Management
Trends in Manufacturing: Advances in Technologies and Methodologies
As globalization continues to influence manufacturing practices, organizations must remain adaptable and resilient in the face of change.
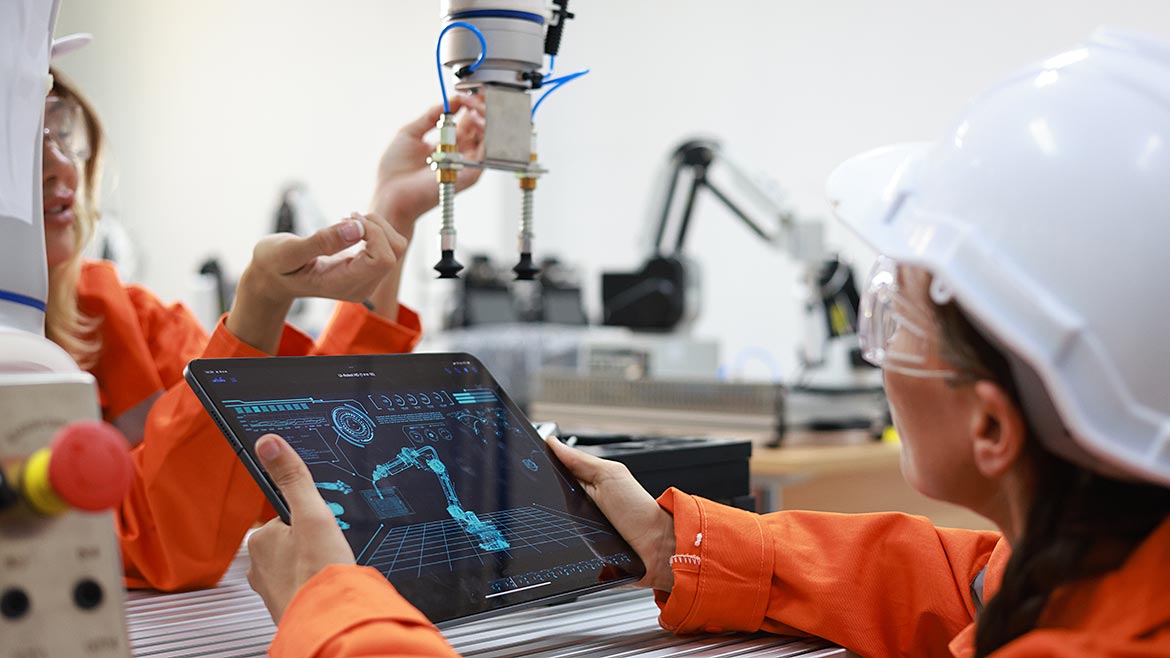
Image Source: onuma Inthapong / E+ / Getty Images Plus
Manufacturing has undergone a significant transformation in the past few decades. Technological advancements, globalization, and shifts in consumer demands all have had an impact and have forced manufacturers to adapt if they want to stay competitive. As part of this process, several trends have emerged that are redefining the landscape of manufacturing.
Technological Advancements:
Industry 4.0
Industry 4.0 is characterized by the integration of digital technologies such as the Internet of Things (loT), artificial intelligence (Al), big data, and automation into manufacturing systems. Often referred to as the Fourth Industrial Revolution, Industry 4.0 represents a fundamental shift in how manufacturing and production processes are conceived and executed.
At its core, Industry 4.0 aims to create “smart factories” where machines, devices, and systems communicate and collaborate seamlessly. The backbone of this interconnected system is the loT, which enables physical objects to connect to the internet, facilitating real-time data exchange. Examples are position sensors, CNC machines, robots, RFID tags and vision systems.
One of the most significant advantages is the potential for increased efficiency and productivity. By feeding data to Al driven analytic software, manufacturers can gain insight into operational performance, identify inefficiencies, and make data-driven decisions in real time. For example, ready access to Overall Equipment Efficiency (OEE) data can provide early warning of increased downtime, longer cycle times or reduced quality. Another example would be data collection used for predictive maintenance. Sensors can detect equipment malfunctions before they result in costly breakdowns, reducing downtime and costs.
Moreover, Industry 4.0 promotes customization and personalization in manufacturing. Traditional mass production methods are great for standardized products, but the integration of advanced technologies allows for more flexible production processes. Companies can create specialized products at scale, catering to individual customer preferences. This shift not only improves customer satisfaction but also drives competitive advantage in a crowded marketplace.
However, the transition to Industry 4.0 is not without its challenges. One of the most pressing concerns is the potential impact on employment. As automation and Al technologies become more prevalent, there is a fear that many jobs may be displaced. While it is true that certain roles may become obsolete, it is essential to recognize that new job opportunities will also emerge. The demand for skilled workers who can manage, maintain, and innovate within these advanced systems will increase, necessitating a workforce equipped with the right skills.
Data security is another significant challenge. The interconnected nature of smart factories makes them vulnerable to cyberattacks, potentially leading to catastrophic consequences. Ensuring robust cybersecurity measures and safeguarding sensitive data will be paramount as companies embrace these technologies.
Advanced Robotics
Advanced robotics refers to cutting-edge technologies and innovations to further advance standard robots that have been around for decades. Latest technology robots often integrate Al, machine learning, and advanced sensors to perform complex tasks autonomously or with minimal human intervention.
One significant advancement is the development of collaborative robots, or cobots. While traditional robots are characterized by their robustness and ability to handle heavy payloads, cobots are designed to take on intricate, repetitive or dangerous tasks in collaboration with human operators within a manufacturing cell. This frees humans to focus on more strategic activities within the process, thus amplifying their capabilities and increasing productivity.
Another key aspect is the use of robotic vision systems, which enable robots to interpret and understand their surroundings. This capability is essential for applications like quality control, where robots can detect defects in real-time, or in autonomous vehicles, where navigation depends on environmental awareness.
Moreover, advanced robotics can adapt to changing conditions. With the incorporation of machine learning, robots can improve their performance over time by learning from experience, making them more versatile and effective.
Additive Manufacturing
Additive manufacturing, or 3D printing, is revolutionizing the production of complex parts and prototypes. This technology allows manufacturers to create components layer by layer, significantly reducing material waste and lead-times.
Additive manufacturing is particularly useful in decreasing time and expense to market for new product development. Prototypes needed for proof of concept can now be printed, eliminating the costly and time-consuming need to develop specialized tooling. Design changes to prototypes can be made quickly and inexpensively, so when tooling is designed for final production product, it is right the first time.
3D printing is now available in a wide range of materials and sizes, lending itself to not just prototypes, but also to production parts. Industries such as aerospace, automotive, and healthcare have embraced 3D printing for its ability to produce lightweight, custom parts quickly. Technology has matured to the point that the potential for mass customization becomes increasingly feasible, aligning production with individual customer needs.
Evolving Methodologies:
Lean Manufacturing
Lean has been around for decades and originates from the Toyota Production System, which emphasized waste reduction. While the evolved Lean mindset is still concerned about waste, it also emphasizes value creation for customers, i.e. eliminating activities the customer would not be willing to pay for.
Another evolution is simply that more and more manufacturers are coming around to the benefits of Lean, i.e., investments made in lean practices are yielding significant ROI, improving flexibility, and increasing customer satisfaction.
Here are some key trends and developments in Lean’s evolution.
- Emphasis on Value Creation: Traditional Lean primarily focused on waste reduction. The evolved Lean mindset emphasizes value creation for customers, encouraging organizations to identify what customers truly value and align processes to deliver that value effectively. This shift promotes a more customer-centric approach to operations.
- Value Stream Mapping (VSM): VSM helps organizations identify inefficiencies and waste in their processes, leading to streamlined operations. VSM is being enhanced with data analytics and digital tools that visualize the entire production process in real-time, leveraging the data to identify inefficiencies quickly and to streamline workflows on a continuous basis.
- Cultural Transformation/Employee Empowerment: Evolved Lean methodologies place a stronger emphasis on creating a culture of continuous improvement and employee engagement. Traditional Lean focused on tools and techniques, while modern Lean fosters an environment where all employees are encouraged to contribute to improvements, enhancing overall organizational culture and morale. Teams are encouraged to take ownership of processes and actively participate in problem-solving. Some companies even encourage shop floor workers to set aside 10-15 minutes of each day to identify and implement small improvements.
Agile Lean
Agile Lean is a methodology that combines the principles of Lean manufacturing with Agile Project Management which emphasizes responsiveness and flexibility. This methodology enables manufacturers to adapt quickly to changing consumer demand and market conditions. By fostering cross-functional teams and leveraging technology, organizations can respond rapidly to shifts in product requirements or supply chain disruptions.
- Customer Focus: Both Agile and Lean emphasize delivering value to customers. Agile focuses on customer collaboration and iterative feedback, while Lean prioritizes eliminating waste to enhance value.
- Continuous Improvement: Lean principles advocate for constant evaluation and improvement of processes. Agile promotes iterative cycles, allowing teams to refine their products based on user feedback and changing requirements.
- Cross-Functional Teams: Agile Lean encourages collaboration among diverse teams, ensuring that all stakeholders (engineering, operations, sales and supply chain) work together towards common goals.
- Waste Reduction: Like traditional Lean, Agile Lean aims to minimize waste in all forms - time, materials, and resources - by streamlining processes and eliminating non-value-added activities, leading to faster delivery.
Workforce Development
- Skills Development: As technology becomes more prevalent in manufacturing, the demand for skilled labor is increasing. Traditional manufacturing roles are being replaced by positions that require advanced technical skills. People with these skills are in short supply and competition for them is fierce. In response, manufacturers are investing more heavily in workforce development programs to ensure that employees possess the necessary skills. Collaboration with educational institutions and workforce development organizations, apprenticeship programs, development of solid hands-on training programs, and online training programs all are providing employees with real-world experience, preparing them for careers in advanced manufacturing.
- Leadership Development: As experienced leaders become increasingly hard to find, many companies are promoting from within to fill supervisor and lead roles. However, good shop floor workers do not necessarily equate to good managers. Manufacturers are increasingly looking to leadership development training like TWI and DDI to help their new and inexperienced leaders to be more effective managers and trainers.
Conclusion
The manufacturing landscape is undergoing a profound transformation, driven by technological advancements, evolving methodologies, and shifting consumer expectations. Industry 4.0 technologies, advanced robotics, and additive manufacturing are reshaping production processes, while methodologies like lean, agile manufacturing and workforce development enhance operational efficiency.
While the benefits are substantial, the challenges associated with workforce displacement, workforce development, and data security must be addressed proactively.
As globalization continues to influence manufacturing practices, organizations must remain adaptable and resilient in the face of change. By embracing these trends and fostering a culture of innovation, manufacturers can position themselves for success in an increasingly competitive and dynamic market.
Looking for a reprint of this article?
From high-res PDFs to custom plaques, order your copy today!