State of the Art Part 2
What's new in the calibration field?
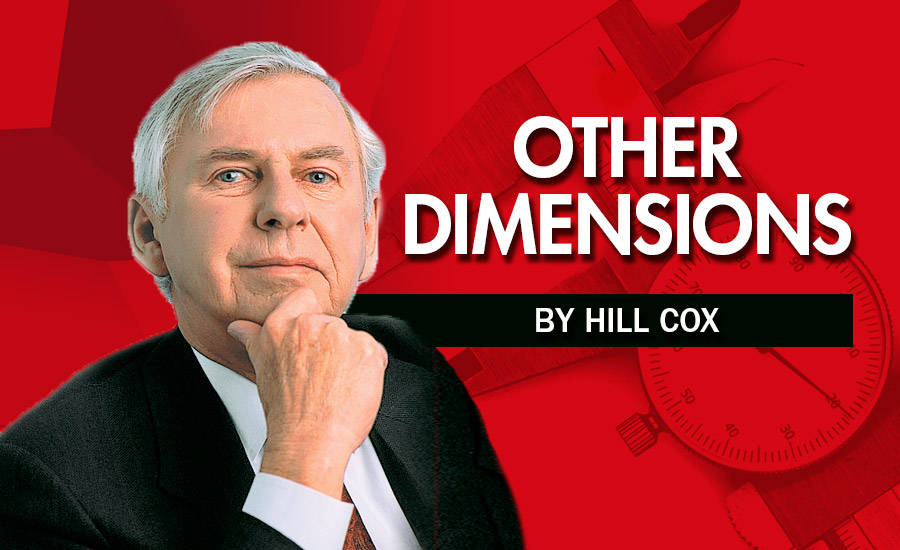
In my last column I mentioned the Market Research Study: United States Testing Laboratories done by the Consulting Group at Virginia Tech with Rachel Trebour as the project manager.
It received 529 responses from a number of fields including calibration, aerospace, energy, material testing, medical examiners—seventeen industries in all. Despite the range of laboratories covered, there were a number of common concerns across most, if not all, of them.
Calibration labs represented the largest single group—some 22.9% of respondents. I was surprised to see that 7.1% of those in the field were not accredited. I was not surprised to find that 87% were accredited to ISO 17025. Despite this wide acceptance, many labs across all sectors have the same problem: industry specific risks and requirements. These could be broken down to unique quality system requirements beyond what 17025 requires, usually in reports in the form of all types of extra information of often questionable value having to be reported. An example of this may require the lab to list the calibration dates for the equipment used, NIST traceability numbers, etc.
Another industry specific risk involves the hardware and/or methods required for certain types of products or instruments being calibrated. Typical of this would be how pitch diameter is measured and/or reported on a gage. To do the job properly, the calibration laboratory must have a copy of the relevant standard and understand the technical details. (See ASME Standard B1.25 also.)
All labs were asked to indicate areas of risk within their operations and about 31% of them indicated people problems as a key one. Employee turnover, lack of skills, low staffing levels, and human error were cited.
In the case of calibration laboratories, 46% indicated similar people concerns while 25.4% noted industry specific risks which included equipment. Part of the high staff turnover and/or low staffing levels may be caused by management trying to reduce costs by automating where possible to avoid the need for skilled staff which can result in boring jobs for remaining staff, among other problems.
This indicates that management can’t find or won’t pay for people that know what they’re doing in this field so they prefer lower cost instrument readers and look to computers to reduce or eliminate even this function. However, when the wheels come off, the instrument readers may not even recognize this and if they do, their limited knowledge makes it more difficult to get things back on track.
Laboratories across all sectors appear to be looking for magic bullets in the form of software, particularly for situations requiring acceptance and other decisions. Some existing software already has a feature which does this to a limited extent by comparing numbers. The problem with what’s out there is the numbers used for the comparison are usually taken from new specifications for items which do not necessarily apply to used items or even relate to the manufacturing tolerances the gage or instrument is required to verify. This ‘requirement’ is brought about by the owners of the items being calibrated downloading the decision making to the lab which rarely has enough data to make such a call. A lab making such decisions—by any means—runs the risk of legal problems should the decision come into question. Considering the litigious nature of business today, I consider this one of the most significant risks a calibration laboratory faces.
One way out of this problem is for laboratories to remain neutral by reporting their measurements only and leave the decision making where it belongs: with the user of the equipment. After all, the user is the only one that knows all the requirements needed for such decisions.
On the dimensional calibration side of the study there is a lot of information which I have only touched on. Lots of graphs and numbers with minimum editorial—an easy read. If you would like a copy, visit https://sites.google.com/vt.edu/cgvt-market-study/home.
This is part two of a two-part series. Read part one here.
Looking for a reprint of this article?
From high-res PDFs to custom plaques, order your copy today!