Other Dimensions | Hill Cox
Thread Ring Gage Calibration
The basic advantage of the solid thread ring is that it does not have a size adjustment that can be changed.
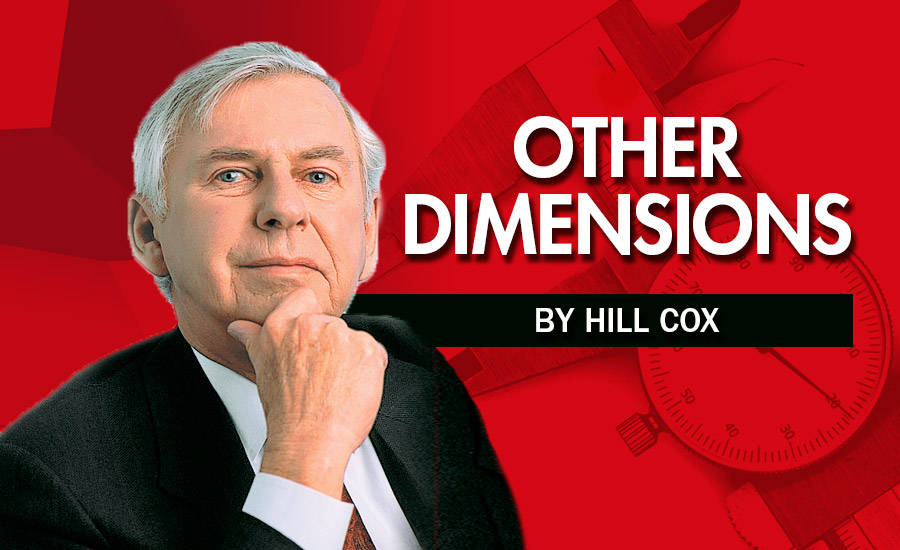
In my last column I listed some basic equipment requirements for the calibration of thread plug gages so I thought it would be helpful to give mating gages the same treatment.
Thread ring gages sold in North America are the adjustable type as standard compared with the rest of the world where they are solid or non-adjustable. Endless arguments over which is the better type to use for the typical threaded product will always be with us so I won’t go into great detail on that subject. However, the basic advantage of the solid thread ring is that it does not have a size adjustment that can be changed.
The Hardware
The ASME standards for adjustable thread ring gages require the use of setting plug gages specifically made to the standards for calibration purposes. There is no instrument on the market at this time that will produce measurements of pitch diameter, for example, that will duplicate the size indicated by the use of setting plugs. Yes, there are a number of devices their makers claim can measure pitch diameter but the use of such equipment will always produce pitch diameter readings that are larger than indicated by the correct setting plug gage. This is due to the fact that such devices are measuring the thread at two points of contact while the setting plug – in a perfect world – is contacting the full form of the ring. This means that variations in thread form, roundness, linear pitch, etc., will affect the functional size of the ring while remaining undetected by direct measurement.
When you have rings below approximately .500” or 12mm, you are below the capacity of most, if not all, direct measuring devices so setting plugs are your only option. Irrespective of what size ring you are trying to verify, you need a setting plug that is made to the specific size and class of fit as the ring.
The Masters
As noted above, the setting plug gages are the masters involved in this calibration work. While small, they have a tolerance for pitch diameter size, which creates great discussions regularly. For example, if you have two settings plugs, one at the lower limit of size, the other at the upper limit of size you could set the ring on one and the other would not enter the ring or would do so with too much play in the fit. This is all due to the gage maker’s tolerance on the plugs.
The problem crops up a lot with rings set by their maker to their setting plug which is unlikely to be the same as that used by your calibration source.
The Environment
Assuming the rings and setting plugs are made of steel, the environment won’t pose too many problems provided both items are at the same temperature. Finally—some good news in all of this. Unfortunately, there is something else you have to consider: disputes over settings.
Settling Disputes
The easy way to settle most disputes is to have the rings in question set on the same master by the same technician. If you have two different calibration facilities setting the rings on different setting plugs, there will be disputes caused by differences in ‘feel’ between the technicians doing the work and minor size differences between the plugs.
If things get hot enough, the labs might pull out their accreditation to show how good they are and there may be a significant difference between them. So, now what? Who do you believe? Even though they may be accredited, I would suggest you don’t have much faith in either of them or the uncertainty values shown on their scopes as the numbers are simply guesses rarely supported by an uncertainty budget worthy of the name. For example, linear pitch is a critical element of a thread but there are very few labs that have the right hardware to measure it to a level of precision required for a setting plug.
If you’ve learned anything from this rant, I hope it will show you why you should always buy a proper setting plug with any special thread rings you need to avoid these problems. And while the rings may wear out in time, setting plugs will last much longer
Looking for a reprint of this article?
From high-res PDFs to custom plaques, order your copy today!