Charting the process with the help of a turtle.
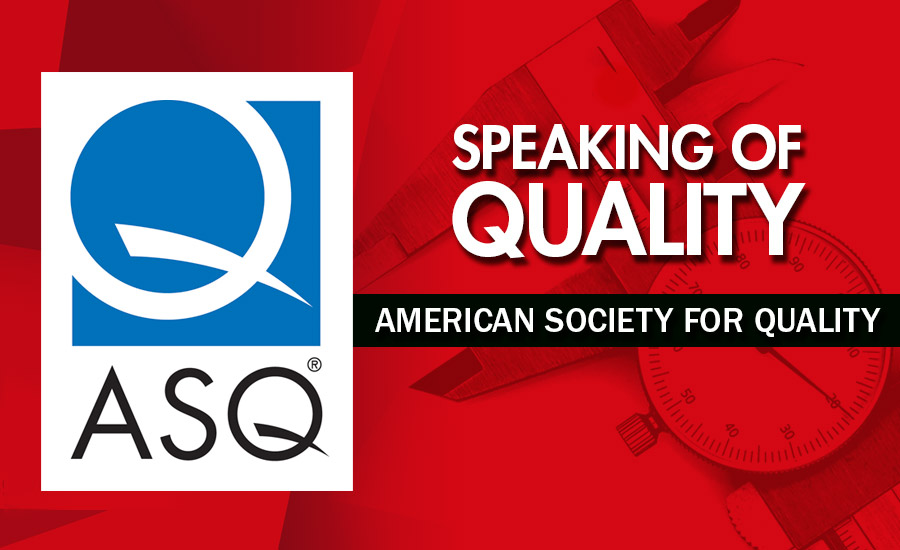
Map the process. Chart the process. Get the turtle! (?)
Undoubtedly, you have heard—perhaps spoke—the first two statements. You are in the business of process improvement, after all. You want to be sure you have an effective quality management system (QMS). Process maps and flowcharts are essential for your QMS. However, these tools are mistaken for the same tool and used interchangeably.
Now, about the turtle. In this case, the mention of the shelled reptile refers to the turtle diagram, a helpful tool often overlooked when developing flowcharts and process maps. The purpose of this article is two-fold to assist you get the most out of our QMS:
- Keep you from falling into the trap of equating process mapping with flowcharting
- (Re)introduce you to the turtle diagram and its unique use
Before we address the turtle, let’s tackle the maps and charts.
Flowchart ≠ Process Mapping
The most likely reason process maps and flowcharts are mistakenly seen as interchangeable is that they look similar and use many of the same graphic symbols. However, the goals of each are different.
A process map “is an essential technique,” writes Miriam Boudreaux in her article, “On the Map,” (Quality Progress, November 2010) “for identifying all the processes that take place in an organization, as well as their interrelation. This visual tool makes it easy to understand the sequence in which these processes take place.” A process map is detailed, yet easy to follow and includes the following components:
- Inputs
- Core processes
- Interactions shown by arrows
- Outputs
- Support processes
A process map then is meant to be of use to the company in a strategic way and to empower staff based on team and individual goals. The article “Knowledge Map and Process Map Overview,” published by APQC (October 2009), states that you should use a process map to:
- Ensure everyone understands the shared vision of a process.
- Provide an accurate snapshot of the process.
- Aid in identifying non‐value added tasks.
- Facilitate training of new employees.
- Determine where in‐process measures need to be used.
The following table helps differentiate the process map and flowchart in more detail.

From “On the Map,” Miriam Boudreaux (Quality Progress, November 2010)
And, Now, Here Comes the Turtle
It is time to add another helpful and efficient layer to the process. Turtle diagrams and flowcharts have both been used to graphically display a process for a number of years. In “Best of Both Worlds,” (Quality Progress, April 2011) Gene Granowicz explains everything a process turtle diagram identifies:
- Inputs: Includes internal and external customer requirements.
- Outputs: The process’s results.
- For a system process, this includes information, reports or data.
- For a manufacturing process, the outputs include the finished product, statistical data and other manufacturing-related records, as well as any scrap from the process.
- For any process, the actual output should represent the satisfaction of customer requirements.
- What: These are the non-human resources needed to perform the task.
- Who: These are the human resources needed to complete the process.
- How: This provides insight into the operational controls required.
- Measures: This is a listing of the performance indicators that will indicate the success or failure of the process.
Each of these items is visually represented in the turtle format.
As Granowicz explains, turtle diagrams are very useful for internal and external audits because they describe the inputs, outputs, and the means for measuring the process. The flowchart, while in some cases, addresses input and outputs, does not address measurement.
What can be helpful for your organization, is to combine flowcharts and turtle diagrams. By doing so, Granowicz states you have created a solid process map. This map can be rolled up into standards documentation.
Process maps, flowcharts, and turtle diagrams are three useful tools in your QMS. As you continue and strengthen your improvement efforts, be sure to explore each tool’s unique qualities.
Slow and steady. Keep the process improving.
Looking for a reprint of this article?
From high-res PDFs to custom plaques, order your copy today!