Test & Inspection
Leak Testing EV Battery Cells and Modules Is Critical to Avoiding Defects
The leak testing industry has progressed to where electrolyte leak testing of every cell can be performed at production line speeds.

Image Source: Shutterstock
As the mobility industry in North America grows, the necessity for battery cell leak testing is often underappreciated or not widely disseminated within organizations. Whether testing a cell, a module or an assembled battery pack, at each stage proper leak testing can help avoid costly and reputation-damaging defects.
We need to remember the pain experienced by the air bag inflator industry, where humidity ingressing into driver side pyrotechnic inflators over many years, even decades, reacted negatively and even now continue to inflict damage. The immediate corollary in the traction battery industry may be “thermal events” such as the recent fire in a Korean parking structure. Embracing leak testing of both cells and modules for water vapor ingress is a solution that can speed adoption of New Energy Vehicles.
Available research published by SAE has explained how invisible porosities can lead to cell degradation through either water ingress, or even ingress of water vapor. Water ingress more highly affects the battery pack as the packs, regardless constructed of steel, plastic or aluminum, each have low acceptable limits for defect size. A relevant metric for individual cells is that that defects greater than single-digit micron(s) potentially invites atmospheric moisture to invade individual battery cells and create hydrofluoric acid.
Battery production in North America relies upon joint ventures between auto OEMs and battery manufacturers. Completed battery cells arrive at module assembly facilities, ready for assembly into modules. Within most battery production facilities, it’s understood that individual cells should be tested for electrolyte leaks as a final step in that process. Naturally, those cells need to be electrically connected to produce the correct voltage. Often overlooked is that module assembly itself presents a new opportunity to create defects when connecting multiple cells. It is therefore desirable to test each module in a final electrolyte leak test before any electrical function testing.
Problems in module assembly, process challenges
Assembling multiple cells of any type into a module requires welding, whether lasers, ultrasound or resistance, and each connection method has its own challenges specific to cell type. That challenge may be excessive heat affecting delicate cell layers, tolerance gaps between foil and dissimilar metal surfaces, or even surface oxidation. Assuming successful welds, ones that are not electrically intermittent or above spec in resistance, there’s always the problem of weld cracks or tab detachment. With hundreds, even thousands of welds per pack, a statistically small percentage of faulty welds presents enormous potential difficulty whether reputation, warranty or negative events.
These facilities are highly automated with little human interaction, so bits and pieces move from Station 1 to Station 2 and soon an assembled module, all its tabs welded, appears and is ready for quality assurance testing. A common way to test the completed module is an electrical function task.
So, you send the module to a station and the robot hooks up. There, with 12 or 16 cells that are all bonded together, you’ve got a Plus and a Minus terminal. The robotic test station hooks on, looking at charge-discharge with certain performance indicators proprietary to each facility. There, the electrical function test says “good battery, bad battery.” If it fails, the robot at the module testing station puts it in a stack of failed modules and this happens all day, every day, in every plant. You must find leaks at your earlies opportunity, ideally at the end of the production line. Electrical function tests will expose gross leaks, while minute leaks—which lead to degradation over time—have yet to be exposed. Without leak testing, problems with small, but significant leaks, will then be exposed in the field and likely while in customer’s possession.
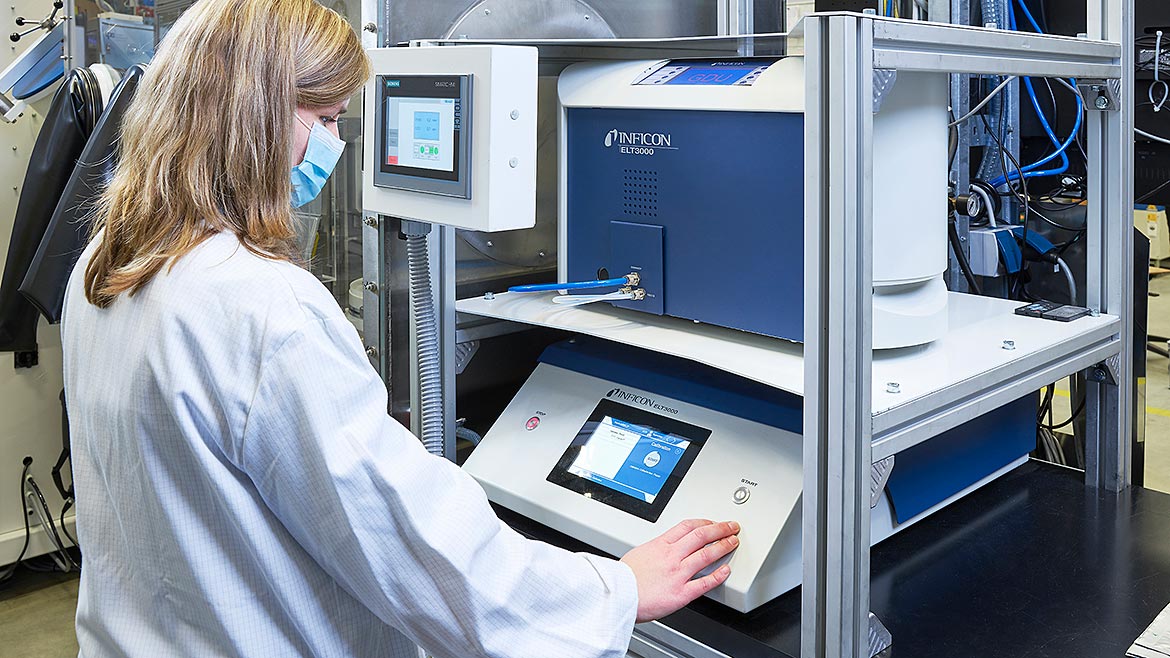
When the technician goes out to look at grossly “failed” modules, the technician can often visualize that some of these cells are swollen. Some of these cells may have visual electrolyte leaks, oozing electrolyte out of the individual cells. So, “Wow, we found these leaks, but we wasted all this time.” There’s a definable value to catching that leak earlier as facilities can leak test every module with a throughput of around two minutes. Think about that in relation to electrical function tests which may require just 10 minutes or up to a full hour, depending on the manufacturer. Finding leaks earlier in the process allows manufacturers to save money because every production slot has value. The further something goes down that production line, the more value is accumulated. The sooner you can find leaks the better.
Quality originates at the loading dock where containers of hundreds of cells arrive, and quickly. Failure of any kind slows output as, for instance General Motors’ Ultium battery packs have 144 cells in a 50-kW battery or 576 cells in their largest, 200-kW battery pack for the GMC Hummer, with many variants between. So, when you’re looking at production speeds, you’re looking at the daily output of battery packs which is that “queen size mattress.”
For plant managers, the metrics of importance are yield and production throughput. Their incoming material, those individual cells help to figure out how large of a batch to test if yield is below standard. A test batch might be as few as two or far more, but yield is going to help determine how big the batches can be. To give an example in another part of the world, look at earbuds. It’s very easy to leak test the batteries in each of these earbuds in batches because the parts are small. And a batch of 40 or 50 coin cells will go into a test chamber for Go/No-Go testing. If a test of 40 fails, it’s split to 20 and set up so that once it narrows down those bad cells, it kicks them out. That company decided, based on their yield, that the optimal number is 40 or 50 cells at a time. Yield will determine your batch size.
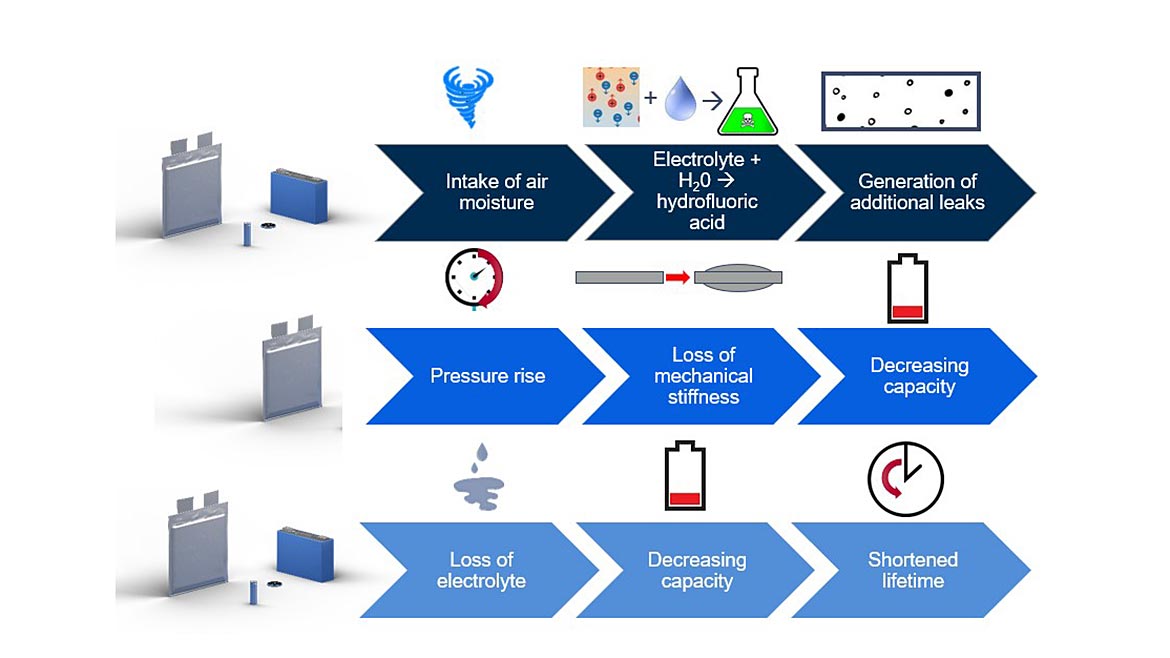
Unfortunately, in some instances, plant managers are having to become adamant about their supplier(s) leak testing each cell before shipping, “Because I’m putting too much value in assembling this module only to have it fail at electrical function testing.” Let’s start moving back upstream and finding leaks earlier. Fortunately, the leak testing industry has progressed to where electrolyte leak testing of every cell can be performed at production line speeds. Further, and after module assembly but before electrical function testing, every module can be rapidly leak tested.
This technology can detect electrolyte leaks down to the micrometer level, which is 1,000 times smaller than those detected by conventional air testing or pressure decay methods. Cells with structure, like prismatic cells, can be pre-tested before filling. After electrolyte filling, sealing and formation, all types of cells can be tested and avoid the cost and risk of formation of faulty cells. Cells also might be tested for electrolyte leaks after forming and aging, which ensures leak-free cells are shipped. Additionally, by using three test chambers on fully automated production lines, batches of cells can be tested, as may be completed modules. The aim is to minimize scrap at every step of production while maintaining production line speeds.
Path to the future
We have in North America, committees working on establishing safety standards, but committees and standards aren’t enough. There’s still a general lack of awareness of the need for leak testing for metal-ion batteries, particularly in educating industry about water vapor ingress, what size leaks matter and how individual battery chemistries matter. For instance, one battery chemistry may be affected by 20 PPM of water vapor while another may have a tolerance up to 80 or even 100 parts per million of water vapor: there are no easy answers.
Unfortunately, in the New Energy Vehicle space, more car fires are materializing, such as an EV catching fire while on a lift at a dealership in Carmel, Indiana, and firefighters using a forklift to move the vehicle, and after hurricane Helene, another EV fire caused by flooding occurred in Pinellas County, FL. With hurricanes causing flooding, more people launching boats and traversing creeks in their New Energy pickups and SUVs, as these numbers increase these events are going to multiply.
Testing every metal-ion battery for leak tightness is necessary and it’s just good business.
Looking for a reprint of this article?
From high-res PDFs to custom plaques, order your copy today!