Medical
Industrial Finishing of Medical Parts and Components: Advances in Technology and Methods
A key consideration for medical device OEMs is the ability to scale up additive parts production without sacrificing quality.

Image Source: Rösler / AM Solutions
The importance of precision, durability, and safety cannot be overstated in the medical device industry. As medical devices become smaller, more intricate, and increasingly reliant on advanced materials, the finishing processes that ensure their functionality and biocompatibility are more critical than ever.
This article will explore how mass finishing technologies, shot blasting, and bespoke solutions for additive manufacturing (AM) parts play a pivotal role in the final stages of medical device production. By focusing on the advances in these finishing techniques, we aim to provide medical device OEMs with insights into how modern finishing processes support innovation, improve efficiency, and ensure compliance with stringent regulatory standards.
THE ROLE OF INDUSTRIAL FINISHING IN MEDICAL DEVICE MANUFACTURING
Medical devices range from simple surgical tools to complex implantable devices, all of which require precise and consistent finishes to meet both functional and aesthetic requirements. In medical applications, finishing is more than just a cosmetic touch, it ensures smooth surfaces free of burrs and sharp edges, promotes biocompatibility, and optimizes the mechanical properties of the device.
Given the critical nature of these devices, the finishing process must ensure that each part meets the highest possible standards. Industrial finishing technologies have evolved significantly over the past few decades, responding to the need for more precise, consistent, and scalable solutions. Whether it’s through traditional mass finishing methods, the versatility of shot blasting, or the bespoke processes required for AM-produced parts, each technology offers distinct advantages for medical device manufacturers.
MASS FINISHING — EFFICIENCY AND PRECISION IN BULK
Mass finishing is a highly efficient and effective process for deburring, polishing, and cleaning medical parts, especially when dealing with high-volume production. This technology utilizes abrasive media in a vibratory or tumbling process to refine the surface of multiple components simultaneously. The ability to process thousands of parts at once makes mass finishing a popular choice for medical device OEMs producing surgical instruments, implantable devices, or any product that requires uniform finishing across numerous identical parts.
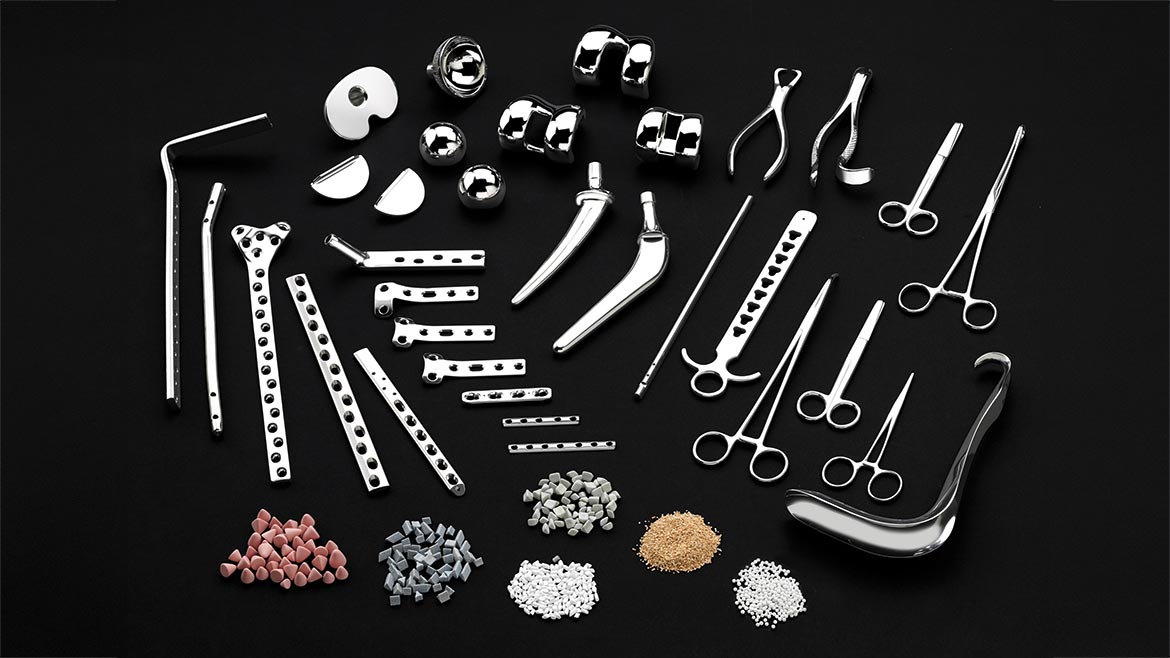
While the basic mechanics of mass finishing involve the movement of abrasive materials across the surface of the parts, the real advances lie in the development of specialized media, compounds, and equipment. Today, media can be precisely tailored to the material of the medical part — whether it’s stainless steel, titanium, or plastic — and can achieve a range of finishes from rough to mirror-polished, depending on the needs of the device.
For medical device manufacturers, the primary advantage of mass finishing is its ability to scale up without sacrificing quality. With consistent results across large batches, manufacturers can reduce the time and labor costs associated with manual finishing processes. Furthermore, this automation minimizes the risk of human error, ensuring that each medical part meets stringent quality standards.
However, mass finishing is not just about efficiency. Medical parts often require highly specific surface finishes to ensure optimal performance. For example, a surgical tool may need a high-gloss polish to reduce friction and improve cleaning efficiency, while an implant might require a textured surface to promote tissue integration. Modern mass finishing technologies allow for this level of customization, ensuring that the final product is both functional and biocompatible.
SHOT BLASTING — HIGH-PRECISION SURFACE TEXTURING
Shot blasting is another finishing process widely used in the medical device industry, particularly for applications where precise surface texturing is required. Unlike mass finishing, which involves the interaction of multiple parts with abrasive media, shot blasting is a more controlled process that uses high-speed media (such as glass beads, ceramic, or metal shot) propelled at the surface of a part. This technique is highly effective for cleaning, deburring, and creating specific surface finishes, especially for more complex geometries.
One key advantage of shot blasting is its ability to create surfaces with a high degree of uniformity and consistency, even on intricate or irregularly shaped parts. For medical devices, this precision is critical, especially for parts that must meet tight tolerances or have specific surface textures that aid in their function. For example, implantable devices often require a roughened surface to enhance osseointegration, while surgical tools may need surfaces that are highly polished and smooth for ease of sterilization.
Advancements in shot blasting technology have further expanded its capabilities. Modern shot blasting systems can now offer greater control over the intensity and direction of the blast, allowing manufacturers to target specific areas of a part without affecting its overall integrity. Additionally, advancements in media types, including biodegradable and biocompatible options, offer further benefits for medical device manufacturers concerned with sustainability and regulatory compliance.
For medical device OEMs, the precision and repeatability of shot blasting are essential. Not only does this process provide a high level of control over the surface finish, but it also reduces the need for post-processing, helping to streamline the manufacturing process, and reduce costs. As medical devices become more complex and their functional requirements more stringent, shot blasting will continue to play an important role in ensuring that these devices perform as intended.
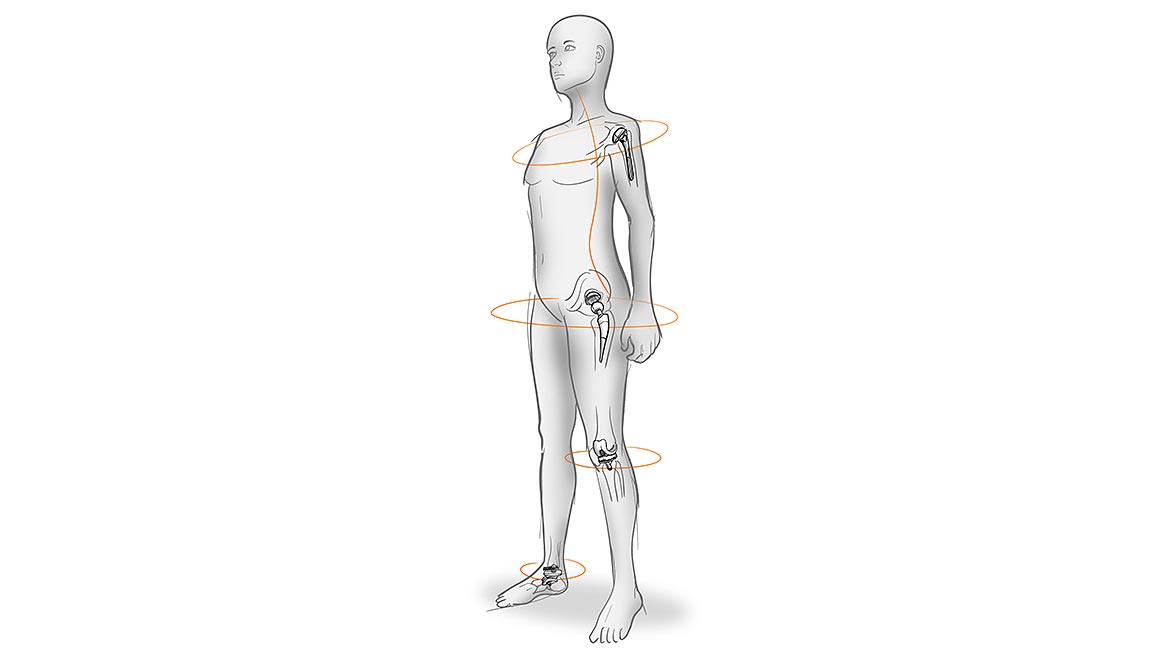
BESPOKE FINISHING FOR ADDITIVE MANUFACTURING (AM) MEDICAL PARTS
As the adoption of additive manufacturing (AM) in the medical sector accelerates, the need for bespoke finishing solutions tailored to 3D-printed parts is growing. Unlike traditional manufacturing methods, where parts are machined from a solid block of material, AM builds parts layer by layer, often resulting in rough or uneven surfaces that require additional finishing before they can be used in medical applications.
AM-produced medical parts, particularly those made from complex geometries or advanced materials like biocompatible metals and ceramics, present unique challenges when it comes to finishing. Standard mass finishing or shot blasting techniques may not always be suitable for these parts, and as such, bespoke solutions are often required to achieve the desired surface finish.
Bespoke finishing processes for AM parts often involve a combination of mechanical, chemical, and thermal treatments. These processes can include everything from micro-deburring and electropolishing to laser finishing and chemical surface treatments, all designed to refine the surface of the part to meet strict medical standards. Given the custom nature of AM parts, finishing solutions must be highly adaptable, ensuring that each part, no matter how complex, achieves the required surface quality.
One significant advantage of bespoke finishing for AM parts is the ability to tailor the surface properties of the part to its specific application. For example, implants can be finished with a porous surface to encourage bone growth, while surgical tools can be polished, as previously mentioned, to a high shine for ease of sterilization and handling. By providing a customized finishing solution, manufacturers can ensure that their AM parts meet both the functional and regulatory requirements of the medical device industry.
Another key consideration for medical device OEMs is the ability to scale up production without sacrificing quality. Bespoke finishing processes, though often more time-intensive than mass finishing or shot blasting, can be integrated into automated production lines, allowing manufacturers to maintain efficiency while still meeting the unique demands of AM-produced parts. Additionally, advances in digitalization and robotics are helping to make these bespoke processes more scalable, enabling manufacturers to meet the growing demand for customized medical devices.
THE FUTURE OF INDUSTRIAL FINISHING FOR MEDICAL DEVICES
As medical device technology continues to advance, so too will the finishing processes required to bring these devices to market. The increasing complexity of medical parts, combined with the rise of AM and other advanced production methods, will drive further innovation in finishing technologies. In particular, we can expect to see greater automation, more precise control over finishing parameters, and an increased focus on sustainability.
For medical device OEMs, staying ahead of these trends will be essential. By adopting the latest finishing technologies and working with experts in the field, manufacturers can ensure that their devices meet the highest standards of quality and safety, while also improving efficiency and reducing costs. Whether through mass finishing, shot blasting, or bespoke solutions for AM parts, the finishing process will continue to play a crucial role in the development and production of the next generation of medical devices.
SUMMARY
The industrial finishing of medical parts is a dynamic and evolving field, one that is critical to the success of medical device manufacturing. Advances in mass finishing, shot blasting, and bespoke AM solutions are helping to drive innovation, improve efficiency, and ensure compliance with the stringent standards of the medical industry. For OEMs, understanding and investing in these technologies will be key to staying competitive in an increasingly complex and demanding market.
Looking for a reprint of this article?
From high-res PDFs to custom plaques, order your copy today!