Four Things Your ERP System Should Do For You
ERP systems can vary widely in size, scope, features, and functionalities, depending on the needs of different manufacturers.

Images Source: Global Shop Solutions
With the manufacturing industry growing more complex every day, it’s hard to imagine operating a manufacturing enterprise without an ERP system. The software provides a critical central communication point for the business, handling all activities from quote to cash and everything in between.
Immediate benefits of using ERP include faster cycle times, better on-time delivery rates, lower labor costs, improved productivity, getting off manual spreadsheets, and more. ERP facilitates better decision making by providing accurate real-time data on every aspect of the business, and acts as an ongoing process improvement tool that empowers the organization to become leaner, more efficient and, ultimately, more profitable.
ERP systems can vary widely in size, scope, features, and functionalities, depending on the needs of different manufacturers. However, at its core every ERP system should do four things for your manufacturing business.
1. Provide A Clear View Of Your Manufacturing
In manufacturing, it’s hard to manage what you can’t see—a common problem with paper documents and spreadsheets is that they often get lost, misfiled, or are almost immediately outdated. ERP consolidates all production data into one integrated electronic system, providing complete control over how you track, measure, view, and analyze the information needed to operate a successful business.
With today’s mobile technologies, ERP can provide access to the data you need, when you need it, from any device. When employees can access real-time data anywhere at any time, information sharing becomes a process improvement tool rather than a bottleneck. Shop floor personnel can do their jobs faster and with fewer mistakes, so you can get products out the door on time while eliminating sources of internal waste.
As production processes become more visible, management can make informed decisions based on accurate data rather than intuition or guesswork. ERP tools such as customizable KPI dashboards and programs that display live data on the shop floor enable fast decision making on schedule changes, hot jobs, and other issues that demand immediate attention.
The efficiencies produced by having access to fully integrated data can be staggering. For example, it used to take Corsair Electrical Connectors, a producer of military, commercial, and aerospace aircraft connectors, 60 hours a week to create a voluminous report used to determine if the company had the materials on hand to start jobs. Now, their ERP system automatically calculates the materials on hand, determines which jobs need them, and correctly assigns them based on due dates—all within four hours.
2. Improve Your Key Metrics
Accurate job costing is one of the most critical activities in a manufacturing enterprise. Without it, quoting and estimating often miss the mark, and determining the profitability of individual jobs becomes a hit-or-miss process. At the end of the year, you can get a rough idea of whether you made money. But the data doesn’t say which products are turning a profit and which are losing money, or why.
ERP software enables manufacturers to track costs with remarkable precision, starting with clocking in and out of jobs correctly, validating the time collection, and issuing materials to the job all in real time. Shop floor personnel electronically log in and out of jobs, and the system automatically assigns the correct costs to their hours. Managers know exactly what each employee works on and how long it takes to complete a sequence. The system automatically assigns any time not logged into a job to indirect.
Precise job costing also makes estimating and quoting more accurate. Suppose you estimated $500 to produce a part, but it actually cost $750. Did raw materials cost more than expected? Did quality issues require rework? Was overtime needed to complete the job? All this information is instantly available in the ERP system for analysis. Furthermore, reviewing historical data for the part can indicate whether the discrepancy was a one-time anomaly or an ongoing trend that needs attention. When you collect labor, issue materials and track costs with precision, you can estimate and quote with confidence.
Accurate job costing also has a beneficial impact on scheduling. When you know with certainty how many labor hours it takes to complete a job and how much capacity exists at each workcenter, you can schedule with greater precision. This, in turn, enables the setting of realistic due dates for on-time delivery every time.
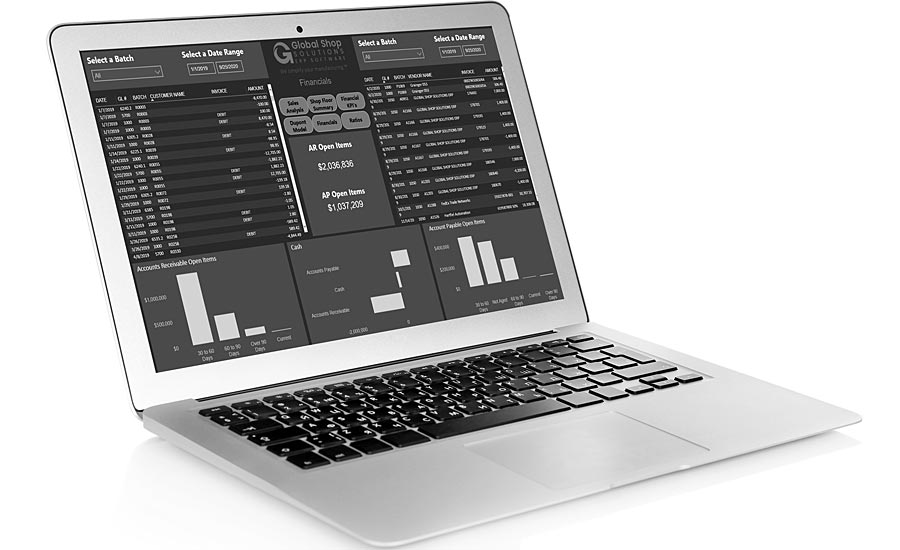
3. Generate Better Outcomes
ERP software can have different impacts depending on what the business is trying to accomplish. In general, manufacturing companies can expect the following outcomes:
- Move parts through the shop faster.
- Schedule and deliver on time.
- Get your quality right.
- Know your costs.
- Grow sales.
- Maintain accurate inventory.
- Control labor costs.
- Improve efficiency by getting rid of manual spreadsheets.
- Integrate your technology and machines.
- Serve your customers faster and better.
ERP also helps improve the company’s competitive position. Suppose you typically ship jobs in two weeks and a customer asks for a one-week turnaround. Most manufacturers would accept the job hoping they can meet the delivery date. This decision often results in working overtime, higher costs for expedited materials, late delivery, and losing money on the job.
ERP lets you know with certainty whether you can meet the deadline without disrupting other jobs in the process. It identifies all the steps you have to complete in order to ship in one week, shows your available labor and resource capacity, and determines whether you have the materials on hand for the job. This changes your thinking from a delivery date mindset to an operations completion approach so you can make the right decision about whether to accept the job.
ERP also allows you to provide faster, more responsive customer service. When customers call in about the status of a job, the typical response sounds like, “Let me check on that and get back to you.” With ERP, sales reps can instantly see the current status of the job and give customers an immediate answer. They can also check available capacity and materials on hand before agreeing to a requested due date. In today’s world, quick responses and fast turnaround times produce happy customers. ERP makes both a way of life.
4. Become Your Most Valuable Asset
When used properly, ERP becomes the engine driving everything in your business. From quoting jobs and taking orders to shipping on time and receiving payment, ERP provides a solid foundation for building the infrastructure and shop floor processes that make manufacturing faster, easier and more profitable. ERP often changes how manufacturers think about their businesses, and opens the door to imagining what could be rather than getting stuck in what is now.
By providing accurate data in every area of the business, ERP also creates a culture of accountability. Machinists know when they’re performing well and when they’re not. Managers have the data to reward those who exceed expectations and hold coaching conversations with those who fall short. ERP also provides opportunities for employees to develop new skills and capabilities that boost their careers by adding more value to the business.
As manufacturing becomes more competitive around the globe, opportunities abound for U.S. manufacturers to bring work back from overseas. Without ERP to provide a detailed history of the products under consideration, such a move might be too risky. ERP provides the data needed to determine which opportunities you can take advantage of and which do not align with your current cost structure or strategic objectives.
Build For Today And Tomorrow With ERP
Continuing advances in production tools and technologies, combined with the rapidly growing Internet of Things (IoT), will cause the future of manufacturing to look very different than it does today. ERP helps you plan and prepare for the “new now” by providing detailed historical and current data to help analyze where your customers are heading, where your business needs to go to meet them, and what you will need to do to get there.
Increasingly, today’s ERP developers are creating interfaces that enable ERP to communicate with third-party IoT devices to expand the capabilities of the software. For example, nesting software interfaces can integrate the shop floor cutting process by allowing your ERP system and nesting software to share data with each other.
The ERP system sends work orders, workcenter details, inventory data and other information to the nesting software, which uses the data to optimize material usage and cut patterns for individual sheets of material. The nesting software then sends cutlist details, material drops, scrap, and estimates for routing and work orders back to your ERP system. The entire process only takes a few minutes.
As artificial intelligence and virtual reality technologies continue to make inroads into the manufacturing landscape, ERP software will play a critical role in integrating these game-changing technologies with the way you do business. If ERP doesn’t fit the role of your company’s most valuable asset—for today and tomorrow—you either have the wrong system or you’re not using it correctly.
Looking for a reprint of this article?
From high-res PDFs to custom plaques, order your copy today!