NDT | Back2Basics
Advancements in Semi-Automated Ballistics Assessment: The Role of CT X-ray NDT
High energy CT X-ray NDT can provide detailed internal imaging of critical defense components.

All Images Source: North Star Imaging
Safe, accurate, and thorough assessments of military and defense assets, particularly ballistics, is critical. From ammunition to explosives to body armor, the performance and integrity of these critical components can mean the difference between success and failure on the battlefield. Advanced Computed Tomography (CT) X-ray nondestructive testing (NDT), particularly high energy (9MeV), has revolutionized inspection of ballistics. With advancements in robotic systems integration, quality control and personnel safety has increased. Here we explore ballistics applications and robotics integration that allow for the semi-automated loading and scanning in modern manufacturing. Lastly, we will briefly cover the integrated engineering approach of developing these processes.
Ballistics Quality Control with CT

Ammunition Assessment
The reliability and effectiveness of ammunition are crucial factors in any military operation. CT X-ray NDT provides a nondestructive method for inspecting ammunition, allowing for detailed analysis of internal structures such as casings, propellants, and projectiles. By generating cross-sectional images, CT scanning enables inspectors to detect defects, irregularities, or foreign objects that may compromise the ammunition’s performance or safety. This technology facilitates quality control processes, ensuring that only defect-free ammunition reaches end users, enhancing reliability and safety.
Ballistics Helmets and Body Armor
Protective gear, such as ballistic helmets and body armor, must meet stringent safety standards to effectively protect military and law enforcement personnel. CT X-ray NDT provides a comprehensive method for evaluating these protective components’ structural integrity and performance. Detailed imaging can identify defects, delaminations, or material inconsistencies that may compromise their protective capabilities. Manufacturers can leverage this technology to maintain high safety and reliability standards for their products.
Missiles, Rockets, and Torpedoes
The complex and high-performance nature of missiles, rockets, and torpedoes necessitates precise inspection techniques to ensure operational readiness and reliability. CT X-ray NDT enables inspectors to conduct thorough assessments of these aerospace and maritime weapons systems without compromising their integrity. By examining internal components such as guidance systems, propulsion mechanisms, and warheads, CT scanning can identify defects, anomalies, or assembly errors that may affect performance or safety. This technology plays a crucial role in quality assurance processes, helping to mitigate risks and enhance mission success rates.

Bombs, Mines, and Grenades

The detection and disposal of explosive devices present significant challenges for military and security forces worldwide. CT X-ray NDT offers a valuable tool for inspecting bombs, mines and grenades, allowing for detailed analysis of their internal components and explosive payloads. By generating precise images of circuitry, detonators, and casing structures, CT scanning enables inspectors to assess the integrity and functionality of these devices without resorting to destructive methods. This capability enhances the safety and effectiveness of bomb disposal operations, reducing the risk of accidental detonations and casualties.
Integration of Robotics with CT X-ray Systems
In modern semi-automated manufacturing environments, integrating robotics with CT X-ray systems significantly enhances quality control processes.
Robotics can precisely handle, load, and position components for CT scanning, reducing human error, increasing throughput, and in the case of ballistics handling, increasing safety. Automated systems can consistently align objects, ensuring optimal imaging angles and reducing variability in inspection results.
The combination of robotics and CT X-ray systems enables continuous and efficient inspection processes. Automated systems can operate around the clock, increasing inspection throughput and reducing bottlenecks in the production line. This integration is particularly beneficial for high-volume manufacturing environments where speed and consistency are paramount.
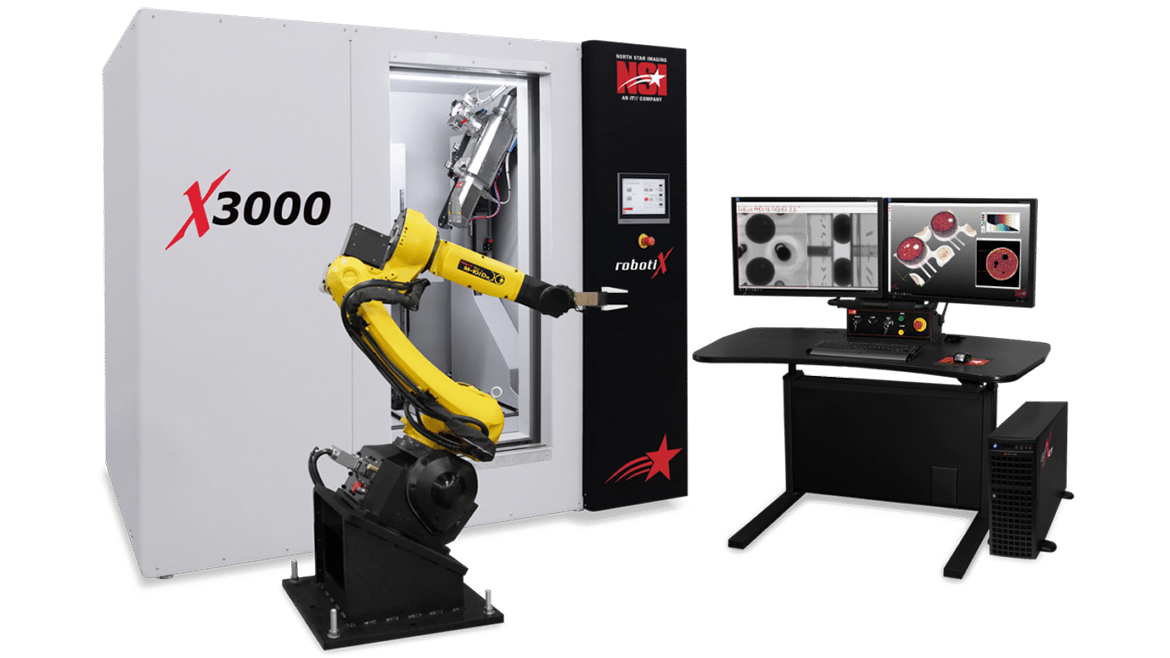

Improved Data Analysis and Decision-Making
Robotics integrated with CT X-ray systems can be equipped with advanced data analysis algorithms utilizing the latest advancements in AI and machine learning (ML). These systems can quickly process imaging data, identify defects, and categorize inspection results. Automated decision-making capabilities allow for real-time quality control adjustments, ensuring that only components meeting stringent standards proceed to the next production stages. The results can be reviewed and next level decision-making can be made by the CT experts on site to determine the overall integrity and safety of the ballistics being inspected.
Process Development
It is important that an integrated team of manufacturing engineers and CT experts come together to develop these processes. By utilizing existing high energy scanning facilities and expertise, manufacturers can configure the optimal CT system, set up, and robotic handling to be integrated into their manufacturing environment.
Conclusion
High energy CT X-ray NDT has revolutionized the assessment of various ballistics applications, providing nondestructive and detailed internal imaging of critical defense components. From ammunition to missiles, this technology enhances reliability, safety, and performance through comprehensive inspections. Integrating robotics with CT X-ray systems further augments quality control processes in semi-automated manufacturing environments, improving efficiency, throughput, and data-driven decision-making. As advancements in CT imaging, robotics, and software continue to evolve, their combined impact on ballistics assessment will further enhance the capabilities and readiness of defense and security forces.
Looking for a reprint of this article?
From high-res PDFs to custom plaques, order your copy today!