Making vs. Measuring
This was a judgment call based on experience and studies.
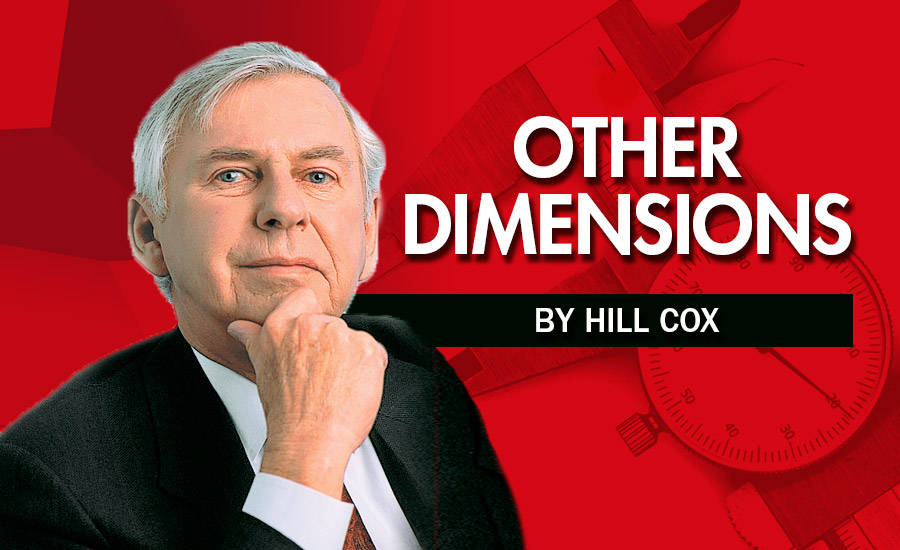
Gage manufacturers and calibration laboratories often find themselves in this minefield. New gages or instruments are supplied or calibrated and immediately returned by the customer because they aren’t correct. This claim is made because the new equipment is rejecting parts—parts that have been continuously produced for twenty years or more without problems. How can you argue with that kind of history? The short answer is that you can’t, but you can argue what that history means even if it is supported by reams of data.
Invariably these situations arise for a couple of reasons. The first is that while repeatability is a requirement of accuracy, it is only a component of it. The second is that the tolerances being claimed have never been met for one reason or another but those tolerances were unrealistic in the first place so the parts would still work if they were outside the tolerance.
This could happen due to a ‘sludge factor’ that reduced the required tolerance—an allowance that made up for real or perceived manufacturing variability. Of course, this was an engineering judgment call based on experience and studies. Now, we have computer programs that can crunch data six ways to Sunday but they have one fatal flaw: they’re non-thinking data processors. What the numbers mean is irrelevant to them.
At the end of it all it is not uncommon for component part features to have tolerances on them a gage maker would have trouble meeting. But in a world insisting on more zeros behind the decimal point, the ‘need’ becomes an article of faith from the altar of the hard drive. And it carries on to the point at which gages and/or instruments are selected to confirm the faith. This often means requests for equipment whose performance characteristics are not readily available—if they ever will be.
Design engineers aren’t the only folks that may use a sludge factor. The practice is often followed when selecting equipment to measure or control dimensions. In this situation, overly accurate measuring instruments, masters and gages are ordered at high purchase cost, and higher maintenance costs. Some justify this as extra insurance to ensure realistic drawing tolerances will be met.
Precision costs money—unnecessary precision costs even more. The tolerance for a plain plug gage to XX tolerance is one half that of a gage to X tolerance so it costs more. If used for production inspection, it will cost more in calibration costs because it will have to be checked more frequently than a class X and will need to be replaced much sooner when it wears out of limit.
When measuring instruments are involved, if you select higher accuracy and resolution than you really need, the dancing digits will keep inspectors pulling their hair out. The ‘insurance’ you thought you were getting in all of this is lost when they are used in a typical shop environment or, in some cases, by staff with inadequate skills.
Setting masters for measuring instruments are often specified to higher accuracy than is needed or practical at a resulting higher cost. Often a lower level of accuracy that has been calibrated will give you a master with all the accuracy you could ever need when the instrument is set to the calibrated value. The accuracy of the calibration will usually be better than the tolerance the master was made to.
You should be aware that some of the ‘standard’ gage maker tolerances seen in catalogs or on websites are not always achievable due to the state of the art. Setting rings closer than X tolerance are an example of what I mean. If you insist on buying them, don’t be surprised if you get different numbers from different labs when they are calibrated. If fact, some makers will advise folks trying to buy them that the maker’s readings will be considered as the final word on their size or they won’t accept the order. They know what the state of the art is and what it means in practical terms.
Design engineers have to work with production engineers and quality engineers and if all goes well, somewhere along the way someone with metrology knowledge will be involved. At the end of the day, if the metrology isn’t right, nothing else will be.
Looking for a reprint of this article?
From high-res PDFs to custom plaques, order your copy today!