NDT | XRF
Ensuring the Quality of Lithium Ion Battery Manufacturing Amid Surging Demand
As the demand for Li-ion batteries continues to rise, efficient manufacturing and recycling practices become imperative.

Image Source: guteksk7 / iStock / via Getty Images Plus
Beginning with the digital revolution where cellphones, laptops and other handheld technology became commonplace, there has been a surging demand for mobile power that has driven research into improved battery performance and more efficient manufacturing. Global policies and objectives for the transition to cleaner energy and the emergence of hybrid and fully electric vehicles have exponentially increased the battery demand, intensifying the pressure on battery manufacturers to improve both product quality and process efficiency.
Lithium-ion (Li-ion) batteries power the majority of the devices we use every day, but manufacturing Li-ion batteries utilizes significant amounts of relatively scarce base metals. Mining for base metals is subject to discoverable supply, sustainability, as well as economic and geopolitical dependencies. During production, manufacturers must also ensure the highest, most reliable yield through their line, and lithium-ion battery recycling will be essential for strategic supply chains in electric vehicle manufacturing. This article will review the use of analytical technologies through the various stages of battery production and recycling to maximize Li-ion materials and optimize production.
Material Impurity Analysis & Ensuring Quality Keeps Pace with Speed
When looking to improve the reliability of production, battery manufacturers must first consider the purity of the materials and ensure there is no contaminants in the raw material that would interfere with or impact the quality of their end product. The use of handheld and lab-based analytical techniques allows manufacturers and miners to quickly and efficiently analyze raw materials to ensure that battery production is optimized from the outset.
Take graphite, for example, a mineral that commonly serves as the anode material in Li-ion batteries due to its abundance as a resource, relatively low cost, and contribution to high energy density. Wavelength dispersive X-ray fluorescence (WDXRF) is commonly used for elemental analysis, and it’s an ideal method for the analysis of graphite purity. WDXRF technology can analyze trace concentrations of a wide range of elements commonly found in graphite samples with very low limits of detection, preventing early contamination from impacting the final product.
When considering anode materials, Raman spectroscopy is an important analytical tool to characterize battery components, for example, the different allotropes of carbon [Figure 1]. Probing molecular structure and local chemical environments, Raman spectra changes can be correlated with variance in electrochemical performance and offer insight into subtle changes in materials or characterizing new anode materials.
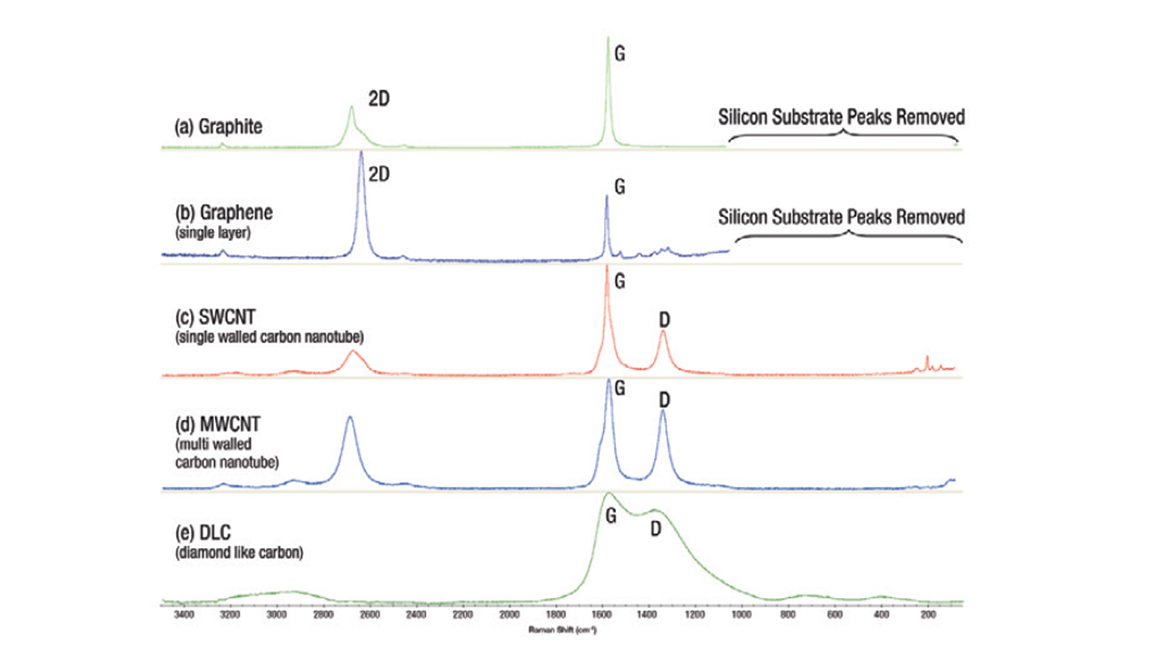
Monitoring Critical Parameters During Electrode Manufacturing
Further along in the process, during electrode manufacturing and battery slurry production, manufacturers must also ensure a number of properties are in ideal range before the mixture is applied to the electrode. Historically done through batchwise compounding of active materials that results in batch-to-batch variations, labor-intensive processes, and production downtime, manufacturers can now leverage twin-screw compounding for a continuous production process. This technique ensures high reproducibility, less cleaning time, and high material efficiency, while enabling transfer from lab processes to high-throughput production of slurries. Innovations in research-level compounding have arrived with compounders available for inclusion inside glove boxes with the capability of up to 5 kg/hr production rates.
Real-time, in-line metrology can also provide essential insights into electrode mass loading, allowing manufacturers to quickly detect non-uniformities and defects, assuring the quality of coating. By integrating the new technique of in-line mass profilometry directly into the manufacturing line, longstanding issues like high scrap rates, currently estimated between 5-30%, and unplanned downtime can be significantly reduced. In-line mass profilometry measures the mass loading of active material on the entire electrode, providing complete traceability and edge-to-edge data at a millisecond rate and exceeding the limitations of current scanning metrology that may miss large areas of the coating. Rich data collected in real-time helps assure that battery electrodes meet high quality specifications, enabling the optimization of production yield and realizing process efficiencies for continuous improvement.
When accessing the anode coating, Raman spectroscopy can also provide relative defect concentrations, indicating that the carbon coating over the anode may be impure or uneven. Yet, unlike other applications where defect-free materials are preferred, the presence of defects due to edges and vacancies in coating materials, such as graphene, actually improves electrochemical properties of the battery, potentially extending the power capacity.[1]
Use of Handheld X-ray Fluorescence Analysis in Lithium-ion Battery Recycling Operations
When considering battery end-of-life, there are a number of elements that can be reused from the initial battery. Multiple recycling processes involving combinations, including, in some cases, thermal, and mechanical treatments, pyrometallurgy or hydrometallurgy seek to maximize the recovery of these materials, but it is worth mentioning that not all recycling processes are economically viable for every type of cathode material.
Li-ion batteries are made of multiple components, and the most valuable one is the cathode which can concentrate 40% to more than 70% [2,3] of the value of the battery depending on its chemistry. The more commonly used Li-ion batteries cathode active materials for electric vehicles are lithium nickel cobalt manganese oxides (NCM) with 66% followed by lithium iron phosphates (LFP) with 24% and lithium nickel cobalt aluminum oxide (NCA) with 10% [2].
Delivering fast and accurate results, handheld X-ray fluorescence analysis (see figure 2) is a type of elemental analysis that has proven to be efficient in other recycling areas such as scrap metal and automotive catalytic converters. Although this technology does not detect lithium, it can measure most elements from the periodic table between magnesium and uranium including nickel (Ni) or cobalt (Co) which both often represent much higher value than lithium in an Li-ion battery [3].
Handheld XRF analysis is mostly used upstream of the recycling process, to identify the type of cathode scrap films from gigafactories, which represents as of 2023 around 70% [3] of the feedstock in battery recycling. Identifying the type of cathode material (figure 2) is essential to select the appropriate recycling process. For example, pyrometallurgy (smelting) can be very efficient to recover nickel and cobalt from NCM cathode films. Yet it would not be adequate in the case of LFP cathode films, because lithium - the only commodity of high value - is lost within the slag. In the case of LFP, the cost of processing the slag via hydrometallurgy, including energy and chemicals, exceeds the value of the recovered product.
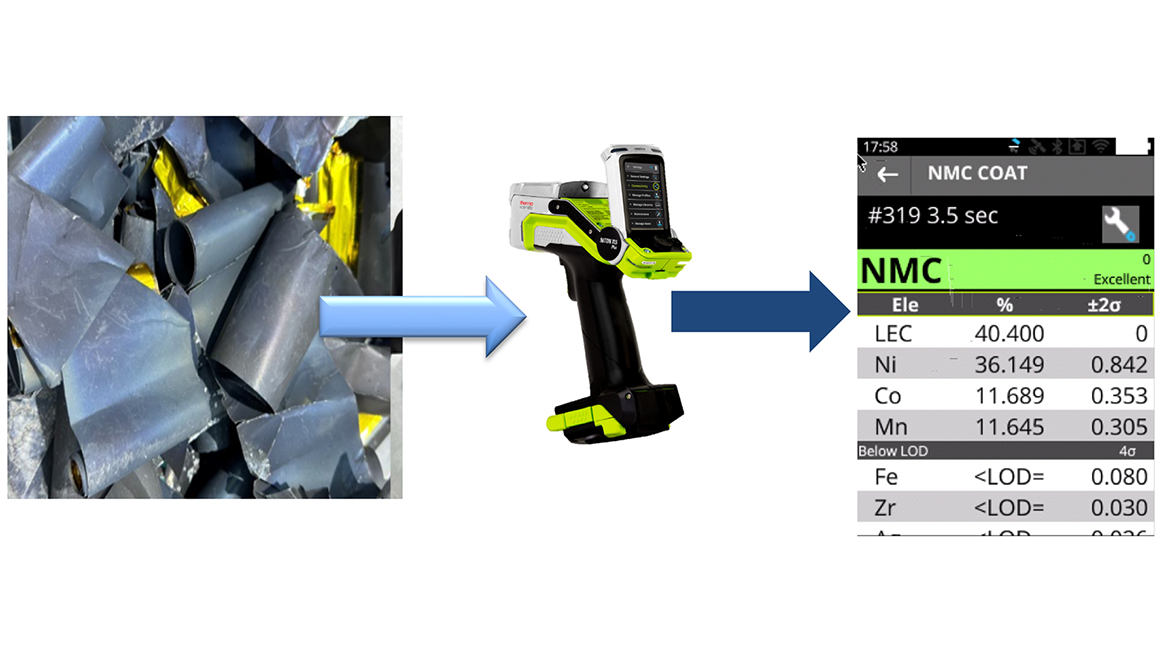
Materials Recovery from Spent Batteries
The remaining 30% of the Li-ion battery recycling feedstock [3] comes from the recycling of end-of-life batteries from either consumer products or electric vehicles. Those spent batteries generally undergo mechanical processing including shredding, magnetic separation and separation upon density and particle size. This results in a number of various recovered products, including battery shells, aluminum and copper from the current collector, as well as the black mass, which will undergo further hydrometallurgical processing to recover pure compounds.
Analyzing the recovered product using HHXRF provides information for risk assessment, adequate material treatment and process efficiency. Black mass is certainly the most valuable product recovered. The amount of nickel, cobalt and manganese and other elements (see figure 3) can be rapidly measured with minimal sample preparation to help assess their economic value.
Recycling is a critical link in the Li-ion battery value chain and the use of handheld XRF provides recycling companies with critical information about the type of scrap cathode films and the composition of recycling products including battery shells, copper and aluminum from current collectors, and black mass. This information helps companies estimate the economic value of the recycled products and to make fast decisions in selecting the appropriate recycling process and measuring the process’ efficiency.
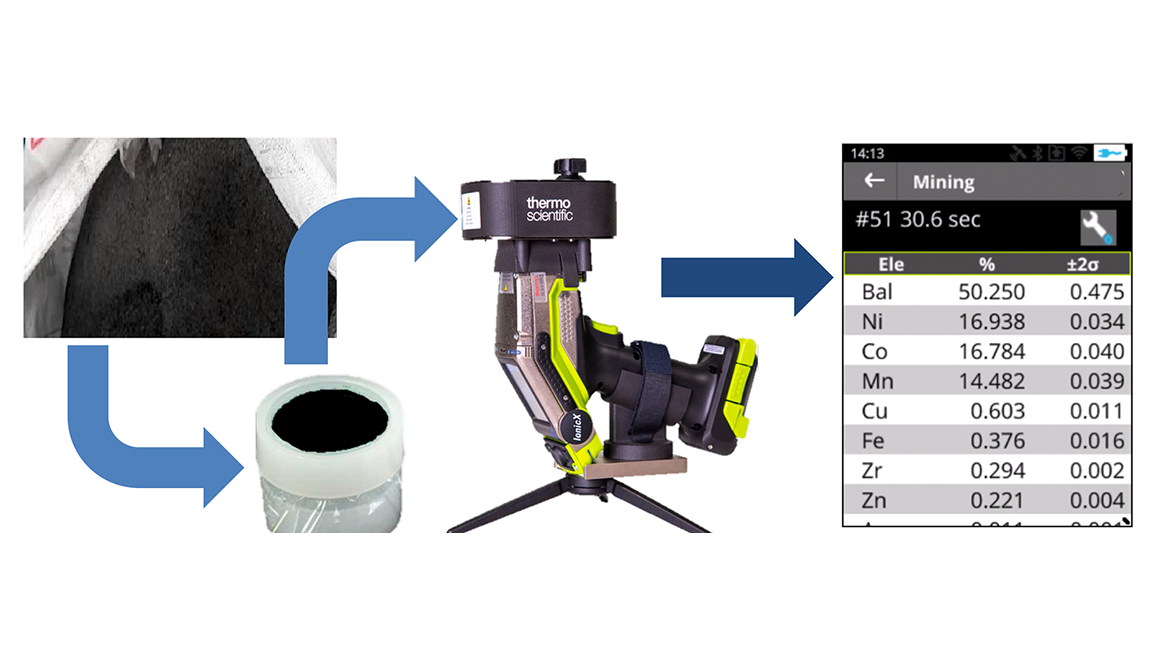
Supporting Heightened Analysis from Line to Landfill
While other materials for battery power are currently under development, it will be years before these alternatives come to fruition. The related demand in Li-ion batteries will only continue to grow, making it imperative for battery manufacturers to maximize their yields and recover materials after end-of-life where possible.
From ensuring material purity to monitoring critical parameters during manufacturing, techniques like in-line mass profilometry, XRF analysis and Raman spectroscopy offer insights crucial for optimizing processes and maximizing yields. As the demand for Li-ion batteries continues to rise, efficient manufacturing and recycling practices become imperative. By leveraging advanced analytical techniques from production to end-of-life, battery manufacturers can not only meet the escalating demand but also contribute to sustainable resource management and environmental conservation. Thus, supporting heightened analysis from line to landfill is crucial for ensuring the longevity and sustainability of the Li-ion battery industry in the years to come.
REFERENCES
[1] Timothy N. Lambert, Claudia C. Luhrs, Carlos A. Chavez, Stephen Wakeland, Michael T. Brumbach, Todd M. Alam, Carbon, 48, 2010, 4081-4089.
[2] Heiner Heimes et al., Recycling von Lithium-Ionen-Batterien, 2. Edition, Dec 2023, PEM RWTH Aachen University & VDMA, ISBN: 978-3-947920-43-3
[3] Julia Harty, Six key trends in the battery recycling market, June 2023, Fastmarkets, https://www.fastmarkets.com/insights/six-key-trends-battery-recycling-market/
Looking for a reprint of this article?
From high-res PDFs to custom plaques, order your copy today!