Flies in Dies: Spending a Little Money to Save Bigger Costs and Time
They needed to get the flies out of the plant.
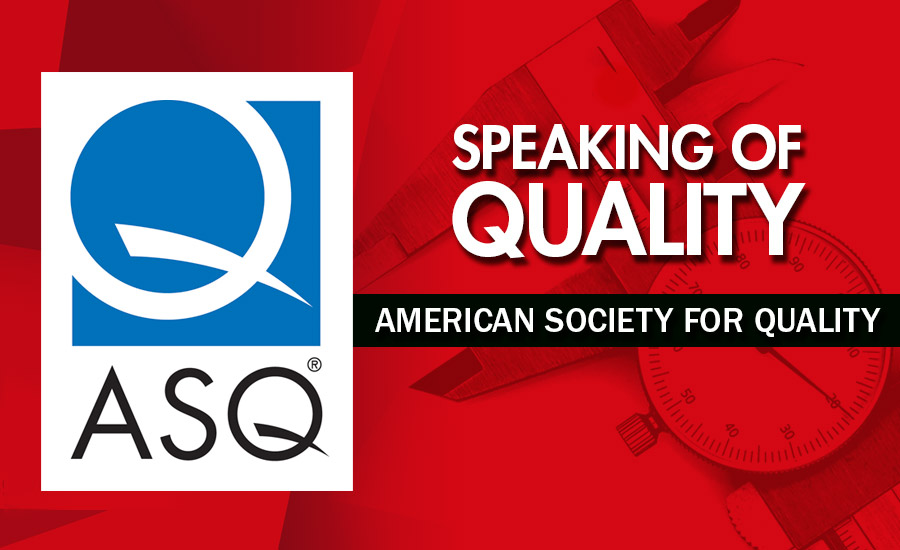
Today it is a vacant plot. Back in the early 1990s, a stamping plant was there, with three main buildings supplying North American automotive final assembly operations. I was an inspector working the second shift, assigned to a stamping line producing outer panels for an automotive door.
While inspecting panel surfaces one hot summer day, I noticed an odd pattern. When a defect occurred in the outer panel surface on one panel, it was followed by a defect at a lesser degree at the same location on the next three panels. A total of four panels were scrapped at a cost of $50 each. This pattern repeated throughout the night, which meant that each event cost the company $200. Because this was long before I knew about Six Sigma, I planned to just use root cause analysis. I had already determined the four rejected panels were not random. But what was the common cause?
Turning the first panel over to inspect the inside surface, I found a dead fly on the metal. The defects on the other panels were from fly parts remaining on the die. I had now determined the defect cause but not the root cause.
To find the flies, I walked to the start of the press line where I expected to see flies flying through the stamping die. The operator saw me looking around and told me the flies were already in the steel. I inspected the steel blanks. Sure enough, I found a fly in between the steel blanks. I needed to visit the blanking press operation in the back of the plant.
I arrived at the blanking press and immediately started looking. No flies. The blanking operator told me that if I wanted to see flies to come back at 8 p.m.
The plant was old, dating to the 1920s, if not earlier. Because it was a hot night, windows were open. There were also broken windows throughout the plant. In addition, the loading dock doors were open to get night air in to cool the plant. And we were located near a river and the local water treatment plant.
At eight o’clock I returned to the blanking press. There were flies everywhere. A light was centered over the press, and the flies buzzed around the light. Some would hit the light and fall into the blank immediately covered up by the next blank.
I took my findings to management. The response was to stop running the blanking press during the night shift. I pointed out that, as production schedules got tight, they would need to return to running the press during second shift. To properly fix the problem, they needed to turn off or relocate the light, repair the broken windows, and close the other windows and doors. They needed to get the flies out of the plant.
However, I could not get management to act on any of my ideas. Out of frustration, I said, “Don’t worry, the problem is intermittent and will go away by itself.” For a moment, I had management’s attention again. “What do you mean?” they asked. I told them that winter was coming and the flies would go away until next summer.
For a few weeks production ran on day-shift only and then again included second shift. The flies-in-the-dies came back. I left the company a few weeks later. Had I stayed I would have found a way to create change.
I thought what I had witnessed was a one-of-a-kind problem until I came across a case study about flies getting into food wax packaging. The root cause of that company’s issue was manufacturing in an old plant with broken windows. They repaired the windows. The flies stopped getting in the plant.
To make any lasting change, you need management support. And management needs to listen to the people working the process, because they know the process best. Once you determine the root cause, using formal corrective action programs (like 8D) helps improve the process.
Problems, even the hard ones, can be solved. You just need to get the “flies” out of your processes.
Looking for a reprint of this article?
From high-res PDFs to custom plaques, order your copy today!