Analyzing Potential Failure
Failure modes and effects analysis is an effective method.
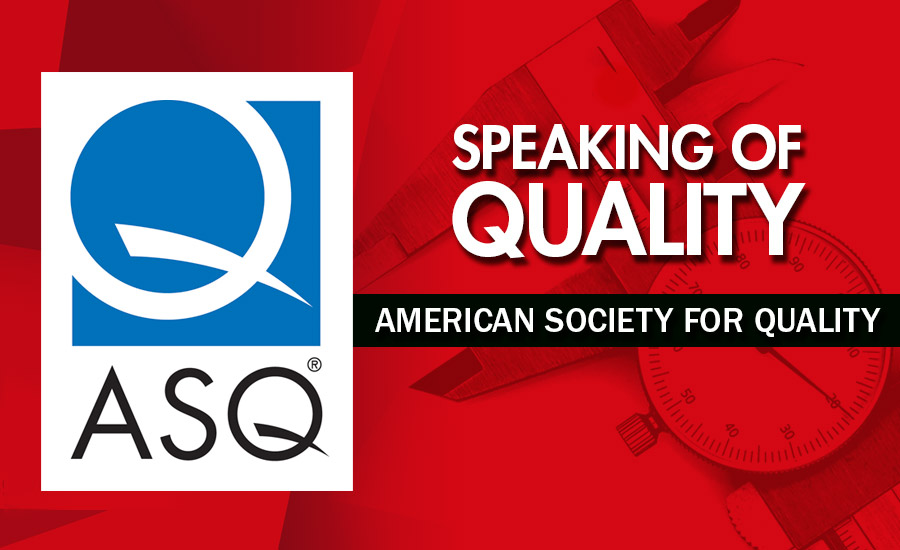
At the individual level, failure isn’t always a welcome event but it is recognized as a path to growth, innovation, and change. Prior to engaging in a particular endeavor, you can look at potential areas of failure and examine possible consequences. If the activity doesn’t involve death, divorce, or disaster—and with a little internal and external encouragement—you will go for it.
For the organization, however, failure is often viewed as lost product, wasted time, and, of course, squandered cash. This feeling—whether conscious, deliberate, or accidental—can create contradictory messaging to staff, causing confusion and leading to more lost time, product and, of course, money.
To keep your organization out of those situations, you need an approach to identify possible failures in design, process, and the product/service. Failure modes and effects analysis (FMEA) is an effective method to use. Developed in the 1940s by the U.S. military, it was further developed throughout the 1950s and has been used in U.S. manufacturing since. There are two “parts” to FMEA. Failure modes define the ways in which something (design, process, or product) might fail. Most important are the failures—actual or potential—that directly affect the customer. Effects analysis studies the consequences of each failure. The purpose of the FMEA is to take actions to eliminate or reduce failures, but the process also documents current knowledge and actions about risks that can be used in continuous improvement. Altogether the FMEA is used to prevent failures and, after design, used for control.
An important aspect of the FMEA is to be sure you are appropriately using the approach at the right time. Use the FMEA for a process, product, or service:
- When designed or redesigned, after quality function deployment.
- When being applied in a new way.
- Before developing control plans for a new or modified process.
- When improvement goals are planned.
- When analyzing failures.
- Periodically throughout the life.
Once you have identified FMEA as the correct approach (additional information can be found at asq.org/learn-about-quality/process-analysis-tools/overview/fmea.html and in “The Quality Toolbox,”
by Nancy R. Tague) you will want to:
- Select a cross-functional team with diverse knowledge of customer needs as well as the product/process/service.
- Identify the scope of the FMEA, using flowcharts to make sure every team member understands.
- Complete the identifying information at the top of your FMEA form. See sample figure below.
- Identify the functions of your scope.
- Identify the potential failure modes for each function.
- Identify all the consequences for each potential failure mode (potential effects of failure).
- Determine the severity rating, or S (rated on a scale from 1 to 10, where 1 is insignificant and 10 is catastrophic).
- Determine all the potential root causes, using cause analysis tools.
- Determine the occurrence rating, or O (rated on a scale from 1 to 10, where 1 is extremely unlikely and 10 is inevitable).
- Identify current process controls.
Determine the detection rating, or D, for each control (rated on a scale from 1 to 10, where 1 means the control is certain TO DETECT the problem and 10 means the control is certain NOT TO DETECT the problem).
Calculate the risk priority number, or RPN (RPN = S × O × D).
Calculate criticality (= S × O).
Identify recommended actions, noting who is responsible for the actions and target completion dates.
Note results—along with the new S, O, or D ratings and new RPNs—and the date on the FMEA form.
Failure can be disastrous for your organization. Failure can also be a way to innovate. Strategically analyzing potential failure can save money, improve product and processes, and lead to new ideas. FMEA is a powerful tool for your use. Go for it.
Looking for a reprint of this article?
From high-res PDFs to custom plaques, order your copy today!