NDT | XRF
From Lab to Line: Evolution of XRF in Manufacturing Quality Assurance and Control
The versatility of XRF technology extends across a wide range of industries, including automotive, aerospace, electronics, pharmaceuticals, and more.

Portable and handheld XRF analyzers are used across a wide range of industries, including scrap recycling, mining, mineral exploration, environmental analysis, and manufacturing. Source: All images used with permission from Evident
In modern manufacturing, ensuring product quality and consistency is paramount. Any compromise jeopardizes brand reputation and poses significant risks to consumer safety. To navigate this complex landscape, manufacturers have long relied on analytical techniques that offer rapid and accurate insights into material composition and integrity. Among these, X-ray fluorescence (XRF) has emerged as a reliable tool revolutionizing quality assurance and control processes across various industries. This article explores the evolution of XRF technology and its pivotal role in enhancing quality assurance and control in manufacturing environments.
The Foundation of XRF Technology
X-ray fluorescence, commonly referred to as XRF, is a nondestructive analytical technique used to determine the elemental composition of materials. The principle behind XRF is based on the interaction between X-rays and atoms within a sample. When exposed to high-energy X-rays, atoms in the sample undergo excitation, leading to the emission of characteristic fluorescent X-rays. By measuring the energy and intensity of these emitted X-rays, the elemental composition of the sample can be determined with remarkable precision.
Early XRF Developments and Applications

How XRF Can Improve Quality
Andrew Hanuszek of Evident explains what quality professionals need to know about using XRF, the role of automation, and how it aligns with today’s trends.
Listen to more Quality podcasts.
The roots of XRF technology can be traced back to the early 20th century when scientists began exploring the interaction between X-rays and matter. However, it wasn’t until the mid-20th century that significant advancements paved the way for practical applications in analytical chemistry and materials science. The development of high-energy X-ray sources and sensitive detectors laid the groundwork for the emergence of XRF as a powerful analytical tool.
Initially, XRF was primarily employed in laboratory settings for elemental analysis of geological samples, metals, and minerals. Its ability to provide rapid, nondestructive analysis made it invaluable in research and exploration endeavors. However, as manufacturing processes became increasingly sophisticated, the need for on-site, real-time analysis became apparent, leading to the evolution of portable XRF analyzers.
The Advent of Portable XRF Analyzers
The introduction of handheld XRF analyzers marked a significant milestone in the evolution of XRF technology. These compact, portable devices revolutionized the way elemental analysis was conducted, enabling rapid on-site testing in various industrial settings. Equipped with advanced X-ray sources and detector systems, handheld XRF analyzers offered versatility and convenience.
In manufacturing environments, handheld XRF analyzers found widespread adoption for quality assurance and control purposes. From verifying the composition of incoming raw materials to monitoring in-process components, these devices empowered manufacturers with real-time insights into material properties. The ability to perform nondestructive analysis directly on the production floor accelerated decision-making processes and streamlined quality control workflows.

Benchtop XRF Analyzers: Bridging the Gap
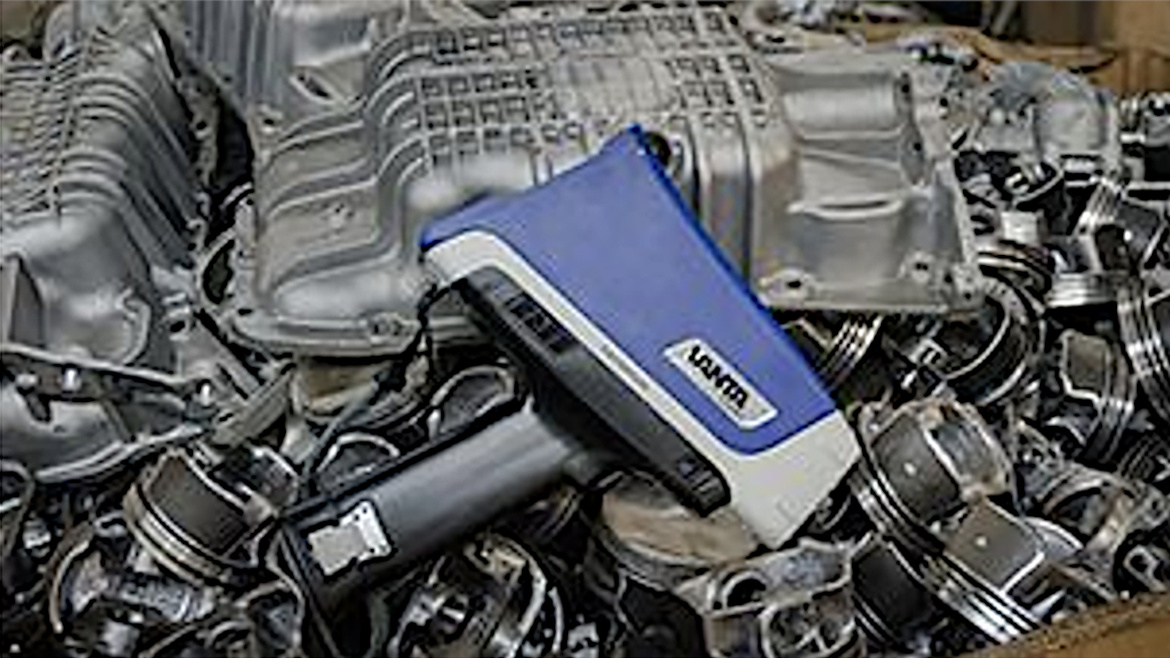
While handheld XRF analyzers offered portability and convenience, they were sometimes limited in terms of analytical performance and sample throughput. To address these challenges, manufacturers turned to benchtop XRF analyzers, which offered enhanced analytical capabilities while retaining the versatility of their portable counterparts.
Benchtop XRF analyzers are typically larger and more robust than handheld devices, enabling higher precision and sensitivity in elemental analysis. Equipped with sophisticated X-ray sources, detector arrays, and automated sample handling systems, these instruments are capable of handling a wide range of sample types and sizes. Moreover, their compact footprint makes them well-suited for integration into laboratory environments and production lines.
In manufacturing settings, benchtop XRF analyzers play a crucial role in ensuring product quality and compliance with regulatory standards. By providing accurate and reliable elemental analysis data, these instruments enable manufacturers to make informed decisions regarding raw material selection, process optimization, and product validation. Additionally, their ability to automatically analyze multiple samples enhances efficiency and throughput, thereby reducing overall production costs.
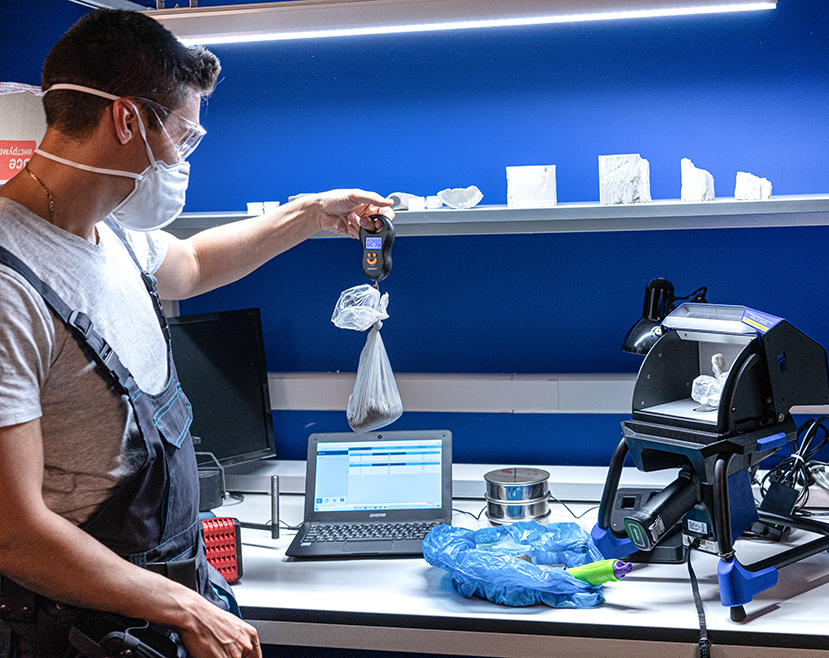
In-Line XRF Systems: Real-Time Quality Assurance
As manufacturing processes continue to evolve, there is a growing demand for real-time monitoring and control solutions. In-line XRF systems address this need by integrating XRF technology directly into production lines, enabling continuous, nondestructive analysis of materials as they are being processed.
In-line XRF systems are designed to seamlessly integrate with existing manufacturing equipment, providing real-time feedback on material composition and quality. By monitoring key process parameters in situ, these systems enable manufacturers to detect deviations from specifications and take corrective action before defects occur. This proactive approach not only minimizes scrap and rework but also helps ensure consistent product quality and compliance with regulatory requirements and traceability.
XRF Applications Across Industries

The versatility of XRF technology extends across a wide range of industries, including automotive, aerospace, electronics, pharmaceuticals, and more. In automotive manufacturing, for example, XRF analyzers are used to verify the composition of alloys in engine components, confirming optimal material performance and durability. In the electronics industry, XRF is employed to assess the purity of solder materials and detect contaminants that could compromise device reliability.
In the pharmaceutical sector, XRF technology plays a critical role in quality control processes by helping to ensure the integrity of active pharmaceutical ingredients (APIs) and excipients. By providing rapid, nondestructive analysis of raw materials and finished products, XRF analyzers help pharmaceutical manufacturers maintain compliance with stringent regulatory standards and uphold patient safety.
Future Directions and Challenges
Looking ahead, the evolution of XRF technology is poised to continue, driven by advancements in instrumentation, data analytics, and artificial intelligence. The integration of XRF with other analytical techniques, such as optical spectroscopy and mass spectrometry, holds promise for further enhancing analytical performance and expanding application capabilities.
However, as with any technology, XRF is not without its challenges. One of the primary concerns is the potential for matrix effects, where the composition and physical properties of the sample matrix influence the accuracy and precision of XRF measurements. Addressing this challenge requires ongoing research and development efforts to improve calibration algorithms and sample preparation techniques.
Conclusion
NDT
Related Articles
In conclusion, X-ray fluorescence technology has emerged as a cornerstone in the realm of quality assurance and control in manufacturing environments. From its beginnings in the laboratory to its widespread adoption in industrial settings, XRF has undergone a remarkable evolution, driven by innovation and demand for faster, more reliable analytical solutions.
Whether in the form of handheld, benchtop, or in-line systems, XRF analyzers continue to empower manufacturers with rapid, nondestructive elemental analysis capabilities. By enabling real-time monitoring of material properties and process parameters, XRF technology helps ensure product quality, safety, and compliance across a diverse range of industries. Integration of measurements provides seamless transfer of data to manufacturers’ ERP systems throughout production processes, creating a streamlined workflow from start to finish.
As we look to the future, the evolution of XRF technology holds promise for further advancements in manufacturing quality assurance and control. By embracing innovation and collaboration, manufacturers can leverage the full potential of XRF to drive continuous improvement and excellence in their operations.
Looking for a reprint of this article?
From high-res PDFs to custom plaques, order your copy today!