Meet the 2024 Quality Rookie of the Year: Justin Wise
April 10, 2024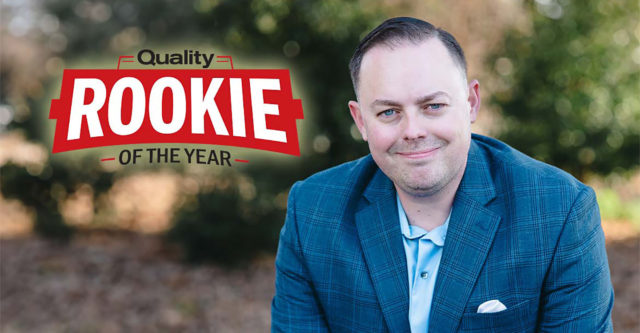
Meet the 2024 Quality Rookie of the Year: Justin Wise
April 10, 2024Photos provided by Justin Wise

ARTICLE INDEX
RELATED
It’s not every day you meet someone who has been deployed seven times who also speaks Navajo and Cahuilla. Justin Wise has had a long and varied career. When we spoke he was off to Hawaii the next day for a flight with the California Air National Guard.
He has two bachelor’s degrees and is finishing up a master’s degree in quality this year at California State University at Dominguez Hills. His applications for a Ph.D. program are pending. After several years at the Defense Contract Management Agency (DCMA), he just started a new job in February working as an inspector general with the Navy.
Quality has been a constant through it all. As an Air Force mechanic, he’s experienced the pain firsthand of a part that fails immediately after installation. Getting bad parts was the worst feeling. “It’s agonizing,” he says. “Once I got to DCMA, I wanted to make things better so my brothers and sisters get those parts and don’t have those issues.”
And when he was the one in the field, he didn’t forget about those back in the office.
“When he was deployed, he was still answering questions about his Monday through Friday job,” said former colleague Michael Vittorio. “People always depend on him, they know he’ll always deliver. Every time I talk to him, there’s something going on. He still hasn’t let up.”
He was named the 2021 Quality Representative of the Year award for the entire DCMA, a career highlight in addition to his military career.
Quality agrees with DCMA—Justin Wise is a person worth honoring—and he is our 2024 Rookie of the Year.
Starting Out
From being on a small Forward Operating Base in Afghanistan to flying to Hawaii for a few days for aircraft maintenance, his career has lead him all over. He started his career in the Air Force as active duty, then went to the reserves, then California Air National Guard.
Looking for a reprint of this article?
From high-res PDFs to custom plaques, order your copy today!
He likes to volunteer while he is deployed. The deployments have lasted anywhere from nine months to 90 days. During his deployment to Djibouti, a small country located in the Horn of Africa, he ordered soccer balls to be sent to his site so local kids could play. Volunteering makes it time well spent, he says.


And it’s not just working on the project at hand. Ever answer emails while deployed in a combat zone? For Wise, this is just standard operating procedure.
This year he’ll have 19 years with the military. Though 20 years is a good time to retire, he plans on continuing and seeing how far he can go.
“It’s been a great ride,” Wise says. “Who knew 20 years would pass so quickly?”

The Importance of Mentors

Mentors have helped him along his career, showing how things work and smoothed the way. He urges others to help newcomers to the industry and for newcomers to seek out mentors. You can’t go it alone, though he did try to early in his career.
He’s been active duty Air Force, reserves, and now Air National Guard. This latest position has kept him very busy. Missions could include strategic airlift, training, or modular airborne firefighting, for example, or anything needed by the government.
His military career has been woven through his quality career. Both sides involve quality. As an aircraft mechanic, he knows the importance of quality, and how important the right processes are for success.
During an early manufacturing job, he kept ending up in quality because his position would have been filled by the time he got back from a deployment.
He enjoyed the role of quality, and knowing how everything works. With his experience in the California Air National Guard and the aerospace industry, he had a broad range of knowledge to apply to quality.
Mentoring others was the next logical step.

The 2024 Quality Rookie of the Year Shares His Story
Justin Wise has had a long and varied career, including seven military deployments. He has two bachelor’s degrees and is finishing up a master’s degree in quality this year at California State University at Dominguez Hills. Quality has been a constant through it all. Here he offers his perspective on quality as well as how to say hello in Cahuilla.
Listen to more Quality podcasts.
Michael Vittorio, a quality assurance specialist at DCMA, met Wise about eight years ago through the military. Within a few years, both had gone into quality.
“It’s a natural transition to go to quality from our role,” Vittorio says. In their work at DCMA, they ensured that aircraft parts weren’t defective.
“As an aircraft mechanic goes, he’s very detail oriented. He loves getting into the books, loves learning the whys and the hows of how a process flows,” Vittorio says. “He’s very willing to support others. One example on the military side of things, we had a huge influx of newer people come in, with no experience on maintenance. He sat down and developed, on his own, a training plan to help them.”
“That’s probably his biggest attribute, his willingness to support others and be there as a mentor,” Vittorio said. “People look to him, if they have a question or a concern, people go to him, he’s a good person to talk to, he’s there to listen with an open mind and open heart.”
“His leadership, his ability to listen, his ability to help. Those are the main things that stand out for Justin. His knowledge, he’s always diving into books, always diving into manuals to learn how something works. He gets an assignment or a task, he wants to learn everything there is to learn about it. I think that speaks volumes. He’s a good person to work with and a good person to be around.”
QUALITY CONCEPTS AT WORK
“Justin has adeptly utilized quality concepts and techniques to solve problems and capitalize on opportunities within our organization. One notable example is his implementation of a root cause analysis process to address recurring quality issues in the contractor we oversee's manufacturing line. By systematically identifying underlying causes of defects and implementing corrective actions, Justin successfully reduced defect rates by 30% within a three-month period. Additionally, Justin implemented statistical process control (SPC) techniques to monitor key process parameters and identify potential deviations before they escalate into quality issues. This proactive approach not only prevented defects but also optimized production processes, resulting in a 20% increase in production yield. Furthermore, Justin utilized Six Sigma methodologies to streamline our inventory management processes, reducing lead times by 15% and improving overall efficiency.” — From William Schuh’s nomination
Early Days
He recalled his mother saying he wanted to be a doctor when he was little, though he doesn’t remember this. He was interested in the police and even took a sheriff’s exam, but realized he didn’t like the idea of being on call 24/7 along with overtime and prisons. Later he was interested in art and thought he would become a graphic designer. Though his career didn’t go that route, he doesn’t regret his degrees and would love to get more.
He watched 9/11 in his high school classroom and wanted to join the military after high school. His mother convinced him to try some college first. Today he has two bachelor’s degrees: one in art history with a minor in anthropology and another in history with a minor in native studies. He’s finishing up a master’s in quality and also interested in pursuing a doctorate as well. Though his career doesn’t depend on these advanced degrees, he enjoys learning and says when you stop learning you stop growing.

Unique Skills
Geza Koszty, a colleague at DCMA with 45 years in the industry, says it was good to have people like Wise around. “It helps us to have new people come in and kind of rattle our cages,” Koszty says. “He was very good at inspecting the airplane on the mechanical side, he knew his job very well. It helped the company a lot.”
Michael Adams was Wise’s immediate past supervisor at DCMA, and says he was a strong member of the team. “He was always one of the bigger go-getters.” Adams said he handled things well. Once there was a rash of issues with a contractor’s documentation. “Instead of applying a Big Brother hand,” he set up biweekly meetings, a Six Sigma project, and approached it the way you might in industry. He asked “How do we fix this?” instead of blaming the company or telling them what to do. This approach reduced documentation issues with the contactor, allowing them to fix themselves, Adams said. Wise set up the project to work with them instead of against them.
When looking for someone to take on a new project, Wise was always ready. Adams said he was one of the first people to take on a new task. He was “very excited about the mission, being engaged, wanted to do the best always.” If there was feedback, “he was always willing to hear it. ‘Okay, that’s something I didn’t know,’” Adams said. “He was always looking for the next challenge.”
Adams also notes that Wise brought a unique skill set to DCMA. About 75% of the staff are retired military, but Wise was in the minority in still being active with the Air National Guard.
“His skills are so unique, quality but also acquisitions and contracting,” Adams said. “We can’t enforce what we don’t understand. A lot of people still struggle with it, have a very strong quality background, but don’t understand the complexity of government contracting. It’s like a fire hose when you start here. Some people burn out.”
“He was a really, really good employee,” Adams said. “I’m glad he got the promotion he rightfully deserved, and I’m happy for his continued success.”
Meet Last Year's Rookie of the Year Winner

Jared Curtis
Other 2024 Winners

Dr. Milton Krivokuca

3D Engineering Solutions