ASNT Column | Muriel Magloire
Enhancing Safety Through Nondestructive Testing (NDT): Preventing Catastrophes and Ensuring Integrity
NDT plays a major role in preventing disasters and upholding safety standards.
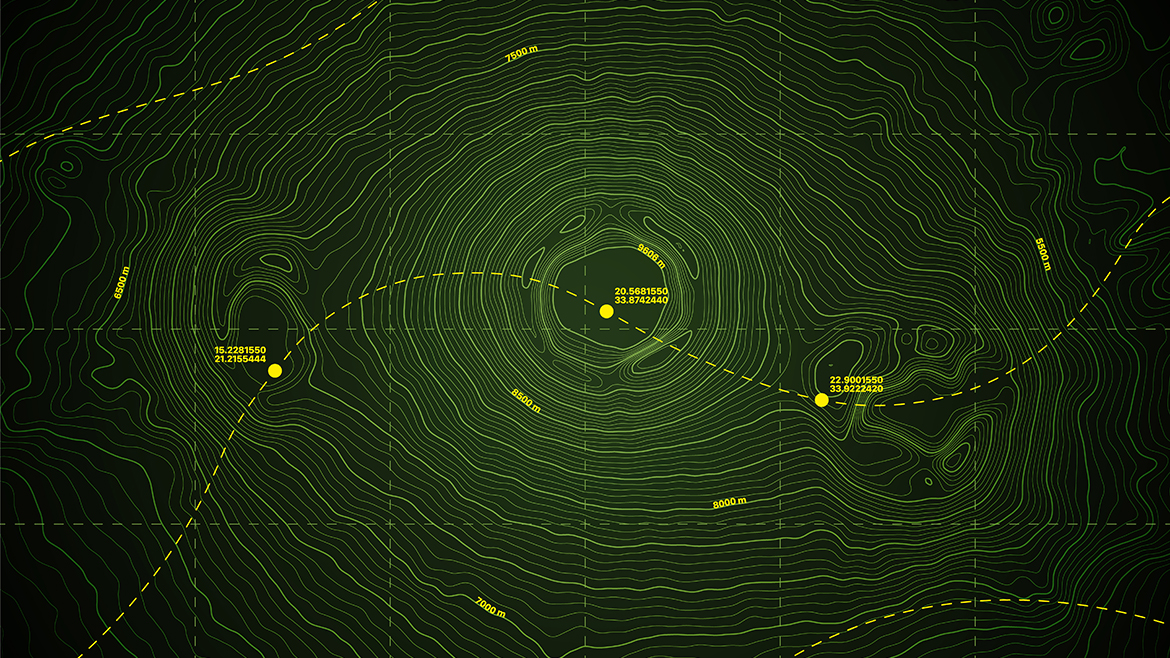
Gettyimages /yamonstro / iStock / Getty Images Plus
Human error is inevitable. No matter the research, the preparedness, or the technology available, mistakes happen. In mitigating the consequences of human error, particularly in disaster prevention and recovery, nondestructive testing (NDT) plays a significant role.
The NDT inspector’s primary responsibility lies in meticulous testing to ensure the readiness of materials and components for their intended use. NDT personnel provide ongoing support from the manufacturing phase, through daily use during maintenance periods, and usually until retirement of materials. These professionals play a key role in preventing severe damage to components in use, where they are susceptible to anything from normal wear and tear to catastrophic damage by finding indications and discontinuities that can significantly worsen over time or suddenly in the event of a disaster. Neglecting these defects can result in financial or time-related losses and, in the worst cases, the loss of lives.
One notable incident occurred in October 2022, when the USS Connecticut hit an undersea mountain off the coast of China. The nuclear-powered submarine sustained significant damage and 11 crew members suffered injuries. A subsequent investigation by the Navy concluded the crash was preventable. This incident and the process that followed in its wake, serve as an example of the weighty importance of NDT in assessing the magnitude of the damage, to assist the engineering team with creating a pathway to repair. It underscores the necessity of NDT inspections in the aftermath of inevitable human error to ensure future safety.
NDT
Related Articles
The USS Connecticut was taken to Puget Sound Naval Shipyard for repair. Our team of NDT inspectors, engineers, welders, machinists, and a host of other professionals all work side-by-side daily to complete this huge undertaking. The mission is to return the vessel to the U.S. Fleet in pristine condition without a trace of the damage sustained in the accident.
NDT inspectors are utilized across various sectors in our society. It is common practice for our inspections to take place before any machine or welding expert begins repairs or new construction. In the case of the USS Connecticut, our team collaborated with engineers to assess and document the damage in the immediate aftermath of the accident. This phase required careful and scrupulous attention to detail, as each step was used to build the foundation for the submarine’s restoration. A high level of precision is essential when dealing with an extremely complex vessel that suffered considerable damage.
For this reason, the field of NDT operates under structured processes that – when followed closely – guides professionals to the best outcomes. These standards and procedures are designed to ensure that NDT assessments yield the most accurate and reliable results possible.
In many cases, visual testing (VT) is the first step of the inspection process. In the context of a situation like this, VT entails a comprehensive examination of a vessel from every angle and each layer, and may start from the outside and continuing to the most inward layers or vice versa. VT focuses on identifying and addressing surface-level issues, which may include things like visible cracks and porosity.
Through assessment and repair preparation, engineers may determine that additional inspection methods are required and might include ultrasonic testing (UT), magnetic particle testing (MT), and liquid penetrant testing (PT).
UT inspection can be used to measure the remaining thickness of submarine pipes or examine the internal structure of submarine walls for possible discontinuities like cracks or voids. This method, like radiographic testing (RT), provides more of a volumetric inspection than MT and PT, but is safer because it uses sound waves instead of radiation waves.
Meanwhile, MT provides an excellent way to uncover surface-breaking discontinuities or those that sit just beneath the surface by using magnetic fields on ferromagnetic materials. This method is especially useful when inspecting the hull of a submarine vessel if it is magnetic.
When you have components that are not magnetic, PT may be the way to go. Through PT inspections, we can test the entire external surface of an object, some times in one operation depending on size, even if it has a complex shape like many parts of the USS Connecticut. With this method, we can detect and magnify very small discontinuities to help provide information on location and approximate depth with a fairly simple evaluation and interpretation process. Unlike MT inspection, PT can only detect discontinuities that break the surface of the part.
A thorough quality check is always the last step, ensuring that any errors present are discovered and corrected.
The standards and codes of NDT inspections are set by the American Petroleum Institute (API), the American Society for Mechanical Engineers (ASME) and the American Society for Testing and Materials (ASTM). The American Society for Nondestructive Testing (ASNT) then advances scientific, engineering, and technical knowledge in the field of NDT to create a safer world.
While demonstrating the salient role that NDT plays in high-profile situations, this case also demonstrates the broader relevance of NDT in ensuring the safety and integrity of materials and equipment. NDT plays a major role in preventing disasters and upholding safety standards.
In a world where human error is inevitable, NDT is a pivotal counteractive measure. Though we cannot prevent all accidents from happening, we can minimize the fallout by ensuring that materials are safe before use, during use, and after disaster strikes. By following NDT procedures with full integrity, we play a significant role in ensuring safety and quality across the board.
Looking for a reprint of this article?
From high-res PDFs to custom plaques, order your copy today!