Software
Data Diversity: A Connected Approach to Quality
It’s time to unlock the potential of metrology data.
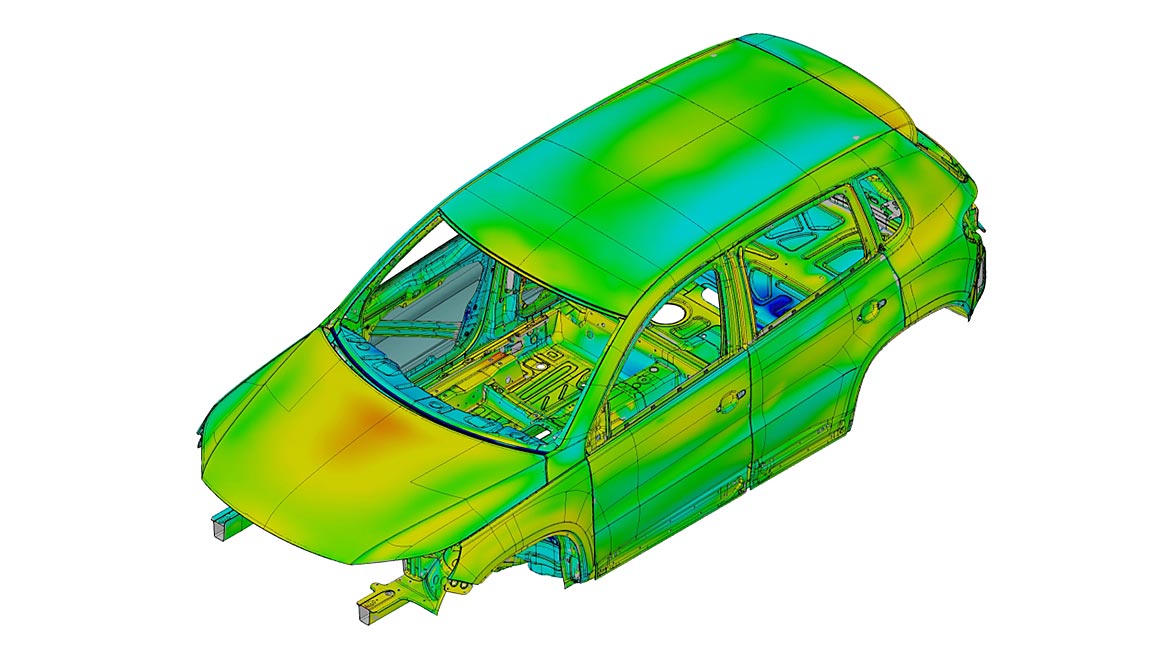
With 3D measurement data inside ZEISS CONNECTED QUALITY software, manufacturers can virtually construct assemblies to analyze parts for form, fit and function before they ever physically leave the factory. Image Source: ZEISS Industrial Quality Solutions
Along with all the innovation surging throughout the modern world comes the need to be agile. Designing and producing new parts with new methods opens the door to unpredictable challenges as new processes are developed. To adapt, manufacturers need the ability to modify parts quickly, which means reworking the CAD and adjusting the measurement strategy and inspection plans at any given moment. However, oftentimes, many people edit the same inspection program for different reasons and have difficulty maintaining changes, leading to costly miscommunication that breeds cultural issues, wastes time, and ultimately defeats agility.
A method of tracking, managing, approving, and documenting when and why changes were made is essential to plan, align, and execute faster so that teams and stakeholders know what to do and nothing is left to chance. With a connected approach to quality inspection, manufacturers maintain the accuracy of the diverse data and systems they work with in a single hub to foster a collaborative manufacturing environment that increases productivity to keep pace with innovation.
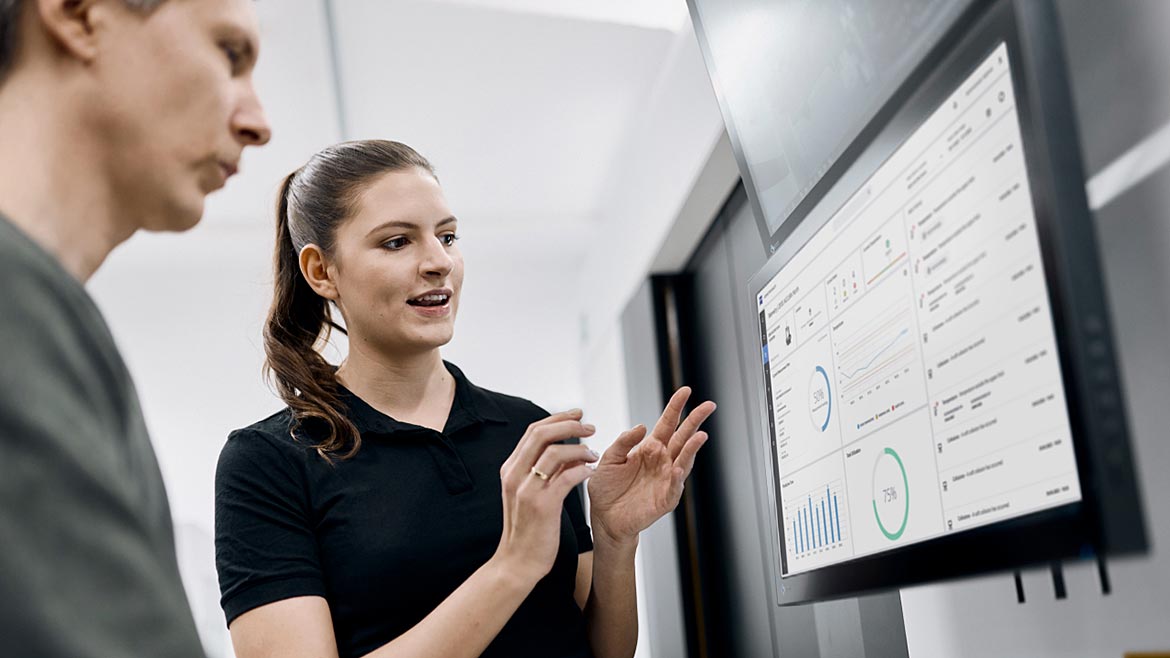
ZEISS CONNECTED QUALITY software connects measurement processes through an intelligent workflow management system to break down silos and replace them with transparent communication.
| Image Source: ZEISS Industrial Quality SolutionsBreak Down the Silos to Streamline Collaboration
Silos often exist because of a lack of transparency and communication, resulting in a lack of collaboration. From disagreements between metrologists, operators, and production workers, to miscommunication that results in costly mistakes, silos hurt efficiency and growth. In global manufacturing settings, these silos are even more distinct due to varying time differences, languages, and work cultures.
By connecting local or global measurement processes through an intelligent workflow management system within advanced quality inspection software, manufacturers can break down these silos and replace them with transparent communication. With this method, inspection plans are accessible centrally rather than locally or in confusing network environments. Not only does this interconnectivity make maintaining version control easy to manage, with clear roles, responsibilities, and transparency, but it also ensures operators have the latest updates and can easily understand which version is the current program.
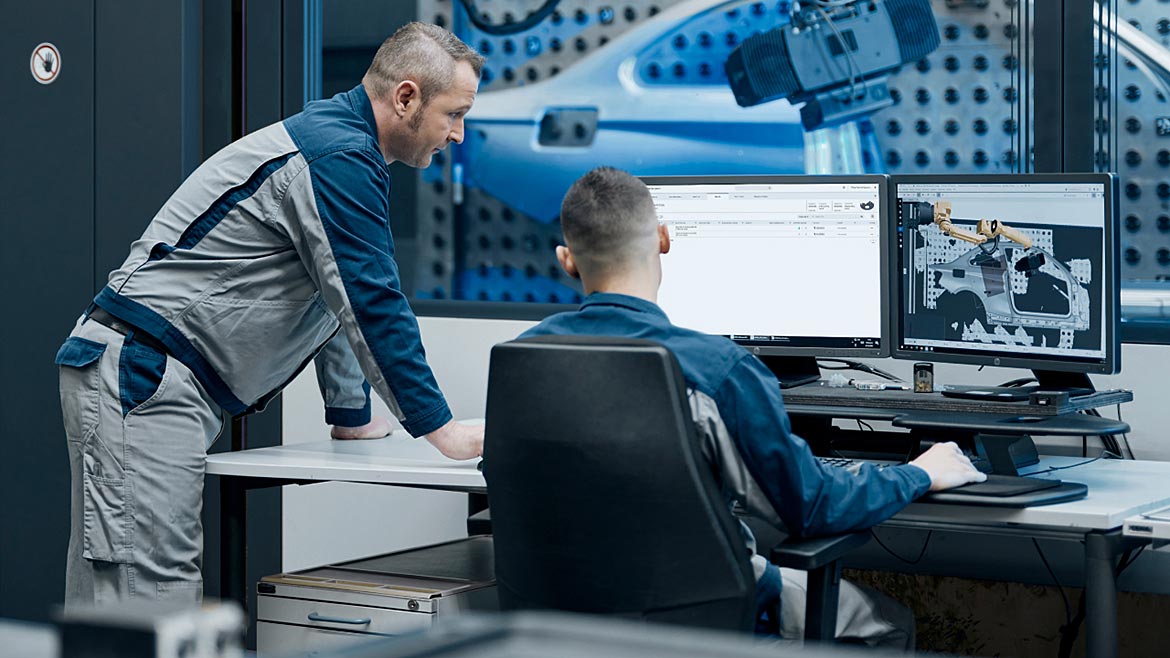
Connecting metrologists, operators, and production workers within the same plant or around the world with instant and easy-to-understand communication promotes transparency and increases collaboration.
| Image Source: ZEISS Industrial Quality SolutionsFor example, a metrologist in one location creates an inspection plan; then, the advanced quality software automatically syncs the inspection plan to an intelligent workflow management interface where inspection plans are approved and pushed for rollout. Operators in another plant instantly receive the notification that the inspection plan has been approved and executes it at their factory. Then, the operator approves the results, and they are uploaded back into the software for the original metrologist to release.
This efficient and streamlined workflow process unlocks the connectivity needed to be agile. Operators receive an easy-to-read timeline to quickly see the status of the inspection plan, and real-time notifications keep everyone on the same page regardless of location. Connecting metrologists, operators, and production workers within the same plant or around the world with instant and easy-to-understand communication promotes transparency and increases collaboration.
Instilling Trust that Boosts Productivity
Trust is a common human problem, especially when working in a complex manufacturing setting. Trust is knowing that the process is reliable. Trust is also believing that team members show up to do their best in the specific role for which they are accountable. When the process is unclear, accountability is too, resulting in lost trust and loss of energy and productivity from teams.
A connected quality software approach can improve work culture by providing clear processes and roles along with an audit history for transparency. Accountability becomes a fact, not an argument, when the roles are assigned, including who has the rights to create, modify, and approve inspection plans. Management of these roles and strict rules create a secure environment where measurement results are stored securely in accordance with company, industry, or regulatory requirements. This approach even enables the monitoring of measurement systems, including utilization rates and when and where to push and pull data.
Transparency is further supported by an audit trail that allows manufacturers to see who made what changes and when. This level of accountability changes the dialogue within organizations – reclaiming time lost to blaming others and keeping teams in a solution-focused mindset. With all this information in a centralized location, it becomes a single source of truth, empowering manufacturers to provide clearer roles, processes, and transparency that instills trust to boost productivity.
A Single Source of Truth for Metrology Processes
A single source of truth is critical to be proactive instead of reactive to unknown challenges. Seeing, executing, and analyzing quality processes, metrology data, quality factories, and machine data in a single hub enables deeper insights into quality processes from a bird’s-eye view down to a more granular view. Manufacturers can access trend analysis on various parts from different factories to understand the health of their processes or view incoming inspection on supplier parts to analyze which vendors in their supply chain thread are having issues. Having a technology-independent solution gives more insight into measurement equipment, including run-time, downtime, and operator performance, further supporting agility by providing the information needed to make quick shifts within quality processes while maximizing Overall Equipment Effectiveness (OEE). Syncing quality data to MES/ERP platforms further elevates a company’s ability to plan and monitor its entire processes more accurately. AI features and predictive maintenance enable manufacturers to minimize downtime, giving manufacturers the competitive advantage needed to thrive in an unpredictable manufacturing climate.
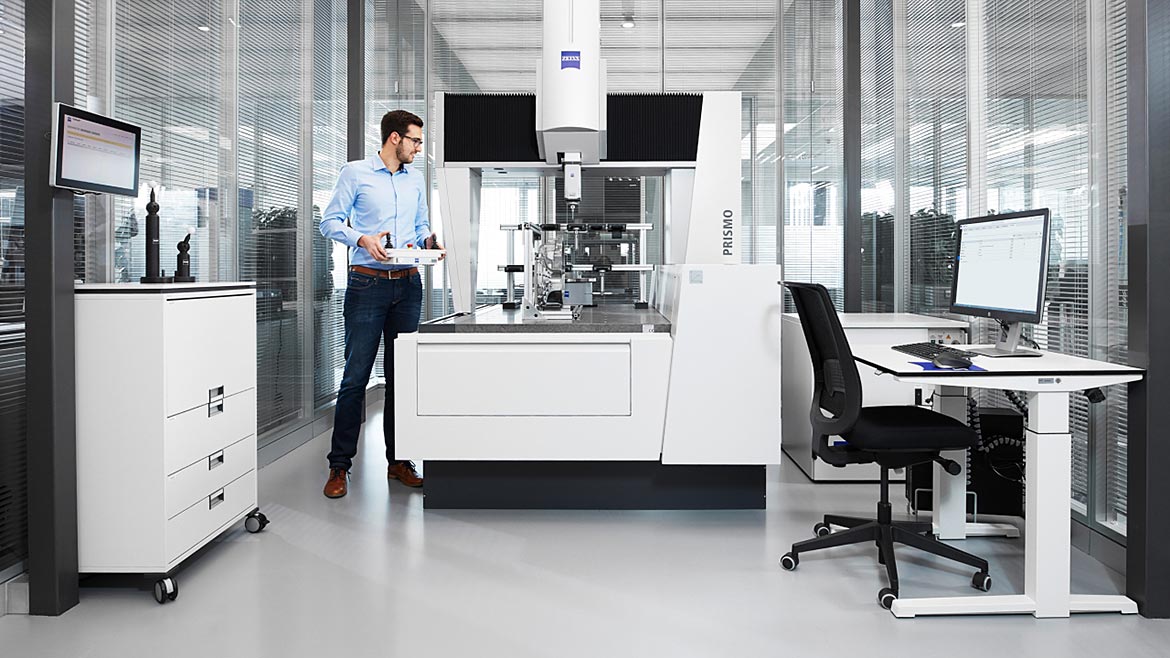
ZEISS CONNECTED QUALITY software enables the monitoring of measurement systems, including utilization rates and when and where to push and pull data.
| Image Source: ZEISS Industrial Quality Solutions3D measurement data within advanced quality software can also be leveraged to implement a digital twin strategy that improves efficiency through proactive inspection and analysis. Known as digital assembly, this method uses accurate digital twins of physical parts derived from 3D measurement data to virtually construct assemblies. With this method, manufacturers can analyze parts for form, fit and function before they ever physically leave the factory. With deeper insights from reliable data, teams can collaborate proactively and effectively on the necessary changes and adjustments before incurring additional production and shipping costs. This advancement uses digitalization to save time and money and promotes decarbonization through efficiency.
Tough decisions depend on having the right data that directs where to shift part production and quality assurance depending on the supply chain climate and available local capacities and capabilities. But simply having the data is not enough if it is kept in silos, inaccessible to those who need it to see the full picture. Manufacturers need a solution that truly connects quality processes to provide deeper insights, meaningful collaboration, and increase productivity. An intelligent centralized data management system offers a solution, serving as a hub for quality processes and orchestrating measurement plan workflows while pushing and pulling data worldwide for reliable analysis in real time.
This connected quality software approach establishes a single source of truth for metrology processes, allowing organizations to be agile when faced with unpredictable challenges. By enabling manufacturers to manage inspection, monitor measuring systems, and access raw machine data across an organization’s ecosystem, they are empowered and connected in quality processes across all dimensions. It’s time to unlock the potential of metrology data.
READ MORE
Looking for a reprint of this article?
From high-res PDFs to custom plaques, order your copy today!