Other Dimensions | Hill Cox
Plain Ring Gage Calibration
Short Range Comparison Techniques are the Most Popular for Calibrating Plain Rings.
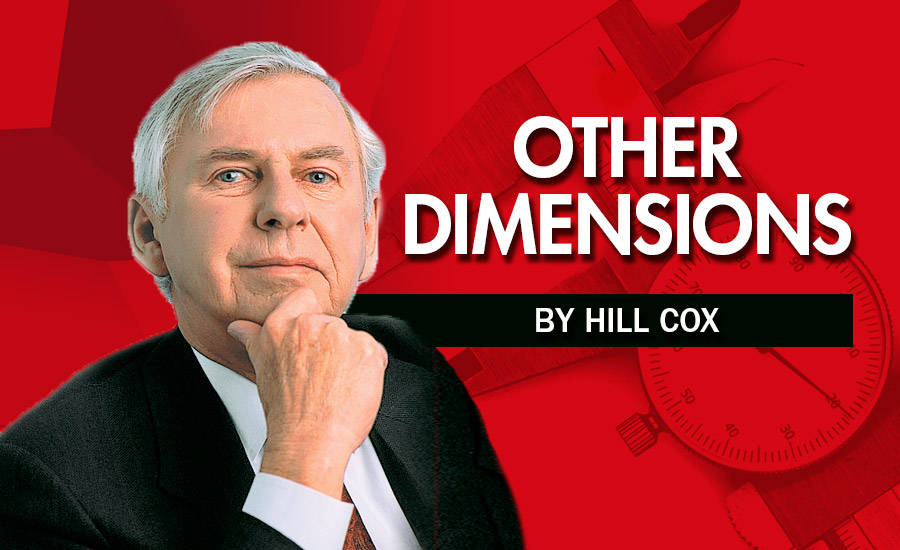
This column is the fourth in a series of overviews on gage calibration to give you some idea of what is involved at this level of measurement. A book could probably be written on each subject and not do the job very well so I will continue keeping it simple to avoid completely ruining your day.
Like their plain plug gage counterparts, plain rings appear to be a relatively simple matter when it comes to calibrating them since there is only one feature to be measured. But, there’s always a ‘but’, the process is not as simple as you might expect.
The Hardware
With ring gages requiring an internal measurement, once you get below .5” or 12mm in diameter, the number of devices you can use to do so is reduced due to physical size of the measuring contacts and the arms they are mounted. Your ‘millionths’ reading digital inside micrometer will not be of any help in the process if the tolerance on the ring is closer than say, .001” or .02mm and most coordinate measuring machines (CMMs) won’t be any better.
Short range comparison techniques are the most popular for calibrating plain rings. They use internal comparators specially designed for the work with the measurements being taken using an LVDT and analog or digital display. These comparators have mechanisms that enable the contacts to find the high point of the bore through centering and tilting it since there is no guarantee that the gage face that rests on the worktable is square to the bore, which could cause co-sine errors. Without this capability manual manipulation is required which is cumbersome, provides erratic readings and has poor repeatability. Like all such devices, this type of comparator requires setting with a nominal size master for each size to be measured due to the short measuring range.
Universal length measuring machines designed for this type of work incorporate controls to manipulate the ring and due to their greater measuring range, only require one or two masters to cover a range of sizes. These features make the ULM faster to use, and in most cases, a more precise device for such measurements.
The Masters
Where one-to-one masters are required, a stack of gage blocks for each size is commonly used but there are concerns with this process that have to be accounted for. First, there is the known error of the build-up of the blocks taken from their calibration report. On its own, the stack is of no value as it is an external value rather than an internal one required to set the instrument. This is created by wringing parallel bars or blocks to the ends of the stack such that they overhang the ends providing an accurate gap for setting purposes. Parallelism of the gap that has been created must be to a high order of precision to be of any value.
A major problem in using gage blocks for this purpose is that the build-up or stack of them creates flat, more or less parallel surfaces while the object being measuring has a round surface so if the spherical contacts have flats on them, the effect of that deviation will be incorporated in the setting of the instrument.
A ULM only needs one or two masters to cover a range of sizes but will suffer from the same problem noted in the previous paragraph with flats on spherical contacts. An effective way to avoid or significantly reduce this problem is to set the ULM with master rings calibrated by NIST or your equivalent national institute of metrology.
Save yourself from grief by ensuring the masters are made from steel so you don’t have to make allowances for different coefficients of expansion.
Some Other Stuff To Consider
Like all high-end gage calibration, the best of equipment is rendered useless if the environment in which it is used is not suitable. ‘Suitable’ in dimensional work means it has to be controlled to 68⁰ or 20⁰C within close limits. Some latitude can be allowed if the measuring device and masters are all steel and have been in the lab long enough to reach the same temperature, one that doesn’t change much over the short term, and the gage is not manually handled very much or at all. Confirm this with an electronic contact type thermometer prior to taking the measurement.
Hill Cox is president of Frank Cox Metrology Ltd. (Brampton, Ontario, Canada).
Looking for a reprint of this article?
From high-res PDFs to custom plaques, order your copy today!