for uniformity, which opens the door for other issues. For example, when spectra for arbitrarily selected regions of interest across an automobile are taken and chromaticity coordinates are averaged, there can be a great deal of variance between the measurements taken at each point within a given sample. Additionally, an examination of the spectra may show distinct differences between colors. While not easily seen by the naked eye, certain samples may be differentiated with typical color measurement instruments. However, subtle differences in other samples may fit within the instrument’s uncertainty specifications and might not otherwise be detected or identified with conventional filter methods.
With intelligent imaging, non-uniformities become immediately identifiable as entire areas of a sample are collected, not just spots within. Using machine learning algorithms, an automated test station can be configured to alert operators to specific issues and provide a readily identifiable flag of differences that might otherwise be missed. In addition to spatial information, hyperspectral imaging cameras can provide a more accurate and rapid assessment of automobile color metrics by identifying distinctions in objects which are invisible to the eye, color (RGB) cameras, or even imaging colorimeters.
Intelligent imaging systems can detect important differences that have a significant impact on the way the consumer interprets a car’s color. Inconsistencies can be found that are not typically visible to the naked eye or within the tight tolerances of colorimetry. The unique combination of portability with instant spectral and spatial analysis means that the same intelligent imaging instrument can be configured for a wide variety of parameters and points of interest during the inspection stage. This both optimizes accuracy and reduces the time taken to capture the image. While many manufacturers will find immediate uses for hyperspectral imaging in the production process, it can also be implemented in any part of the supply chain or within research and development applications. With advances in technology, the cost advantages of hyperspectral imaging systems also vastly improve access for its potential uses.
Looking for a reprint of this article?
From high-res PDFs to custom plaques, order your copy today!