Machine Vision
How Closed Loop Quality and AI-Driven Machine Vision are Transforming Manufacturing
Unlike traditional quality control methods, closed loop systems enable real-time adjustments and proactive problem-solving.

Image Source: Elementary ML
As industries grapple with the dual challenges of maintaining impeccable quality standards and optimizing operational efficiency, a new paradigm is emerging at the intersection of closed loop quality systems and AI-driven machine vision. This integration promises to transform the way manufacturers approach quality control, offering unprecedented capabilities that go beyond traditional inspection methods.
The Evolution of Quality Control in Manufacturing
Quality control has been a cornerstone of manufacturing since the industrial revolution. However, the methods and technologies employed have undergone significant transformations over the last several decades. From manual inspections to statistical process control, and now to AI-driven vision systems, each evolution has brought new levels of precision and efficiency to the production line.
The Limitations of Traditional Approaches
Traditional quality control methods, while effective to a degree, often suffer from several limitations:
Reactive Nature: Issues are typically identified at the end of line, leading to waste and potential customer dissatisfaction.
Inconsistency: Human inspectors can be subject to fatigue, bias, and varying levels of expertise.
Limited Data Utilization: Historical quality data is often underutilized or difficult to access for predictive analysis. What data is utilized usually comes in the form of quarterly reports or spreadsheets.
Isolated Systems: Quality control processes are frequently disconnected from other manufacturing operations, creating silos of information. The data on these systems is often difficult to transfer.
These limitations have presented challenges to the transition towards Industry 4.0, and spurred the development of more sophisticated quality management approaches, with closed loop quality systems emerging as a pivotal strategy for innovative manufacturers.
Understanding Closed Loop Quality
Closed loop quality is a comprehensive approach to quality management that uses connected factory devices to create continuous feedback and improvement throughout the manufacturing process. Unlike traditional quality control methods, closed loop systems enable real-time adjustments and proactive problem-solving.
These adjustments can take different forms. Quality control systems can emit job orders to line operators with appropriate corrective measures. Closed loops systems can also drive adjustments automatically based on AI signals. State of the art manufacturing lines will leverage both approaches.
Key Components of Closed Loop Quality Systems
Real-Time Data Collection: Continuous monitoring of production processes and product quality with sensors throughout the line.
Integrated Analytics: Advanced data analysis tools that identify patterns and trends invisible to operators on the floor.
Automated Feedback Mechanisms: Systems that can automatically adjust production parameters based on quality data and sensor feedback.
Comprehensive Traceability: The ability to track a product’s entire lifecycle from raw materials to final delivery.
By implementing these components, manufacturers can create a dynamic quality control environment that is responsive, predictive, and continuously improving. A fully integrated manufacturing environment can identify potential issues before they escalate into critical faults.
The Role of AI-Driven Machine Vision in Closed Loop Quality
While closed loop quality systems provide a powerful framework for quality management, the integration of AI-driven machine vision takes this approach to new heights. Machine vision systems, enhanced by artificial intelligence and deep learning algorithms, offer capabilities that far surpass traditional inspection methods.
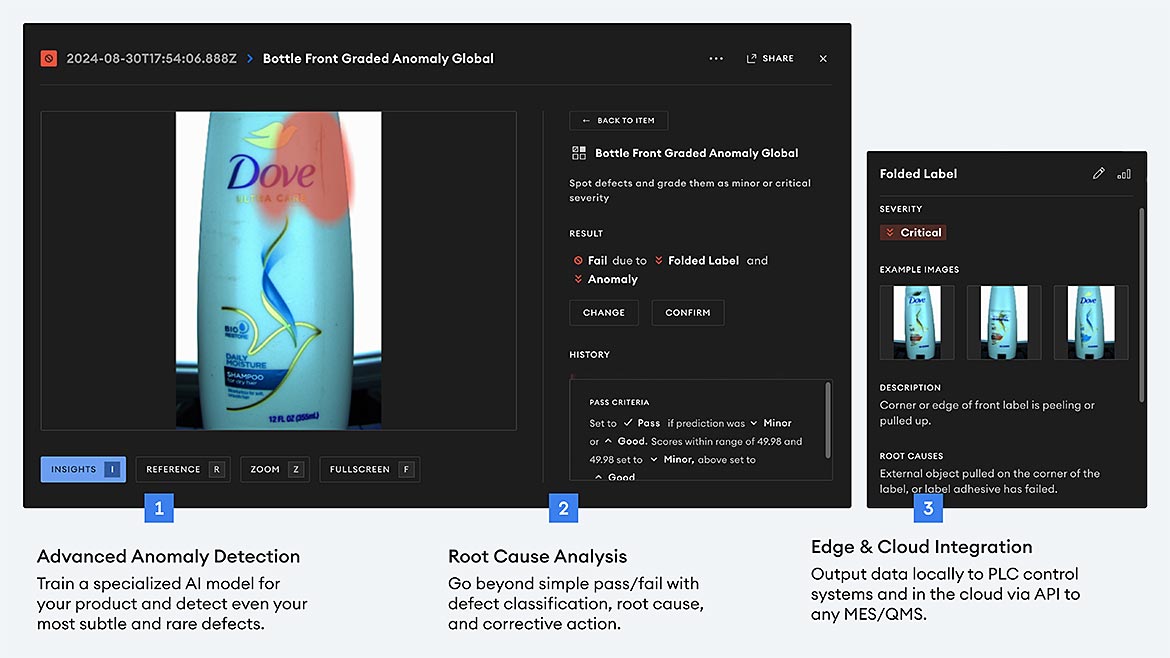
Advantages of AI-Driven Machine Vision
Robust Defect Detection: AI systems can detect subtle defects that might be invisible to the human eye or traditional vision systems.
Consistency: Machine vision systems maintain consistent performance 24/7, without fatigue or variability.
Speed: High-speed cameras and powerful processors enable real-time inspection of fast-moving production lines.
Adaptability: Machine learning algorithms can be trained to recognize new defects or product variations quickly.
Data Gathering: Every inspection generates valuable data that can be used for analytics and process improvement.
Integrating AI Vision into Closed Loop Quality Systems
The true power of AI-driven machine vision is realized when it is fully integrated into a closed loop quality system. The integration of the two technologies enables a quality workflow with significant benefits to manufacturers.
The Integrated Workflow
- Continuous Inspection: AI vision systems monitor products at multiple stages of production, collecting performance data of all processes.
- Real-Time Data Analysis: Inspection results are continuously evaluated for anomalous trends or spikes.
- Automated Adjustments: The system automatically adjusts production parameters to address quality issues. These systems can generate work orders for operators or technicians.
- Predictive Maintenance: With sufficient data analyzing defect patterns, the system can predict equipment failures before they happen.
- Comprehensive Reporting: Quality managers receive detailed reports and analytics, enabling data-driven decision-making.
Case Study: Process Improvement from Connected Quality Systems
Elementary installed a set of six vision inspection systems for a large toilet paper manufacturer in a facility in North America. Elementary validated the feasibility of the application in their test lab in Southern California and then deployed the first system to begin data collection.
Installation and Model Training
Elementary worked closely with factory quality engineers to ensure images of products, both good and defective, were properly labeled. This process is critical to produce an accurate and robust AI model. In under a week, the team trained and deployed a production ready model.
After the success of the first installation, the manufacturer proceeded with the next five systems. The SKUs and environment were the same across all lines, allowing the five systems to come online and detect defects in just a few days.
Finding the Error
While most systems showed less than a 1% defect rate on average, the manufacturer reported an anomaly on one of their production lines. Operators on the line found that one of the Elementary systems detected a 22% failure rate. While many factors could affect the accuracy of the model, Elementary Support confirmed that the results were accurate. Each data point was supported by an image of a defective product.
With this renewed certainty, the manufacturer looked upstream and discovered that a maintenance issue in the packaging machine caused the large failure rate. Operators were previously unable to detect the issue given the subtle nature of the defects.
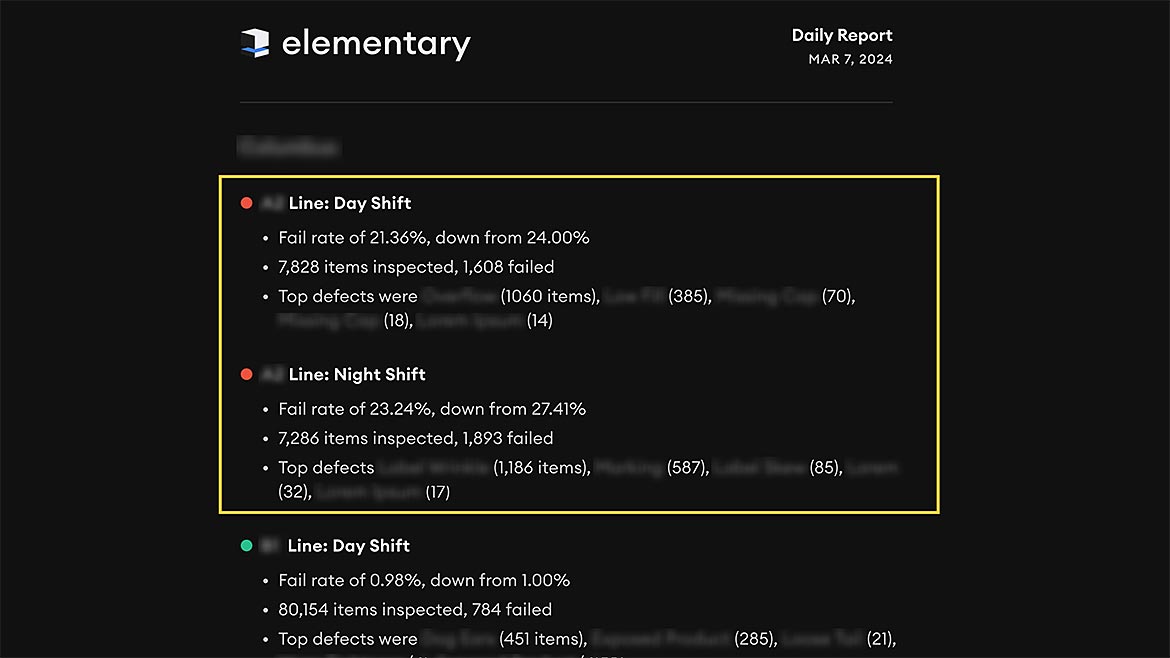
Key Takeaways
These inspection systems provided immediate ROI by uncovering a consistent production issue. This issue would have resulted in customer complaints and damage to the manufacturer’s brand. The closed loop system prevented this from occurring.
Using cloud connected AI-driven machine vision technology, Elementary was able to find the defects, analyze the trend, and empower workers to communicate the severity and extent of the issue to find a quick resolution.
Challenges and Considerations
While the benefits are significant, implementing a closed loop quality system with AI vision can present challenges:
- Initial Investment: The upfront costs for advanced vision systems and data infrastructure can be substantial.
- Data Management: Handling the large volumes of data requires robust IT infrastructure and expertise.
- Workforce Adaptation: Employees need training to work effectively with new systems and interpret AI-generated insights.
- Integration Complexity: Seamlessly integrating AI vision into existing manufacturing processes can be technically challenging.
Given these challenges, it is recommended that manufacturers work with an experienced solution provider.
Driving Quality Innovation
The integration of closed loop quality with AI-driven machine vision represents a paradigm shift in manufacturing quality control. Manufacturers can continuously improve processes, predict issues before they occur, and drive higher quality and innovation.
For operations managers, quality control experts, and manufacturing professionals, embracing this integrated approach is a necessity for staying competitive in a demanding global market. The future of manufacturing quality has arrived—it’s intelligent, interconnected, and adaptable
The manufacturers who leverage these technologies will lead their industries and set new benchmarks for quality and efficiency. The journey towards a zero defect world is ongoing, but with closed loop systems and AI vision, we have never been better equipped to pursue it.
Looking for a reprint of this article?
From high-res PDFs to custom plaques, order your copy today!