A ‘cutting’ history of accuracy
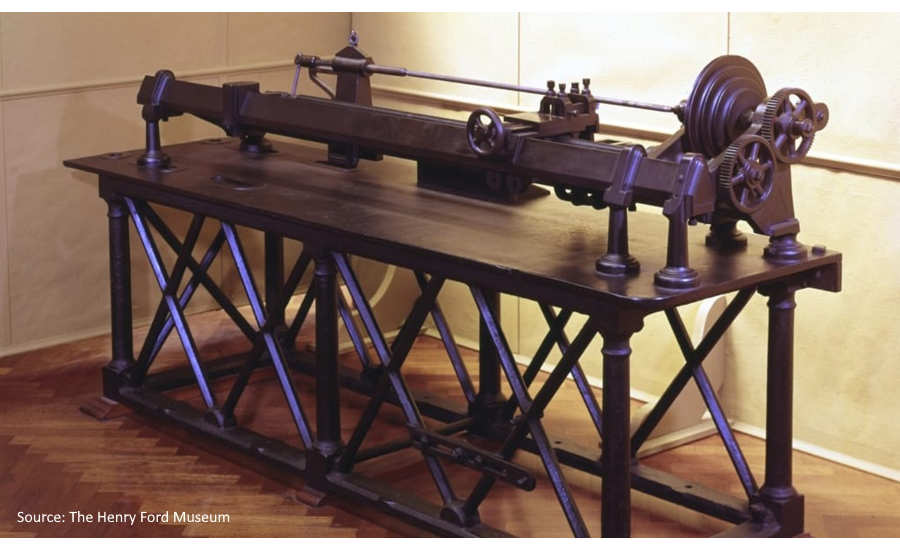
There’s a long-lived adage in woodworking and carpentry—measure twice, cut once. As civilization grew and evolved from millions of years ago when primitive cutting tools were used to hunt and gather food, a need for more accurate cutting tools grew and evolved with it.
Ever since those early days of cutting tools made of stone, the concept of cutting has remained the same—separating objects through highly directed force. Two related ideas have also remained true—the material the cutting tool is made from must be harder than the material it is cutting and stress at the contact point between the tool and the material must increase until the material breaks at that point of contact.
One of the first evolutions in cutting tools occurred in the Bronze Age when we discovered that copper could be melted and molded into stronger, finer tools. This age also brought the rise of metallurgy, leading to alloys and harder, tougher, more resistant cutting tools.
Through metallurgy, we also came to understand materials at a micro-level, like understanding the dislocation of grains in metal at an atomic level and being able to manipulate these dislocations to provide stronger cutting tools. This is probably one of the first examples of purposeful improvement of a product through a manufacturing process.
As metallurgy, and society, progressed, the world saw iron, then steel, each one-upping the other in strength, hardness, and ability to be “alloyed” with other materials. Processes for increasing the efficiency and reducing the cost of producing these alloys continued to the 1900s, somewhat culminating, if you will, with the ability to produce as much as 100 tons of steel in a single furnace.
However, in the very early 1800s, strides were being made in the accuracy of the tools we made. Ironically, ever since the early days of stone tools, tools were being used to make better tools. As we moved forward with this idea, accuracy became as important to cutting tools as the strength of the materials from which they were made (Truth No. 1). The invention of the lathe allowed for the accurate repositioning of a cutting tool during the process of mass production, which is the term that was adopted, and persists to this day, to describe the ability to produce interchangeable parts, exact replicas, if you will, with great accuracy, efficiency, and at a lower cost. By the end of that century, these more accurate “machine tools” like lathes, mills, grinders, and saws were standard in the manufacturing process.
Just a few of the more notable machine-tool inventions include:
- A machine that bored engine cylinders developed by John Wilkinson in 1775.
- A screw-cutting engine lathe designed and built by Henry Maudslay in 1797. The lathe featured a lead screw, geared to the spindle of the lathe, which advanced the tool at a constant rate of speed that ensured accurate screw threads.
- The shaper invented by James Nasmyth. It’s a machine where a workpiece could be clamped horizontally to a table and worked by a cutter using a reciprocating motion to plane, cut, or machine surfaces. Nasmyth also invented the steam hammer.
- The milling machine invented by Eli Whitney in 1818.
- And artificial abrasives developed in the late 19th century that lead to grinding machines and C.H. Norton’s demonstration of grinding an automobile crankshaft in 15 minutes—a process that previously had required five hours.
The next great impact—more like a crater—on cutting tools, as with a host of other industries, individuals, and entire societies, came from the computer. Most specifically for cutting tools, the computer numerical control, or CNC, machine. With computers at the wheel, machine tools became highly accurate and highly repeatable. More recently, cutting tools have moved past the idea of a stronger metal cutting a weaker metal to incorporate technology like laser and plasma cutters and ventured into an area of accuracy beyond that of a mere computer to include robotics, automation, artificial intelligence, and machine learning.
The proliferators of the measure-twice-cut-once rule would be proud!
Looking for a reprint of this article?
From high-res PDFs to custom plaques, order your copy today!