Software & Analysis
Make A Quality Part On Time Every Time With ERP Software
With modern ERP software, scrapping non-conforming parts can and should happen in real time.

All Images Source: Global Shop Solutions
When American manufacturers began taking quality seriously in the 1990s, they focused on physical quality to do a better job of meeting customer tolerance requirements. At first, many manufacturers viewed total quality management as a fad. However, those who forged ahead realized they could gain a competitive advantage by consistently delivering high-tolerance parts with a minimum of returned rejects. As other manufacturers began to catch on, quality parts became a must-have to get on a customer’s vendor list.
Since then, the definition of quality has changed dramatically, and so have customer expectations for what it entails. The next phase in total quality development consisted of manufacturing parts to precise tolerance at a lower cost. This was addressed in several ways, including outsourcing production to countries with lower labor costs and embracing increasingly sophisticated technology to provide quality products for less.
As product quality continued to improve and the price of finished parts became more competitive, customers again recalibrated their quality expectations. Now the expectation for superior quality consists of delivering high-tolerance, low-cost parts on time every time. If you can’t deliver on all three, you don’t make the cut.
The quality software in most ERP systems tracks manufactured and purchased parts by scrap trends, cost, department, employee, workcenter, and other criteria. But there’s more to delivering parts on time than knowing how many you scrap and how much it costs. Having an ERP system that integrates various software modules with the quality module is essential for understanding, measuring and managing all the processes that contribute to superior quality and on-time delivery. For example:
1. Vendor Performance
Most ERP quality modules track vendor performance in terms of tolerance accuracy, number of rejects, cost, and on-time delivery rates. Some provide additional features that simplify the overall vendor management process, such as a vendor approval process that ensures vendors meet your criteria in all areas. It lets you set up a vendor approval workflow that includes all necessary signoffs and has a field that only allows purchases from approved vendors.
Other features that simplify vendor performance management include returned material authorization (RMA) forms that help speed up the return process; tailored reports and dashboards that make vendor analysis faster and more efficient by displaying only the data you want to see on the screen; and customizable data fields that can be set up for side-by-side comparisons of supplier performance.
Your customers hold you accountable for delivering quality parts on time. ERP software helps you do the same with your vendors.
2. Routing Software
ERP routing enhances quality by enabling first-piece inspection data to be included throughout all router documentation. A first article inspection involves testing one or more parts from the first production run to verify a precision match with customer specifications. Having this data in the router at every step of the production process helps ensure every piece in every lot meets the customer’s quality standards.
The routing software helps with on-time delivery by optimizing production sequencing so you can manufacture a high-quality part at the lowest cost in the least amount of time. It provides accurate, detailed work instructions for every step of the production process, making it easier to meet scheduled due dates.
3. ECN Authentication
Using handwritten notes or word of mouth to manage engineering change notices (ECN) opens the door to miscommunication and production mistakes. ERP electronically tracks all ECNs in the quality module so you can efficiently manage both immediate and future changes. The module produces documented revision levels for customers and communicates the revision change in a timely manner. It also creates an authorization list by providing the internal process change steps, thereby ensuring that every step is documented and authorized before moving to the next one.
ERP software also provides multi-factor control over the approval process by requiring engineer and/or quality manager signoff before the designated corrective action can proceed. Efficiency is added through functionalities in the system, such as copying the bill and router from the defective part to new bills and routers.
The quality module safeguards against future problems with the part by allowing you to set up the ECN record to allow or disallow use of the part numbers until final sign-off. This helps prevent certain issues, such as entering an inactive revision level on an order or sending inactive parts and work orders to have labor applied. If a revised part will continue to be sold, purchased or manufactured, the system activates the number. Old revisions that will no longer be sold, purchased or manufactured remain inactive.
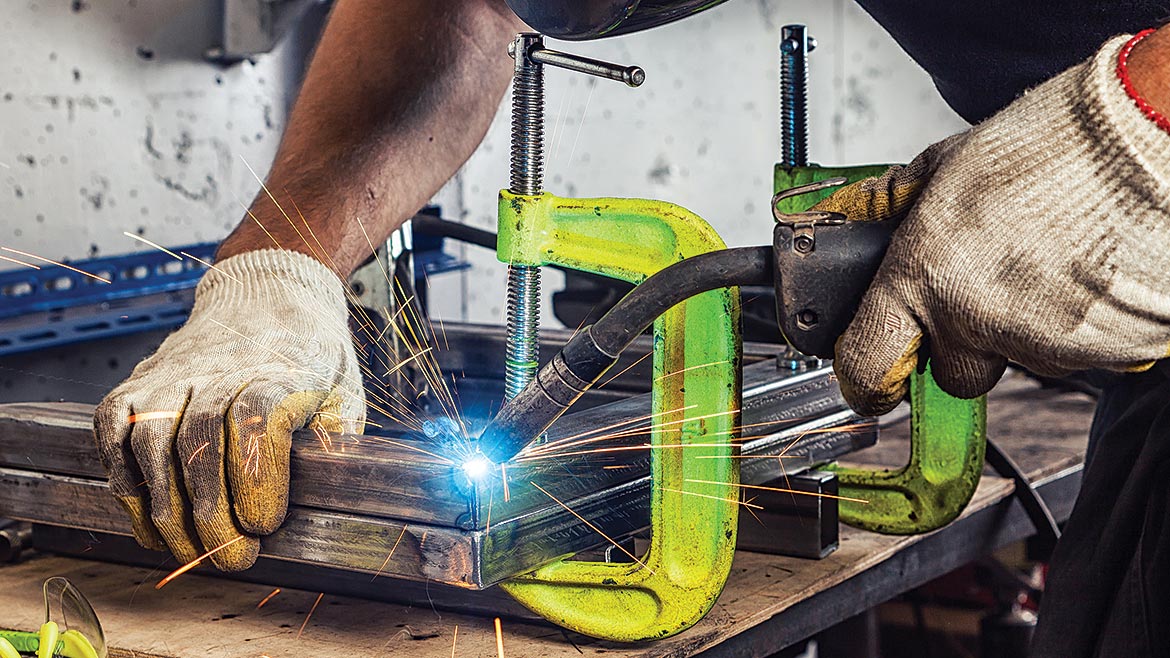
4. Real-Time Quality Control
For years, managing quality was mostly a historic process. Defective parts usually didn’t get identified until after the job was complete, resulting in more rework and higher cost. With modern ERP software, scrapping non-conforming parts can and should happen in real time.
This process starts with machinists entering non-conforming data as soon as they finish a job sequence. Placing ERP software stations at each workcenter makes this step quick and easy. The data entry screen can be set up to alert quality control supervisors by automatically sending texts or emails through the ERP messaging system. This enables quality control decision makers to analyze and respond to the problem as soon as the non-conforming parts are entered into the system. When a machinist scraps a part, the ERP system automatically sends the data to the quality module, which assigns a dollar value to the part.
Armed with this data, managers can make informed decisions about whether to scrap or rework the defective parts. The data also provides information for a cause and corrective actions report, which is then attached to the work order to prevent further mistakes from recurring.
5. Error-Free Quality Management
ERP software should track everything related to quality – from the time a job begins to the reconciliation of the financials. This requires the system to automatically send data from planning and scheduling, shop management, document control, company messaging, dashboard software, and other areas of the system directly to the quality module. Otherwise, it can’t digitally receive the data it needs to manage the quality process.
With fully integrated ERP software, the entire system works together to make quality a precise, error-free process. Routers electronically deliver accurate details and work orders to the shop floor. Engineers and machinists always work off the correct document revision. The system traces every part with 100% accuracy as they move through the shop floor.
ERP lets you identify bad parts as they’re made, accurately log all purchasing, inventory and manufacturing rejects, and view all rework, rejects and scraps from one dashboard. It tracks your entire quality history in one central location and easily produces quality documentation for ISO and other compliance auditors. Most important, it provides the true cost of quality by part, job and overall.
If you’re losing customers due to quality issues or the same quality problems keep recurring, ask yourself five questions to determine if your ERP system is up to the task:
- Does your quality software enable you to identify and correct defective parts before you ship them?
- When parts are out of tolerance, does your quality module prevent the job from continuing until the problem gets corrected?
- Can you identify your cost of quality down to the part level?
- Does your scrap rate equal or surpass the industry standard?
- When you identify a quality problem with work in progress, does your system calculate whether it would be more cost-effective to correct the defective parts or scrap them and start over?
Managing quality is one of the most complex tasks for a manufacturing enterprise, but ERP quality modules have come a long way in the last decade. From immediate entry of scrap into the system to the ability to analyze the data in real time and take quick corrective action, delivering quality parts on time every time has become an achievable goal for all manufacturers.
Looking for a reprint of this article?
From high-res PDFs to custom plaques, order your copy today!