Other Dimensions | Hill Cox
Plain Plug Gage Calibration
Nothing could be simpler than calibrating the lowly plain plug gage - at least at first glance
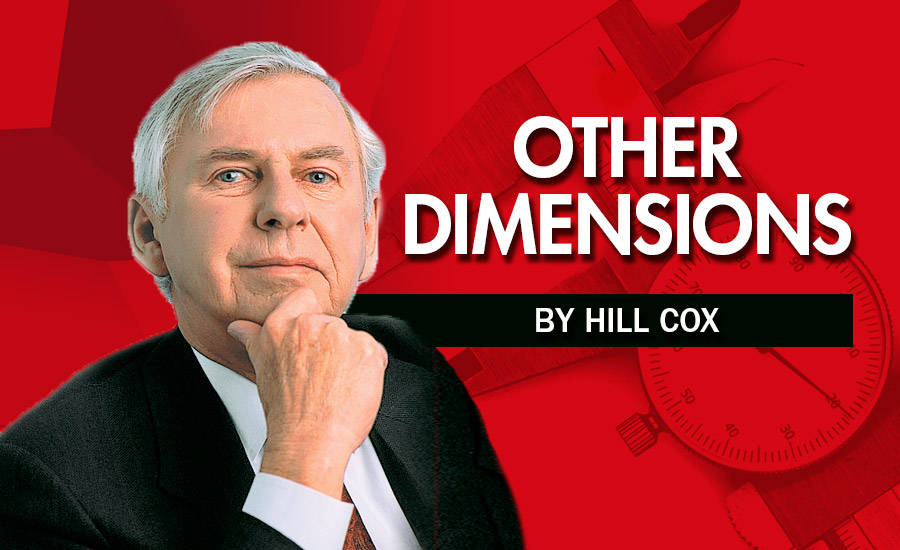
Following the path of a cheap and cheerful ‘how to do it’ format of the last two columns, I continue with something easy – or is it?
Nothing could be simpler than calibrating the lowly plain plug gage – at least at first glance. You only have one thing to deal with, an outside diameter that is easy to get at with a variety of measuring instruments. However, before you grab your trusty digital micrometer to do the job, there are a few things to consider.
The Hardware
The variety of instruments available for the task may have the desired resolution due to the wonders of electronics, but not all of them operate at a level of precision to make that resolution worth having. This is due to the makers of them realizing that for a few dollars more, they can improve the resolution and charge a lot more for the instrument because - even today – too many people equate resolution with precision.
So, when it comes to resolution, what do you need? It depends on the tolerance of the gage. For example, if the tolerance is .0001” or .0025mm, you require a device with .00001”/.00025 or better. You could get away with a little coarser resolution but your uncertainty for the calibration will increase so you might not be any further ahead trying to skate around what you should have.
The most popular and, in many cases, the most precise method of taking these measurements is achieved using comparative techniques. This involves a high magnification comparator setup comprising a sturdy comparator stand on which is mounted some form of LVDT probe connected to a display that compares the size of the gage being calibrated to a build-up of gage blocks to provide a 1:1 comparison. The usual comparator stands designed for use with dial or digital indicators are rarely solid enough which can cause the digits on the most precise display to dance around and drive you nuts. Maybe I should have written a ‘chunky’ comparator stand is what you need. In simpler terms, if the device you intend using for such calibration can be held in one hand, it won’t be solid enough.
An alternative piece of hardware is a universal length measuring machine (ULM). These devices come with varying levels of precision and have the advantage that, once set on a single master, they can be used to measure a range of sizes. It’s still a comparative process but the design of this type of device is such that manual manipulation of the gage is avoided including the search for the actual diameter or high point on the gage. However, like other comparative devices, at some point during the process a master or masters are required.
The Masters
Gage block build-ups for use as masters are required for one-to-one comparative measurements while single gage blocks covering a range are all that a ULM system needs. Since build-ups of blocks may typically include up to four blocks per built-up size master, their flatness and parallelism and wringing characteristics reduce the precision of the size while the ULM single block method does not have this problem to any significant degree.
The highest level of precision will require that the blocks used in build-ups have their setting size adjusted to account for the variation of each block in the stack. Some companies may use blocks to one of the higher levels of precision and ignore this which is possible, but is not as exacting as adjusting the setting size based on individual block calibrated values. If you have the appropriate capability, which means a long range, high precision gage block comparator, calibrating the built-up stack of gage blocks eliminates this problem
As you’ve already guessed, the uncertainty in the calibration of gage blocks used must be as low as you can get without breaking the bank for their calibration.
Some Other Stuff
The environment in which this type of calibration is done must be controlled or the fanciest masters and measuring hardware will be of little benefit. The impact of this increases in proportion to the level of precision you need to obtain. If your masters are ceramic and the gages to be calibrated are steel, you have a difference in thermal expansion between these materials that has to be considered.
There are other factors to be considered but I think I’ve given you enough to think about for now.
Looking for a reprint of this article?
From high-res PDFs to custom plaques, order your copy today!