Help with Measurement Problems
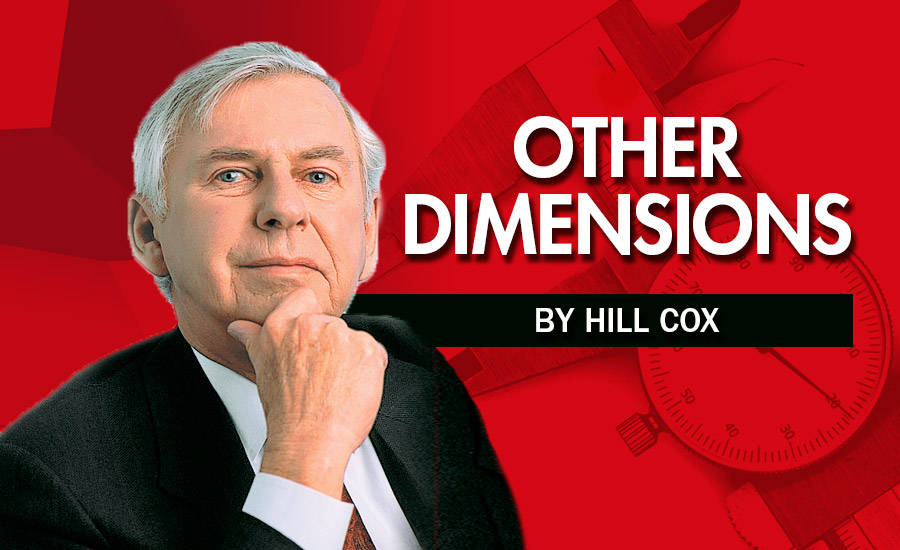
I offered some comments that relate to gaging problems in the last column but thought it would be worth giving measuring instruments the same treatment.
In general terms, fixed limit gages are used to ensure parts made within prescribed limits will assemble. When it comes to actual size measurements, a lot of additional factors come into play one or more of which can indicate that what appears to be the best instrument for the job won’t work well at all. Here’s a list of some of the factors and/or questions you need the answers to in order to make a good choice.
TOLERANCES
The precision required of a measuring instrument to meet the tolerances a measurement is required to verify will be determined by the tolerances. The resolution of a particular instrument is not an indication of its precision no matter how many digits are in the display and is not a reliable indicator of its performance. Someone experienced in dimensional metrology should review the tolerances involved to determine what devices have a reasonable chance of doing the job—all other factors being equal.
WHERE THE DEED IS TO BE DONE
The actual environment in which the measurements are to be made can be the most critical factor—especially the temperature. The ambient temperature is one thing but if the work is to be measured immediately after machining, this must be allowed for. And if measurements are required during machining, other problems can arise regarding handling the measuring instrument in addition to temperature problems.
WHICH END IS UP?
Orientation of the axis of the feature to be measured can mean an otherwise excellent choice for the application will not work precisely enough for the situation. Typical of this are long bore diameters that must be measured while their axis is horizontal. Even short bore measurements can have problems if the instrument requires careful manipulation such as centralizing to produce reliable readings.
WHO/WHAT WILL DO IT
Despite the wonders of digital instruments, they require human (or robotic) handling to provide meaningful readings. Human skills are the most variable and the need for high skill levels increases as the tolerances decrease. Robotic handling also requires proper positioning/sensing abilities for the same gains and while offering high repeatability, may not be as reliable as a similar device used by an experienced machinist or inspector.
IS THE CALIBRATION RELEVENT?
Instruments and masters used with them may have a current calibration report but it can be of little value if not done thoroughly. If the instrument was calibrated by a device with flat anvils but it is being used to measure a feature with cylindrical surfaces or vice versa, measuring contact geometry can introduce errors. A review of how a device was calibrated can reduce the impact of these conditions.
HOW MUCH TIME HAVE YOU GOT?
Some instruments require more time than others to be used effectively and this can be a challenge when measurements are being made in a production situation. In some cases this is due to manual use of the device, in others, response time of the device may not be suitable even though it is part of an automated setup. A trade-off may be required to obtain the desired degree of precision for the application.
CLEANING UP YOUR ACT
Hand tools such as micrometers and calipers are regularly being promoted with claims they meet some standard or other that enables them to be used with machine coolant splashing all over them. Impressive as this may be, if you want precision, don’t use them under such circumstances where you could be measuring over dirt or bits of metal, or grinding dust, etc. Cleanliness improves your precision every time whether it’s the instrument or the item being measured.
AN UNCERTAINTY BUDGET?
Calibration laboratories prepare uncertainty budgets in their work so readers of their reports can get a sense of how reliable their processes are. You should consider doing the same for instrument selection because a lot of guesswork and personal preferences are taken out of the decision when it is based on a number of factors reduced to common denominators. Some factors will be common to all devices (such as temperature) while others will vary. In the end, a lot of arguments can be avoided when the selection is based on budgets for the different instruments being considered.
Looking for a reprint of this article?
From high-res PDFs to custom plaques, order your copy today!