Other Dimensions
Bore Measurement
A brief overview of popular instruments used to measure bores.
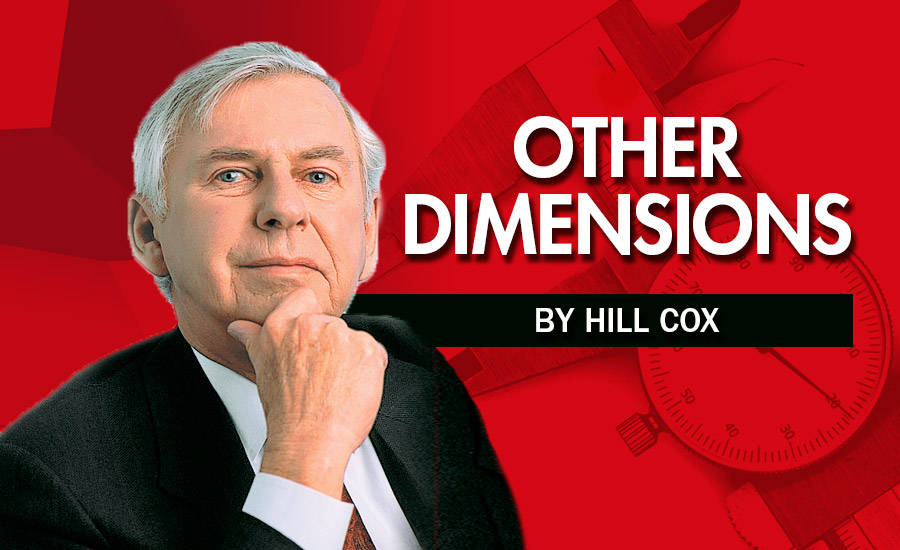
This is part three of a three-part series.
These two choices for bore measurement come into play when close tolerances are the order of the day and speedy, repeatable measurements are required in a production environment. Keeping these requirements in mind, instrument makers usually offer options such as hard chromed bodies or carbide pads and contacts where needed to keep wear at a minimum.
Since both types are used for close tolerance work, their speed of use can be compromised when large diameters are involved. These conditions can make insertion of the plug into the bore being measured awkward and slow. Makers of both types offer options to assist the user in such cases by providing a taper on the front of the plug or an easy entry pilot ground into the body.
AIR PLUG GAGES
These devices are so simple even I can use them easily which makes them great for production inspection using semi or unskilled inspectors.
As their name implies, these are plug gages through which controlled compressed air flows out of small jets to contact the wall of the bore being measured. The faces of the jets are often recessed in the body of the gage protecting them from wear to ensure their diameter relationship relative to the bore being measured is maintained. There are no moving parts at the business end of an air plug gage, only the air moving through it which means they can be produced to measure very small bores. A side benefit of these ‘jets’ is the cleaning action they provide while measuring.
An air plug gage may have an indicating system built into its handle or be connected to a display via flexible plastic tubing. In the past, the displays were mechanical with converters available to provide electronic or digital displays. Today, many use multi-range digital displays with outputs eliminating the need for converters.
The downside of these systems is their limited measuring range of a few thousandths of an inch and their cost. Each is custom-made for a specific diameter and one or two ring gages are required for setting purposes. Since they don’t actually have to touch the work to measure it—the air does that—their ‘contact’ area is equal to the diameter of the jets, typically about .040” or 1mm. Special jet sizes or configurations are available to enable air plugs to measure diameters very close to the bottom of blind bores.
Since air plug gages sense the bore over an area, their answers as to size may conflict with devices that do contact the bore such as dial or digital bore gages and electronic plug gages or coordinate measuring machines. Sensing over an area means variations in surface finish in that area are averaged by the flow of air. Generally, this will not cause problems using open jet air plugs if the surface finish is better than about sixty microinches.
ELECTRONIC PLUG GAGES
These gages are often referred to as ‘measuring’ plug gages since they look a lot like their fixed limit counterpart. The body of the gage is machined to a specific diameter just below the smallest acceptable part size to help keep it aligned while the actual diameter being measured is contacted by a contact points protruding from the body. The operating mechanism is similar to traditional bore gages or the split ball type.
The display of measured size for these gages can be a traditional or digital indicator or electronic probe and display when preferred. In the latter case, faster response time compared to air systems makes them ideal for automated applications.
Greater measuring ranges compared to air plug gages make these gages a preferred choice especially when parts have to be measured to coarse tolerances during a roughing stage of manufacture then a finishing operation to closer tolerances. Often one gage will accommodate both situations.
Correlation of results between electronic plug gages and other two-point system is quite good assuming the other system is equal to the precision of the electronic gage.
Like their pneumatic counterpart, electronic plug gages are made to suit specific sizes and tolerances and are set up using a dedicated ring gage.
The last three columns have provided a brief overview of popular instruments used to measure bores. I hope you found them interesting and perhaps worth saving for the next time you have to make such a choice.
Looking for a reprint of this article?
From high-res PDFs to custom plaques, order your copy today!