In Search of Precision Measurements
This is a new experience for many students.
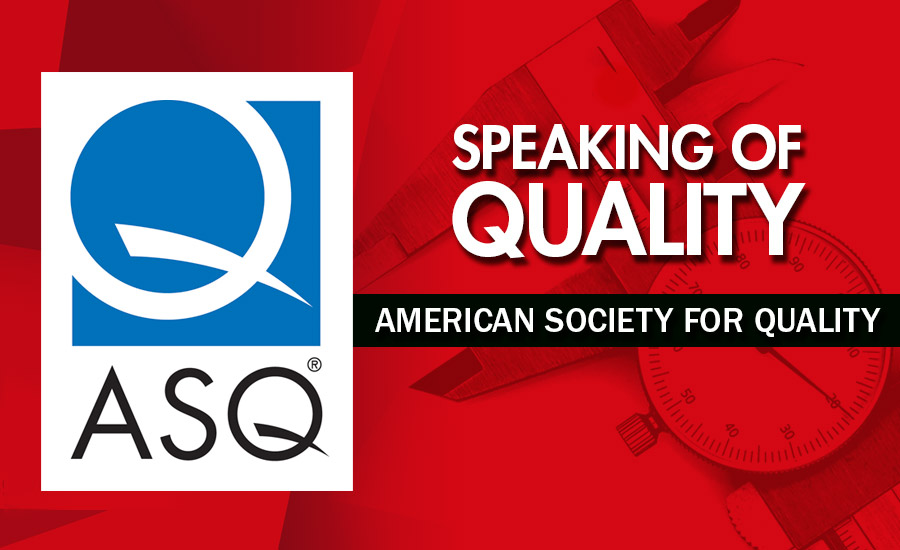
How big is big? How small is small? What is precision measurement?
I am in my tenth year as a part-time instructor at Western Michigan University, currently working with junior- and senior-level engineering students. I instruct the hands-on metrology lab of Dr. Pavel Ikonomov’s metrology class. We have about 15 weeks for this three-credit hour class to introduce metrology, focusing on precision measurement. We have about 45 students taking three hours of lecture and three hours of lab each week. These are the questions asked on the first day of lab:
- Where does precision measurement start?
- What is the smallest object you can see with an unaided eye?
- What is the smallest difference you can feel with your sense of touch?
I ask these questions because I want the students to get a sense of size. They struggle with the answers, partly because the class is new and partly because they never gave it much thought.
Precision measurement starts at .001 inch. A finer measurement is considered .0001 inch. I ask them, “How many thousandths are there in an inch?” I ask this question because my former employer included it on a test given to quality department candidates. As an inspector, I graded the inspection test. One person’s answer to “How many thousandths are there in an inch?” was memorable: “I don’t know, they are small, there must be a million of them.”
As my students and I gather around a surface plate, I ask about the difference in thousandths you can feel. Responses range from .050 to just a few thousandths. I place various gage blocks on the surface plate (.100, .101, .102, .103, .104, .105, .110 and .120). Placing the .100 block next to the others you can feel the difference. Your sense of touch can detect below .003 difference. The students get to see what one hundred thousandths looks like, and what .010 and .020 feel like. This is a new experience for many students.
We decide the smallest object you can see is dust, a grain of sand, or a human hair. So, I take one of my gray hairs and measure it with a digital micrometer at .0026. I comment that the standard human hair is about .003 and mine is thinner. We sample students’ hair, all get a chance to measure and all are thicker than mine. Most of the students do not know hair can be measured. They are starting to get a sense of size and the ability to measure to .001 of an inch.
This is a hands-on measurement lab. Students are in two-person teams and complete 15 assignments. This allows both students to compare their readings. I stress the part does not change so the measurements should be the same. Sometimes the measurements differ by .020. That is when I have them repeat the assignment to look for measurement errors and why the two are not within .001 of each other. It is new to them and they need practice.
We work with calipers and micrometers to start. Go and no-go gages, pin and thread gages and functional gages are used. We measure threads with the three-pin method and that is eye opening for the students. We have a new Faro Arm, and this year a new Zeiss CMM. We use surface plates, with height stands, dial indicators and gage blocks. We are using optical comparators, optical microscopes, and old Sheffield comparators. There are two larger projects, completing a gage R&R and then a capability study. To finish off the semester it is required to make a part to a provided geometric and tolerancing print, measure the part to the print tolerances and predict if it will fit the gage by the measurements they have recorded. Half the time the part does fit the gage and is in tolerance.
Another point I stress throughout the semester is to check precision instruments prior to use. Always check the zero setting and a few points in the range you are going to measure. I call this process verification and not calibration, which is a much more detailed process. Even if there is a calibration sticker on the gage, what have you done to confirm the gage is acceptable to use? I have had students tell me they never thought about that before. If a caliber was next to a machine, they would just use the caliper without checking. As a quality professional with four certifications (CMI, CQT, CQA, CQE), I understand the need for knowledge to progress a career. I encourage my students—and you—to look outside of the company and university for additional knowledge to improve yourself and your inspectors and join (and get involved in) a professional society.
Looking for a reprint of this article?
From high-res PDFs to custom plaques, order your copy today!